
The Challenge of Water and Steam Waste in the Steel and Iron Smelting Industries
آذر ۹, ۱۴۰۳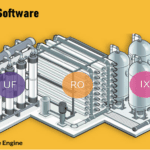
Reverse Osmosis and Water Treatment Design with Wave Software
آذر ۱۶, ۱۴۰۳Introduction
Laboratory scaffolding and design of clean rooms are among the basic components in modern science and industry. In today world, the accuracy and precision of work in research and industrial laboratories is of particular importance. The basic design of these spaces can have a significant impact on the quality of results, user safety and productivity improvement.
Proper implementation of laboratory scaffolding and cleanrooms not only helps to maintain accurate data and conduct relevant research. It also helps to preserve the life and health of users. Creating an effective project management process that includes all stages from design to implementation can guarantee success in achieving the set goals.
What is Laboratory Scaffolding?
Laboratory equipment and scaffolding are designed with the aim of preparing a suitable space as a work table and for placing devices, glassware, supplies and laboratory equipment. From the point of view of technical experts, the first step in setting up a laboratory is the proper design and implementation of laboratory scaffolding in a principled and correct manner. Safety and observance of technical principles in the implementation of scaffolding and laboratory cabinets are of great importance.
But at the same time, designing and creating an elegant and calm environment for research should not be ignored. The design and construction of durable and well-made platforms will make the laboratory space more favorable for laboratory staff and technicians. And of course, the qualitative and quantitative level of the provided laboratory services will also be improved.
Modern Laboratory Scaffolding Design
Nowadays, new laboratory equipments are produced in various sizes and shapes. Also, most of the equipment is made for use on various laboratory tables. Except for the equipment that is large and designed and projected to stand. New design and technology change, laboratory equipment in general had a significant impact on the growth and improvement of the design of laboratory tables. For example, some modern equipments are easier to use due to the way they are placed on two-sided and island tables compared to placing them on one-sided tables attached to the wall.
Laboratory Scaffolding Components
In general, laboratory scaffolding consists of three main parts: frame, top plate and cabinet (unit) and includes the following equipment: Laboratory platform
weighing table
sinks and faucets
Material storage cabinets
Partition
Types of Laboratory Scaffolding
One Sided Scaffolding
One-sided laboratory platform (one-sided laboratory table) is one of the most widely used types of platforms and cabinets in the laboratory environment. which, by installing on the side of the wall, provides the possibility of one-way use for employees. This model of scaffolding has different dimensions and sizes. However, according to laboratory standards, it is often made with a width of 60 to 80 cm and a height of 85 to 90 cm.
Also, the one-sided laboratory cabinet, which usually has granite stone, steel, epoxy resin, anti-acid ceramic and HPL (Formica) as its top, has the ability to install a sink, all kinds of laboratory faucets, electrical outlets, etc.
Two-Sided Scaffolding
The two-sided laboratory table is one of the other types of laboratory cabinets, which, by installing in the middle of the laboratory environment, provides the possibility of using both sides for employees. Based on the standard of laboratory scaffolding, this model of scaffolding often has a height of 85 to 90 cm and a width of 120 to 160 cm.
Also, this laboratory scaffolding, while having the ability to install a sink, all kinds of laboratory faucets, electrical outlets, etc., creates the possibility of using laboratory equipment and sinks bilaterally for users. And it usually has a top plate made of granite stone, epoxy resin, steel, HPL (Formica) and anti-acid ceramic. The material of the top plate of the platform is one of the important factors that determine the price of laboratory scaffolding.
Features of Laboratory Scaffolding
Stability and Safety
Flexibility and Adjustment
Organization and Efficiency
Versatility
Enhanced Visibility and Access
Chemical Resistance and Durability
Space Optimization
Compliance with Safety Regulations
What is Clean Room?
A clean room is an environment with controlled pollution of suspended particles in space, which contains a certain number of particles per cubic meter. These environments are used to produce products and perform activities that require high precision and quality.
Clean rooms are used in various industries such as pharmaceuticals, food industries, electronics and aerospace. Designing, purchasing and operating a clean room is a complex and multifaceted process that requires sufficient knowledge and experience. This process includes various steps such as determining the needs, designing the clean room, purchasing and installing the clean room equipment and setting up the clean room.
