Modeling and simulation of chemical processes are recognized as key tools in the development and optimization of innovative technologies in the chemical industry. One of the novel and intriguing areas in this field is the selective oxidation (ODH) of organic compounds, such as ethylbenzene to styrene. Styrene holds particular significance as an essential raw material in the production of polymers and various chemicals.
Chemical Looping is a novel technique in oxidation processes that has garnered attention specifically for enhancing efficiency and reducing environmental side effects. This method utilizes oxygen carrier materials to enable the selective oxidation of hydrocarbon compounds while simultaneously preventing the formation of unwanted by-products.
Oxidation of Ethylbenzen
The oxidation of ethylbenzene to styrene is a chemical reaction that occurs under specific conditions. This reaction is significant for two reasons: firstly, styrene is a key material used in the plastic and rubber industries, and secondly, this process can be considered a more sustainable method for producing styrene compared to traditional methods.
Reaction Mechanism
The oxidation reaction of ethylbenzene typically takes place under mild oxidizing conditions. In this reaction, ethylbenzene is converted to styrene in the presence of oxidizers such as air or oxygen-containing compounds. The mechanism of this reaction involves the following steps:
Formation of Free Radicals: The oxidizer attacks ethylbenzene, generating free radicals.
Electron Transfer: The free radicals react with ethylbenzene molecules, producing products including styrene.
Selectivity: By controlling the reaction conditions, selectivity towards styrene production can be enhanced.
Reaction Conditions
Various conditions can influence this reaction:
Temperature: Higher temperatures may increase the reaction rate, but they can also lead to the formation of unwanted by-products.
Pressure: Pressure can also affect the reaction equilibrium.
Presence of Catalysts: The use of appropriate catalysts can enhance both selectivity and yield of the reaction.
Sr0.8Ba0.2Fe0.2Mn0.8O3-δ after one cycle is heated from 30 °C to 950 °C at 10 °C/min and held for 30min in Ar. TG profile shows two stage mass loss. The weight loss of 1.34% in the first stage can be attributed to the removal of adsorbed water. The second stage representing 2.53% weight loss is due to the decomposition of carbonates. 500mg Sr0.8Ba0.2Fe0.2Mn0.8O3-δ adsorbed 12.65 mg of CO2. The EB/Ar flow is 25 ml/min and time on stream is 20 min. This is equivalent to a molar amount of CO2 of 1.15×10-7 mol. When the adsorbed CO2 is included in the product distribution, styrene yield will decrease by ~2.5%.
Oxygen Isotope Exchange Experiment:
200 mg samples were pretreated at 950 °C in Ar (25 ml/min) for 30 min. Then cool to 550 °C to reduce the oxygen in the samples in H2/Ar (25 ml/min). Afterwards, 18O2 (10 ml/min) is introduced to reoxidize the samples. The temperature-programed oxygen isotope exchange was conducted in 16O2 (25ml/min) with a ramp rate of 10°C/min.
Simulation
The simulation of the selective oxidation process of ethylbenzene to styrene is a significant topic in industrial chemistry and chemical engineering. Styrene, which is a key raw material in the production of polymers and other chemicals, can be synthesized from ethylbenzene as a precursor.
The oxidation of ethylbenzene to styrene is one of the key processes in the petrochemical industry. Styrene is of high importance as a raw material for the production of various polymers. This process can be conducted using oxidizers such as oxygen or air, and due to the necessity for high selectivity, its simulation is crucial.
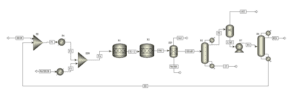
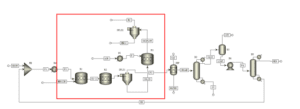
Process Modeling
Modeling this process is typically performed using chemical simulation software such as Aspen Plus or MATLAB. The key stages of this modeling include:
Definition of Reactions and Catalysts:
Simulation requires precise definition of the chemical reactions and the conditions of the catalysts. Specifying the reaction equations and radical mechanisms is of paramount importance.
Setting Operational Conditions:
Operational parameters such as temperature, pressure, and the concentration of raw materials are carefully adjusted to achieve optimal results.
Data Analysis:
After simulation, data analysis is conducted to evaluate the performance of the process. This analysis includes:
Selectivity Calculation: Examining the ratio of styrene production to by-products and determining the conditions that lead to maximum styrene production.
Optimization of Conditions: Using optimization algorithms, the optimal operational conditions for maximum production and minimum cost are established.
Conclusion
The simulation and modeling of the selective oxidation of ethylbenzene to styrene (ODH) was examined as an innovative and efficient method in the petrochemical industry. The results obtained from the simulation indicated that by optimizing operational conditions, high selectivity and effective styrene production can be achieved. Furthermore, the precise modeling of reactions and catalytic conditions plays a crucial role in identifying optimal points and reducing the production of by-products. Additionally, the analyses conducted demonstrated that variations in temperature, pressure, and the concentration of raw materials can have significant impacts on the performance of the process.