
Comprehensive High Services in Master’s and PHD Thesis Writing
مهر ۱۱, ۱۴۰۳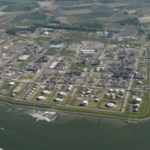
Training of Refinery Units
مهر ۱۱, ۱۴۰۳Sulfur Recovery Unit
Objective
The purpose of this sulfur recovery unit is to recycle acid produced in Unit 101. The feed input for this unit is sour gas from Unit 101, and the final product is liquid sulfur, which is sent to Unit 144 for storage.
Environmental Considerations
The establishment of this unit addresses environmental concerns by converting H₂S from the acid gas generated during the amine sweetening process into sulfur. Designed for daily production, this unit has a capacity of 400 tons with four trains. The core process consists of combusting acid gas through the Clauss process, which leads to the production of gaseous sulfur, followed by the liquefaction of sulfur gases using warm water.
This unit consists of three main sections, as follows:
1. Clauss Stage
This stage includes the reaction furnace, boiler, condensers, and catalytic reactors.
a) Reaction Furnace:
the reaction and thermal cracking occur at high temperatures.
- Air for combustion is supplied by air blowers. Before combustion, air and acid gas are preheated in separate heat exchangers (SH) and are subsequently heated again before entering the second and third reactors.
- b) Boiler and Condensers:
Using warm water, the produced sulfur is liquefied, and steam is generated. The produced vapors in the boiler and condensers are routed to the main steam line (i.e., we have steam production in the unit SL). The second and third condensers cool the vapor in air coolers and return it to the warm water line, with this steam being (barg 101) LLP. - c) Catalytic Reactors:
The conversion of H₂S occurs at lower temperatures in the presence of a catalyst.
2. Gas Dehydration Stage
The sulfur produced from the boiler and condensers is transferred to the gas dehydration vessel. Since H₂S is dissolved in sulfur, it must be removed, which is done through two circulating pumps in two dehydration sections with the injection of the liquid catalyst Aquisulf. The gases are then ejected using steam and through counter-current flow of air and sulfur from the liquid sulfur surface, leading to the upstream flow of the incinerator section. Sulfur is formed as polysulfides.
It is important to note that the permissible amount of H₂S must be maintained at ppm 10, which is continuously measured. The storage temperature for liquid sulfur is between C140 and C150. (If the temperature drops below C140, steam is injected, and if it exceeds C150, warm water is used).
3. Incinerator
The waste gases are ultimately directed toward the incinerator, where they mix with gases generated from the dehydration stage. In this step, the gases are burned by FG at a temperature of C800 and are released into the atmosphere via the stack.