A room in which the concentration of airborne particles is controlled and constructed and used in such a way as to minimize the entry, production and retention of particles inside the room. Other relevant parameters such as temperature, humidity and pressure should also be controlled if needed. Therefore, a clean room is a space where the entry, production and retention of particles is minimized. This is mainly done in two ways:
1- Ventilation With Filtered Air
The air entering the clean room passes through very strong filters to dilute and remove particles and bacteria released from personnel and equipment. This air also pressurizes the room to prevent contaminated air from entering.
2- Use of Appropriate Materials and Equipment
The clean room is made with materials that do not produce particles and are easy to clean. The personnel of these rooms also use special clothes that largely prevent the spread of particles and microorganisms from their bodies.
In addition to particle control, cleanrooms allow temperature, humidity, sound, light, and vibration control. However, these parameters are not unique to the cleanroom. These features have made clean room design a specialized and special job.
Classification of Clean Rooms Based On Technology and Method Ventilation
Types of clean rooms are divided into the following two categories based on technology and ventilation methods:
Turbulently Ventilated
These types of rooms are also known as “non-directional” and their air flow is distributed randomly in the room. In these types of rooms, air exchange is usually done at least 20 times per hour or more, which is much more than air exchange in normal rooms such as offices. Also, in this style of clean room, the pollution created by people and machines is mixed and diluted with the incoming air.
Unidirectional Flow
These types of rooms, which were originally known as Laminar Flow, use a much larger volume of air than the turbulent type and provide much higher cleanliness. In the basic principles of a unidirectional air flow room, high efficiency filters are installed across the ceiling or in some systems on the walls and provide clean air.
This air moves unidirectionally across the room at a speed of about 0.45 m/s (90 ft/min). And through the floor, it removes air pollutants from the room. This uses much more system air than a clean room with turbulent ventilation. But due to the directional movement of air, it minimizes the spread of pollution in the room and directs it out through the floor.
Despite the difference in ventilation methods, both types of cleanrooms, i.e. turbulent and unidirectional, can use clean air devices such as unidirectional tables or isolation chambers. These devices provide locally filtered air and improved air conditions in areas where the product may be exposed to contamination, such as the area where the product is prepared to be opened against contamination.
Classification of Clean Rooms Based On Sensitivity and Pressure
Clean rooms are divided into two general categories in terms of sensitivity and room pressure:
Positive Pressure Cleanrooms
Clean room air conditioning systems are classified into 2 categories of positive and negative pressure clean rooms (heating, ventilation and air conditioning). Positive air pressure clean room systems are commonly used for medical, pharmaceutical, electronics, aerospace, optics, military and defense, research applications, etc. Where air escaping from doors, ceilings or walls is not dangerous due to positive air pressure. Creating safety or health concerns will determine the required particulate cleanliness of the cleanroom design concept, the amount of air filter, CFM (cubic feet per minute) and total air conditioning.
Positive air pressure cleanrooms typically operate in the air pressure range of 0.02 to 0.2 inches of water column (H20). Positive air pressure means that the clean room or rooms filled with filtered air have a higher pressure than the surrounding space outside the room(s).
Negative Pressure Cleanrooms
Clean rooms, with negative air pressure, are used for hazardous manufacturing processes. Negative air pressure cleanrooms are also used for cleanrooms with the following safety levels:
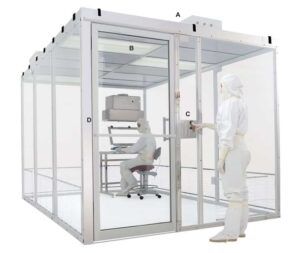
Design and Construction Clean Room
It is important to consider the following:
Design standards: Select appropriate design standards such as ISO 14644 to ensure compliance with cleanliness requirements.
Layout and materials: designing the room plan with consideration of air flow, access and efficient use of space. Selection of materials with easy cleaning capability and minimum particle production.
Service provision: Planning for the provision of clean water and gases, electricity, lighting, ventilation system and temperature and humidity control in a safe manner and in accordance with clean room standards.
At this stage of clean room design and construction, the user must choose the design standards to be used, the overall plan and layout of the room, as well as the appropriate building materials. In addition, how to provide services such as ventilation, electricity and lighting to the clean room should also be considered.
