The Regeneration Phase Itself Consists of a Sequence of Sub-Phases, Including:
- Expansion: Reducing pressure from high to low.
- Co-current expansion GLE1, GLE2, GLE3: Co-current expansion stages (GLE1, GLE2, GLE3, only in 6-adsorber mode).
- Purge sequence.
- Counter-current expansion GEE.
- Low-pressure purge.
- Purge (in 5-adsorber mode, purge gas is taken from the product gas).
- Repressurization: Increasing pressure from low to high adsorption pressure.
- Repressurization DA1, DA2, DA3.
Pressure Changes During The Process Sequence
Process Description
The adsorption separation process is composed of a continuous supply of product from several pressure vessels filled with adsorbent, connecting piping, and related control valves. During operation, at least one adsorber is operating at high pressure, separating impurities from the process stream, while other adsorbers are being regenerated. The control program ensures the sequence of the process and the change of adsorbers in the flow to maintain product purity. Therefore, the sequence ensures that there are always two adsorption sequences operating in parallel. Additionally, before the adsorption capacity of one adsorber is fully utilized, another adsorber is regenerated and pressurized to take over the adsorption. The following diagram shows the pressure changes during the process sequence and adsorber change in a similar project.
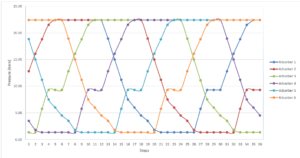
Description of The Simulated Process
Introduction
SANILCO Industry Process Company has simulated PSA unit of TEHRAN Refinery based on information and industrial data of the refinery and additional information from Zhang et al.’s article. This project has three phases; The first phase is a single bed, the second phase is a double bed and the third phase is optimization. The input information is extracted from the industrial documents of TEHRAN Refinery. The table below is the data sheet of the unit and the material balance of the main flows.
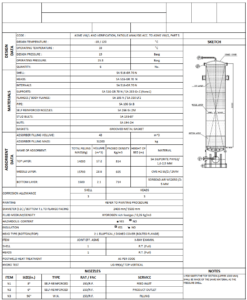
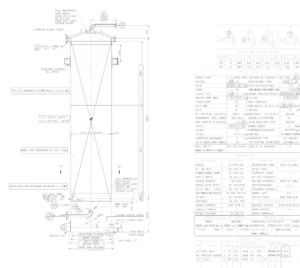
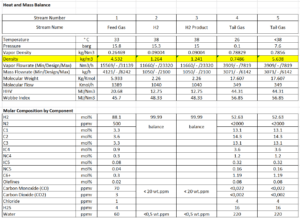
Process Description
The raw feed gas flows upwards through the adsorbent bed from the bottom, and impurities such as CO2, hydrocarbons, and CO are selectively adsorbed on the internal surface of the adsorbent. The purified hydrogen product gas exits the adsorbent at the top and is discharged to the product header , The purity of the product hydrogen remains constant during the adsorption cycle. At the end of the adsorption cycle, impurities begin to appear. This indicates that the adsorbent is saturated with impurities and must be regenerated. The adsorption bed and adsorbent used in the single-bed PSA system are similar to the dual-bed PSA system, which will be discussed in detail later.
Simulation Description
Adsorption Bed
The adsorption bed consists of three layers. The top layer is filled with Zeolite 5A. Since we did not have complete information about the adsorbent in the refinery’s PSA unit, we used a similar zeolite as in the mentioned article. The middle and bottom layers used data from Tehran Refinery. A brief description of each layer is given below:
ZEOCHEM ZA05-PSA-II
The top layer, ZEOCHEM ZA05-PSA-II silicapur, is an alkali metal aluminosilicate. It is the calcium form of the type A molecular structure and has an effective pore opening of 5 angstroms. It is specifically developed for hydrogen PSA processes, ideally complementing the adsorbent bed required for separation and offering high capacity and kinetics for the adsorption of nitrogen, carbon dioxide, and especially carbon monoxide.
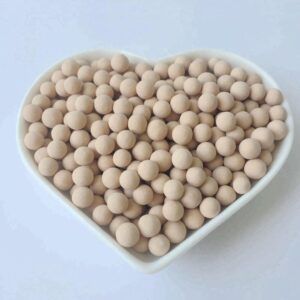
The characteristics of the absorber and the absorption bed are given in the table below, the data of which is obtained from the mentioned article. The correlation parameters of loading ratio (LRC), linear driving force coefficients (LDF) and heat of adsorption in the adsorbent (zeolite 5A) for each component are given in the following table.
