Introduction
Petrochemical industries play a vital role in the production of raw materials for various sectors and are considered one of the most important industrial segments worldwide. Among these, Air Separation Units (ASUs) hold special significance due to their ability to produce essential gases such as oxygen, nitrogen, and argon. These units utilize complex cryogenic separation processes to generate high-purity gases that are employed in diverse applications, including petrochemical processes, medicine, metallurgy, and the food industry.
The simulation of industrial processes serves as a powerful tool for optimizing and designing industrial units, allowing for a precise analysis of operational parameters and the identification of system strengths and weaknesses. The use of ASPEN HYSYS software facilitates accurate modeling of ASU units, enabling engineers to improve performance and reduce operational costs by evaluating various scenarios.
Air Separation Unit (ASU)
ASU divides air into its main components, which are typically nitrogen and oxygen, and sometimes argon and other inert gases.
The most common method for air separation is fractional distillation. Cryogenic air separation units (ASUs) are designed to produce nitrogen or oxygen while generating argon as a by-product. Other methods, such as membrane separation or adsorption, are commercially used to isolate specific components from the air.

The Main Stages of The ASU Process
Air Compression
Description: Air is drawn in from the surrounding environment by powerful compressors and compressed to high pressures (typically between 5 to 10 bar).
Objective: To increase the air pressure to facilitate subsequent processes such as cooling and separation.
Equipment: Multi-stage compressors with inter-stage cooling systems.
Air Cooling and Purification
Description: The compressed air is transferred to a heat exchanger to reduce its temperature. It then passes through filters and molecular sieves (such as silica gel and zeolites) to remove impurities like moisture, carbon dioxide (CO₂), and hydrocarbons.
Objective: To prevent the formation of deposits and freezing in the later stages of the process.
Equipment: Heat exchangers, filters, and molecular sieves.
Air Cooling and Liquefaction
Description: The purified air is transferred to a main heat exchanger (such as a plate or shell-and-tube heat exchanger) and cooled to very low temperatures (approximately -170 to -190 degrees Celsius). This process is carried out using refrigeration cycles, such as the Claude cycle or the Helium cycle.
Objective: To convert air into a liquid form to facilitate the separation of its components.
Equipment: Cryogenic heat exchangers and expansion turbines.
Air Separation
Description: The liquefied air is sent to a distillation column. In this column, the air components are separated based on differences in their boiling points:
Oxygen (boiling point: -183 degrees Celsius) is collected at the bottom of the column.
Nitrogen (boiling point: -196 degrees Celsius) is collected at the top of the column.
Argon (boiling point: -186 degrees Celsius) is separated as a by-product in the middle sections of the column.
Objective: To produce high-purity gases.
Equipment: Cryogenic distillation columns equipped with trays or specialized packing.
Product Recovery and Storage
Description: The separated gases (oxygen, nitrogen, and argon) are stored in either liquid or gaseous form. For liquid storage, insulated pressure tanks are used. For gas storage, the gases are transferred to pressurized vessels.
Objective: To maintain and distribute the final products.
Equipment: Cryogenic storage tanks and gas compressors.
Energy Recovery
Description: In this stage, the cold energy generated during the separation process is recovered. This is achieved using expansion turbines, which convert the energy from the cold gases into mechanical energy.
Objective: To enhance energy efficiency and reduce electricity consumption.
Equipment: Expansion turbines and heat exchangers.
Control and Monitoring
Description: The entire ASU process is managed by advanced control systems (such as DCS or PLC). These systems accurately monitor operational parameters such as temperature, pressure, and flow, ensuring optimal unit performance.
Objective: To enhance safety, reduce errors, and improve unit performance.
Equipment: Industrial control systems and precise sensors.
Cryogenic Distillation Process
By cooling air to the point of liquefaction and then performing fractional distillation on this liquid, high-purity gases can be produced. This process was initiated by Carl von Linde in the early 20th century and is still used today for the production of high-purity gases. The cryogenic separation process requires the integration of heat exchangers and separation columns to achieve good efficiency, with all the energy needed for cooling supplied by the air compressor located at the beginning of the unit.
To achieve ultra-low temperatures, a refrigeration cycle is necessary, and thermal equipment must be housed within an insulated chamber (commonly referred to as a “cold box”). The cooling of gases required for the operation of this refrigeration cycle demands a significant amount of energy, which is provided by the air compressor. Modern ASUs utilize expansion turbines to drive the compressor.

Characteristics of The Cryogenic Method
The cryogenic method for producing nitrogen and other gases has several important characteristics that make it a widely used and favored approach in various industries. Some of the main features of this method include:
High Purity
The nitrogen and other gases produced through the cryogenic method exhibit high purity levels. This characteristic is crucial as industries such as electronics, pharmaceuticals, oil and gas, and food processing require high-purity gases of excellent quality.