Important Points in The Design and Construction of a Clean Room
In general, paying attention to the following matters is important and must be observed.
Construction Materials the construction materials must have a smooth and polished surface facing inward toward the cleanroom. The choice of color for ceilings, walls, and doors is usually white. Nowadays, sandwich panels filled with polyurethane or polystyrene, covered with baked steel sheets, are commonly used.
The surface must be free of projections and should be easy to clean from any settled contaminants. The surface coating in the cleanroom should not break easily, and chips or particles that may contaminate the cleanroom need to be removed.
Corners and connection point should not have openings that could harbor dirt and then disperse it. Penetration points (e.g., for equipment rooms, fire alarm systems, sprinklers, or other lighting devices) should be kept to a minimum and insulated with an appropriate type of silicone (these silicone adhesives should be antifungal).
Utility services
provided to process equipment should have plumbing and cables concealed within the cleanroom space. (For example, in the pathways, pipelines and wiring are covered with steel panels labeled appropriately, indicating flow direction and pathway markers.)
The walls, floors, and ceilings in cleanrooms should be designed and constructed in a way that allows for easy cleaning of the surfaces.
The surface of the cleanroom, especially the floor, must be able to resist chemical disinfectants or liquid products used in the cleanroom. Strong acids or solvents that may attack the surface are used in certain processes.
The type of flooring for the cleanroom should be easy to clean and resistant to chemicals. There should be seamless coverings, particularly at the junction where the floor meets the wall and where walls meet each other, as well as from the floor to the ceiling.
The ceiling design and installation should not obstruct inspections or other services provided by personnel.
Pass-throughs for raw materials and products, both active and standard, should be equipped with dual-sided indicator lights.
Air showers for areas dedicated to sensitive pharmaceutical materials should only be located at the exit from those areas.
Fire safety sprinklers should be of the recessed type for cleanrooms, and smoke detectors should be designed in a dome shape. Fire extinguishers (powder type) should be placed in sealed boxes and be easily accessible and visible in emergencies.
Clean Room Testing and Monitoring
After construction, cleanroom performance should be evaluated:
Initial testing:
verifying the performance of ventilation systems, pressure, filtration and cleanliness level according to design standards.
Continuous Monitoring:
Regular monitoring of environmental parameters such as particle concentration, temperature, humidity and pressure to maintain cleanliness and air quality.
After the clean room is installed and commissioned, its performance should be tested according to established design standards. Also, continuous monitoring of the chamber during its lifetime is essential to ensure that it continues to achieve the required standards.
In the following, we refer to the design and manufacture of laboratory equipment:
Reactor
In a continuous, or flow-through, reactor, the material is transported fluidly by a carrier inside the reactor. Reactants are continuously fed into it. The product is revealed as a continuous stream. These types of reactors are used for a wide range of chemical and biological processes in the food, chemical and pharmaceutical industries. Depending on their type of reaction, it creates different types of shapes and types of devices.
Reactor Components
The basic components of a nuclear reactor are responsible for the safe and efficient production of nuclear energy. These components work together to initiate and control the process of nuclear fission, which produces heat to generate electricity. Understanding the main reactor components is very important to ensure the proper operation and safety of nuclear power plants.
1. Reactor Core
The reactor is the central part of a nuclear reactor where a nuclear fission reaction takes place. It consists of fuel assemblies that usually come from enriched uranium or plutonium. The fuel assemblies are arranged in such a way that the fission of the nuclear fuel is possible. Heat is generated in this process.
2. Control Rods
Control rods are used to adjust the fission rate in the reactor core. These rods are made of materials that absorb neutrons, such as boron or cadmium. By adjusting the position of the control rods, operators can control the number of neutrons available to sustain the fission process, effectively managing the reactor’s power output.
3. Cooling System
The cooling system is responsible for transferring heat from the reactor core. It circulates a coolant such as water or heavy water through the core to absorb the heat produced by the fission process. The heated coolant is then used to generate steam, which drives turbines to generate electricity.
4. Reactor Tank
The reactor vessel is a rigid steel-clad structure that contains the reactor core and cooling system. It is resistant to high pressures and temperatures. At the same time, it creates a barrier against the spread of radiation. The integrity of the reactor vessel is critical to prevent radioactive material from escaping.