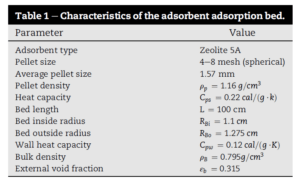

Adsorption equilibria for the two components on zeolite 5A were measured using a volumetric method at 293.15 K, as shown in the figure below. In the low pressure range of about 0 to 12 atmospheres, the simulation data are in good agreement with the experimental data. As the figure shows, the CO adsorption capacity at 6 atmosphere pressure is 1.18532 mmol/g, while the hydrogen adsorption capacity is only 0.09631 mmol/g, indicating that zeolite 5A has a high adsorption capacity for CO.
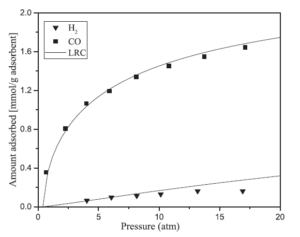
CarboTech CMS H2 55/2
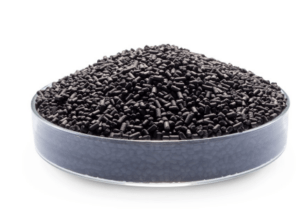
CarboTech CMS H2 55/2 interlayer is a high performance activated carbon specifically designed for hydrogen extraction from various gases. This product is produced using advanced technology and has high absorption capacity, high absorption speed and long-term stability. CarboTech CMS H2 55/2 is widely used in various industries to produce pure hydrogen. Its typical features are as follows:
Filling volume 23.6 cubic meters
Bed height 5217 mm
Pack density 665 kg/m3.
Moisture (when packed): 2% max
Ash: 4%
Seed diameter: 2.2 ± 0.2 mm
SORBEAD AIR WS2050 /2-5 MM
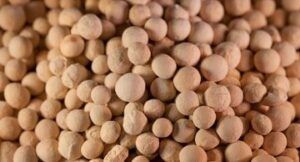
Finally, the bottom layer consists of SORBEAD AIR WS2050/2-5 MM with a filling volume of 2.1 cubic meters, bed height of 465 mm and pack density of 714 kg/cubic meter. SORBEAD AIR WS2050 /2-5 MM is a high performance sorbent designed for compressed air industry applications. This product is available in the form of hard and spherical beads; These beads absorb water and are resistant to crushing and wear.
Phase One: Single Substrate Simulation
Synthesis gas without moisture (a mixture of hydrogen and carbon monoxide in the ratio of 90 to 10 mole percent) has been used as feed. The figure below shows the schematic of pressure swing adsorption (PSA) cycles for a single substrate of Aspen Adsorption software.
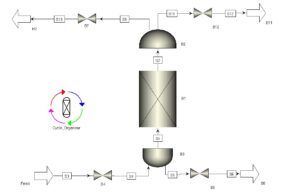
Single Bed Model
In the single bed model, synthesis gas enters the adsorption bed (Bed1) through the feed inlet, and pure hydrogen exits through the H2 outlet. During this stage, hydrogen adheres to the adsorbent surface due to a stronger adsorption force, while other gases are separated. In the simultaneous pressure reduction stage, the remaining hydrogen is removed from the bed. As the pressure decreases, hydrogen is detached from the adsorbent surface and returns to the gas phase. Then, in the purge stage, using the B5 stream, the remaining adsorbed gases are removed from the bed. This stage is essential for preparing the bed for the next cycle. In the regeneration stage, pure hydrogen is injected into the bed to remove any remaining impurities. Finally, in the pressure increase stage, synthesis gas is reinjected into the bed to bring the system pressure back to its initial value and start a new cycle.
Dual Bed Model
For the dual bed model, similar steps are followed, with the difference being additional steps to equalize the pressure between the two beds. This increases the efficiency of the process. The simulated models have been compared with experimental data, and the results show good agreement between the model and the experimental data. This indicates that the simulation model accurately predicts the behavior of the real system. The figure below shows a schematic of the pressure swing adsorption (PSA) cycles for a dual bed in Aspen Adsorption software.