Precise Control
The cryogenic method allows for precise control over the production rates of nitrogen and other gases. This capability helps industries quickly adjust production levels to meet their specific needs.
Cost Savings
The cryogenic method is economically advantageous in terms of costs. Compared to other methods such as fractional distillation or membrane adsorption, it incurs lower expenses, enabling industries to reduce production costs.
Safety and Sustainability
The cryogenic method is recognized as a safe and sustainable approach due to its non-reliance on hazardous chemicals and complex processes. Additionally, this method is more environmentally friendly and contributes to environmental preservation.
Products of The ASU Unit
The products of this unit include the materials listed in the table below.
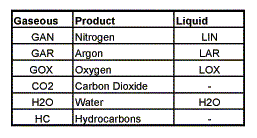
Oxygen
Applications:
– In petrochemical industries for oxidation and combustion processes.
– In steel and metallurgy industries for steel production and metal refinement.
– In medical industries for therapeutic and hospital uses.
– In environmental industries for water and wastewater treatment.
Purity Level:
Typically between 95% to 99.9%.
Nitrogen
Applications:
– In petrochemical industries as an inert gas to prevent unwanted reactions.
– In food industries for packaging and extending product shelf life.
– In electronics industries to create an inert atmosphere during manufacturing processes.
– In pharmaceutical industries for drying and preserving sensitive materials.
Purity Level:
Typically between 99% to 99.999%.
Argon
Applications:
– In welding industries as a shielding gas to prevent metal oxidation.
– In lighting industries for filling fluorescent and LED lamps.
– In medical and scientific research industries.
Purity Level:
Typically above 99.99%.
Importance of ASU Products
The products of Air Separation Units (ASU) are highly significant due to their wide applications across various industries, including petrochemicals, steel, medicine, food, and electronics. These units play a crucial role in enhancing industrial processes and increasing productivity by producing high-purity, quality gases.
Leak Detection in ASU Units
In ASU units, due to the vacuum insulation of certain pipes, one of the essential tasks for overhauling the unit can be to check the integrity of the vacuum in the pipes and to dry these pipes before the unit is started up.
Additionally, there is a Cold Box in this unit that houses the BAHX heat exchangers for cryogenic heat transfer. According to API 668 and ALPEMA standards, helium leak testing should be employed for their servicing. If leaks are present in these exchangers, the overall efficiency of the ASU unit can significantly decline (depending on the design, the exchangers may vary in type).
The condenser and separation column located within the Cold Box must also be leak-tested and serviced according to standards. By overhauling the piping system and equipping the Cold Box, it can be expected that the unit will return to its original efficiency. In this unit, the turboexpanders must also undergo helium leak testing in accordance with API 617 standards.
Simulation
The simulation of the ASU (Air Separation Unit) at the Bushehr Petrochemical Company is conducted using Aspen HYSYS software for the purpose of analyzing and optimizing the air separation process. In this unit, air is separated into oxygen and nitrogen, which are essential for industrial and petrochemical applications.
Simulation Stages:
Defining Materials and Equations of State: Selecting the appropriate equation of state for modeling the thermodynamic properties of gases (such as oxygen and nitrogen) is essential.
Defining Equipment: Initially, the main equipment such as compressors, heat exchangers, distillation columns, and storage tanks must be defined within the software.
Inputting Operational Data: Operational parameters, including temperature, pressure, and input and output flow rates, must be accurately entered.
Analyzing Results: After the simulation is completed, the results, including the composition of the outlet gases, separation efficiency, and energy consumption, are analyzed.
Optimization: Using the optimization tools available in the software, operational parameters can be adjusted to enhance the efficiency and productivity of the unit.
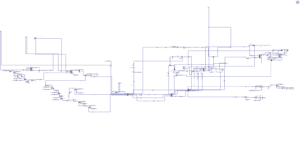
Conclusion
The simulation of the ASU unit at the Bushehr Petrochemical Company using Aspen HYSYS software serves as a key tool for analyzing and optimizing the air separation process, highlighting the importance of advanced technologies in the petrochemical industry. This simulation enables engineers and researchers to improve system efficiency and reduce production costs by thoroughly examining operational parameters and process conditions.
SANILCO, leveraging its technical expertise and experience, has successfully carried out this simulation. The results obtained can serve as a valuable reference for the design and optimization of similar units in the petrochemical industry. This project not only aids in enhancing the efficiency of the ASU unit at Bushehr Petrochemical but also provides a model for other industrial units aimed at improving productivity and optimizing energy management.
Ultimately, the results of this simulation underscore that the use of advanced simulation software can be a key strategy for enhancing performance and promoting sustainable development in the petrochemical industry.
Examples of Completed Projects
Simulation of an Air Separation Unit for Oxygen and Nitrogen Production with Aspen Hysys
Dynamic Simulation of Unit 105 and 107 ASALOUYE with Aspen Plus
Simulation of Nitrogen Separation Process From Air (Aspen Adsim)