5. Control System
The control system of a nuclear reactor includes various tools and mechanisms for monitoring and regulating the operation of the reactor. It enables operators to adjust parameters such as coolant flow, control rod position and power output to maintain safe and stable reactor conditions.
6. Handling and Storage of Fuel
Fuel handling and storage systems are responsible for the safe handling of nuclear fuel before and after it is used in the reactor core. It includes the following.
Loading processes
Fuel unloading and storage
Used fuel management
Radioactive waste
Laboratory Reactors
A laboratory reactor is a reaction control device. The reactor is a lined glass tank into which a thermal control fluid is pumped to control and regulate the temperature of the reactor contents. A number of other sensors such as temperature, pH and pressure are also used to measure and record the parameters of the reactor contents. In fact, it can be said that laboratory reactors are devices for conducting chemical reactions under supervision and with the possibility of controlling various parameters.
History of Laboratory Reactor
The first laboratory reactors evolved from control systems used in chemical plants. These reactors were generally dedicated to specific tasks because it was difficult to reprogram them. These reactor prototypes were often made at home or in a small workshop, and instead of software systems to control temperature and pressure, they used hardware.
Modern Examples of Laboratory Reactors
Modern systems of today’s reactors are a wide variety of different types that have the ability to work on a wide range of parameters. Usually, the information in these reactors is transferred to the computer for storage, and the necessary controls are carried out based on the instructions in the computer. Although in other devices it is possible to record information outside the computer.
Advantages of Laboratory Reactor
One of the advantages of laboratory reactors is that they give the user more control over chemical reactions, including temperature control of vessel contents, measurement of parameters such as pH or pressure, and mixing and dispersion applications. User controls for laboratory reactors depend primarily on the types of reactions that are taking place (polymerization, hydrocracking, etc.). These settings include flow rate, temperature range, volume and pressure range.
Application of Laboratory Reactor
Applications of laboratory reactors include synthesis, decomposition and conversion, mixing and drying of powders, production of lotions and creams, fuel research and processing of fibers in liquids and polymers. This reactor is used in industries such as pharmaceuticals, cosmetics, polymer and petrochemical products, agriculture, etc.
Design Stages of Reactors
Conceptual Design
– Determining the type and amount of raw materials and products.
– Process analysis and reaction simulation.
Engineering Design
– Calculations related to measuring temperature, pressure and reaction time.
– Choosing the right materials for making the reactor
– Designing cooling and heating systems.
Software Design
– Using simulation software such as Aspen Plus and COMSOL to analyze and optimize the design.
Construction Preparation
– Preparation of executive plans and material specifications.
– Planning for the construction and finalization of equipment.
Laboratory Furnace
In the construction of small volume furnaces, which are known as laboratory furnaces, frames with steel sheets with a thickness of 1 to 2 mm are used. After laser cutting, bending and shaping. And it is covered with static paint. In the construction of a laboratory furnace, the power supply and control system is usually considered a part of the furnace chassis. And it is placed in the lower part or on the side of the chassis. It is necessary to pay attention to maintaining a small air gap in order to prevent the heating of the control system and the power supply circuit for the construction of the furnace.
General Characteristics of The Laboratory Furnace
It has a fully insulated chamber with fireproof bricks and fireproof cement and fireproof cotton. Strong elements around the chamber create a high temperature up to about 1100 or 1500 degrees Celsius. Electric furnace is used to melt some materials and to catch ash of other materials. Thermal chamber of the electric laboratory furnace is equipped with a thermostat, thermometer and digital timer. The outer body is made of oiled sheet with electrostatic paint coating. The accuracy of the display is about 2 to 4 degrees Celsius.
Laboratory furnaces are available in different sizes. Because the use of the furnace is very high and they are used by factories, laboratories, and metal smelting mines. For this reason, they are classified in the following categories in terms of volume and size:
Ovens are available in volumes of 2, 2.5, 3.5, 4.5, 5.5, 7.5 liters.
Laboratory Furnace Insulation
A sample of a laboratory device must have certain standards. Now, if the working temperature is high, safety becomes many times more important.