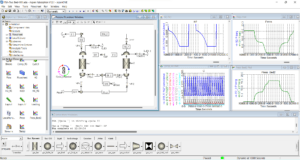
Pressure Swing Adsorption (PSA) Cycle Performance Evaluation
After confirming the single bed failure curves, five and six stage PSA cycles were simulated for single and double beds, respectively. The equivalent steps for the sequence of cycles for both PSA processes are listed in the table below.
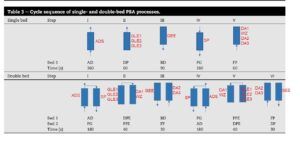
Study of The Performance Parameters of a Single-Bed PSA Cycle Model
The figures below show the single bed pressure during PSA cycles.
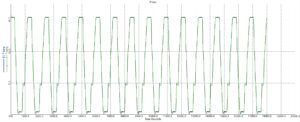

Single Bed Model
In the single bed, during the adsorption stage, the adsorption bed pressure remains near 15 barg. After 100 seconds, the pressure decreased during the simultaneous pressure reduction stage. In this stage, the product gas (H2) is mostly removed from the adsorption bed. In the third stage (purge/countercurrent pressure reduction), purging is done in a short time because the amount of hydrogen adsorbed on the zeolite was in low equilibrium. The adsorption bed pressure decreases to 1 barg and the mole fraction of hydrogen in the adsorption bed also decreases to a low hydrogen mole fraction. In the regeneration stage, pure hydrogen is used to regenerate the adsorption bed until pure hydrogen reaches the feed end. Then, the bed is pressurized with feed gas to an adsorption pressure of 15 barg and is ready for the next cycle.
Parametric Study of The Performance of The Dual Bed PSA Cycle
The cycle method for the dual bed is similar to the single bed model. The most important difference is that the dual bed model has pressure equalization stages, including the pressure reduction equalization stage and the pressure increase equalization stage, which equalize the pressure of the two beds and keep the mole fraction of hydrogen constant. In addition, in the regeneration stage in the dual bed model, pure product hydrogen in one bed is used to regenerate the adsorption bed of the other. The following figures show the pressure of the two beds during the PSA cycles.
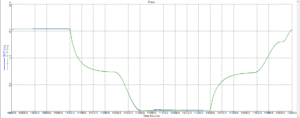
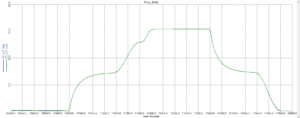
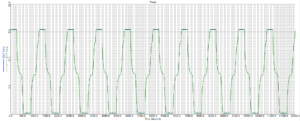
Summary
In summary, increasing pressure in the adsorption process concentrates the weakly adsorbed component (H2) in the gas phase and enriches the strongly adsorbed component (CO) in the adsorption phase. Conversely, decreasing pressure in the desorption process concentrates the strongly adsorbed component (CO) in the gas phase. During the adsorption process, the bed temperature increases. This is due to the exothermic nature of the adsorption process. The performance of the PSA system is evaluated based on the purity of the produced hydrogen, the amount of hydrogen recovered, and the efficiency of the system.
Conclusion
In this work, single and dual bed PSA cycle models for the adsorption of synthesis gas (H2/CO) on a zeolite 5A adsorbent were developed based on industrial refinery data from Tehran and supplementary information from Zhang et al.’s paper. After model validation, breakthrough curves were simulated, and good agreement with experimental curves was observed. Subsequently, PSA cycles were constructed for both single and dual bed models. A parametric study of the PSA cycles was conducted. Conclusions from this study include:
- Recovery and efficiency are better for the dual bed than the single bed.
- The dual bed system has a much better PSA performance in terms of hydrogen purity, recovery, and efficiency compared to the single bed system under feed flow rate conditions.
Simulation of Single and Dual Bed PSA Process for H2 Separation from CO in ADSIM
In this project, the single and dual bed PSA process for H2 separation from CO was simulated in the ADSIM software. This project, along with related training and images, has three phases: phase one for the single bed, phase two for the dual bed, and phase three for optimization. The main source of information is a research paper and data from Tehran refinery.