The different temperature protection layers formed by the lava furnace are:
1. Pourable mass to cover element plates.
2. Ceramic fiber fireproof blanket to control the heat of the elements.
Quality of the insulation is so high that when internal temperature of the device is 1000 degrees, its external body heats up only a very small amount. Application of this furnace is in the laboratories of industries, ceramics and bitumen testing and metallurgy, as well as metal plating laboratories and industrial molds. Power consumption of this device is 2kw per hour and time to reach the temperature of 1000 degrees is 70 minutes. The insulation of this furnace is made entirely of grade 1 ceramic fiber with a temperature tolerance of 1430 degrees.
Design of This Equipment
Analysis of Needs and Design Specifications
– Purpose and application: determining the type of raw materials, final products, temperature, pressure and required purity.
– Distillation type: choosing the type of distillation to be done (simple distillation, under vacuum, steam distillation, etc.).
Selection of Materials and Components
– Materials: choosing the right materials to make the components of the device, especially the distillation pot and condenser. These materials must be resistant to temperature and pressure, as well as compatible with chemicals.
– Size and dimensions: determining the overall dimensions of the device according to the volume of liquids, maximum temperature and required pressure.
Condenser System
– Condenser type: choosing the type of condenser (such as tube-in-tube or horizontal condensers) based on process needs.
– Calculation of heat transfer level: calculation of the required level for heat transfer and steam condensation.
Distillation Column
– Column type and design: if fractional distillation is used, the design of the distillation column, including packing specifications or trays for separating liquids with different boiling points.
– Calculation of thermal and material balances: performing calculations to determine the thermal and material balance requirements inside the column.
Control Systems
– Temperature control system: designing sensing and control systems to monitor temperature and pressure in different parts of the device. – Control circuit: designing electronic circuits and necessary software for automatic process control.
Testing and Validation
– Simulation: using simulation software (such as Aspen Plus or CHEMCAD) to predict the performance of the device. – Risk analysis: assessment of risks and hazards related to the design and operation of the device.
Construction and Installation
– Manufacturers and production: contracting with manufacturers to produce parts, and ensure the quality of materials. – Installation and testing: installing the device in the laboratory and performing initial tests to ensure proper operation.
Laboratory Mixer
Laboratory stirrers are devices that mix different laboratory fluids through various systems. Since the speed of mixing the samples and its frequency are very important in the experiments. Stirrers are essential laboratory equipment. Some types of these laboratory mixers, in addition to mixing the samples, also perform the heating action at the same time.
The homogeneous mixture that is finally prepared by mixers is used in various experiments in laboratories as well as in different industries. These devices are widely used in laboratories such as biotechnology laboratories, biological sciences and wastewater treatment. Also, among the various industries in which mixer devices are widely used, we can mention the pharmaceutical, cosmetic, electronic, food, etc. industries.
Types of Laboratory Mixers
There are different types of laboratory samples of this device, which we mention below:
High Shear Laboratory Mixing
A high shear laboratory mixing device transfers or disperses different phases of material into a continuous phase. This process concentrates the compound into compounds that are normally non-degradable.
Multipurpose Type
Mix
Multipurpose laboratory mixer will help in mixing and collecting different materials. The final result of the composition will be a uniform mixture.
Homogenization
You can use this device to combine various elements to form a uniform mixture. This substance helps to make a uniform solution of two liquids or insoluble elements.
Resolve
You use the machine to mix a solid to form a uniform mixture in a liquid. In the end, you will be able to reach a consistent solution. Decomposition
The device can also help you break down different elements into very small units. These elements lose strength and coherence and gradually sink into smaller parts.
Ribbon Mixer
Mixers or ribbon mixers have horizontal U troughs with a special ribbon stirrer. It also has external and internal spiral stirrer. As the inner ribbon moves the material in one direction, the outer ribbon moves it in the opposite direction.
Mixer Design
The design of mixers is very diverse. In this process, various factors such as minimum space occupation. High percentage of homogenization, minimum time required for homogenization, high flexibility. We take into account minimum energy consumption, easy installation and minimum unloading and loading time. By using engineering sciences, it is possible to design and manufacture all kinds of mixers in different industries.
These machines are suitable for small scale mixing. They rely on pneumatic or electric motors that have a reduced gear range or direct drive speed. Mixing shafts with replaceable and removable propellers provides the ability to adapt different designs.
Types of Control System
Feedback Control Systems
PID Control (Proportional-Integral-