The simulation of the ammonia process is a key stage in the design and optimization of petrochemical complexes. In this regard, the petrochemical complexes of Masjed Soleyman and Lordegan, as two examples of important projects in Iran’s petrochemical industry, require the use of advanced software for analyzing and improving their performance.
The use of Aspen Plus software as a powerful tool for simulating chemical processes enables precise modeling and performance analysis of ammonia production units. Simulating the ammonia process in these complexes not only aids in optimizing production but also contributes to increasing the competitiveness and sustainability of this industry. Additionally, the license used is Casale.
The vast petrochemical complex of Masjed Soleyman is located on a 400-hectare site in the Masjed Soleyman County, 130 kilometers northeast of Ahvaz. It is situated 30 kilometers northwest of Masjed Soleyman, adjacent to the Lali Road (in the Haft Shahidan area), and 11.5 kilometers south of the Karun River. According to development plans, the area will expand to over 1,000 hectares. Geographically, this region has access to international waters through Imam Khomeini Port and is connected to Turkey, Europe, and Central Asia via the national railway network.
The Lordegan Petrochemical Complex, located in the Chaharmahal and Bakhtiari province in the Falar region. is under construction at a distance of 55 kilometers from the city of Lordegan. The Lordegan Petrochemical Company was established in 2008 and benefits from a favorable location due to its convenient access to water and gas resources. proximity to three national gas pipelines, and suitable land and conditions for leveling and infrastructure development.
Ammonia
Liquid ammonia is a colorless compound with a very strong odor. It is the most important hydrogen-containing nitrogen compound with numerous applications, including the production of chemical fertilizers.
The most common method for producing ammonia is the Haber process, which is operationally challenging due to the requirement for high temperature and pressure (temperatures between 280-350 degrees Celsius and pressures between 200 to 15 atmospheres). In this process, ammonia is produced from the reaction of nitrogen obtained from the air and hydrogen. Ammonia plants consist of three main sections: hydrogen production, synthesis gas purification, and ammonia synthesis.
Process Description of Ammonia Unit
The output gas from the secondary reformer is directed to high-temperature and low-temperature shift reactors in two stages to convert carbon monoxide into carbon dioxide, ensuring that nearly all carbon monoxide is transformed into carbon dioxide. The synthesis gas, which is almost free of carbon dioxide, is then directed to the methanation catalytic reactor, where any residual carbon oxides are converted into methane.
Due to the low conversion rate of the ammonia synthesis reaction, it is economically necessary to recycle a portion of the synthesis gas output from the reactor back into the synthesis reactor, a process known as the synthesis loop. Therefore, the synthesis gas is initially compressed and mixed with the gas output from the synthesis reactor, and after final compression, it enters the synthesis catalytic reactor. The produced ammonia is sent to the urea unit for consumption, while any excess ammonia from the urea unit is cooled and stored in a cold storage tank.
The Process of Producing Ammonia From Natural Gas Includes The Following Main Stages:
Desulfurization of natural gas
Conversion of carbon monoxide to methane
Carbon dioxide separation
Ammonia synthesis
Applications of Ammonia
1. Production of various chemical fertilizers for agriculture
2. Production of nitric acid and ammonium nitrate
3. Use in the paint industry
4. Application as a fuel or fuel derivatives
5. Utilization in air pollution control
6. Application in the manufacture of explosives
7. Use in water treatment
8. Employment in reducing catalyst systems to minimize NOx emissions
Process Flow Diagram
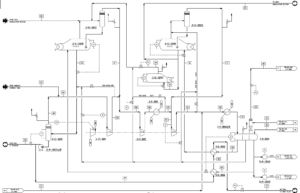
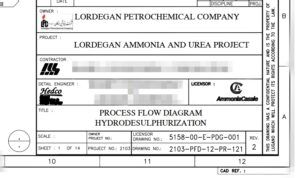
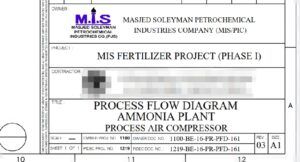
Simulation With Aspen Plus
Simulating the ammonia production process in the petrochemical complexes of Suleiman and Lordegan using Aspen Plus software is an effective method for optimizing and analyzing the performance of these industrial units. Aspen Plus is a powerful software for simulating chemical processes, enabling engineers and designers to model, analyze, and optimize complex processes.
Objective of The Simulation
The main objective of simulating the ammonia process in these petrochemical plants is to evaluate the performance of the production units, identify weaknesses, and improve process efficiency. By utilizing
Aspen Plus, key parameters such as temperature, pressure, material flow, and energy can be accurately analyzed, providing strategies to reduce energy consumption, increase production, and enhance product quality.
Simulation Stages
Process Modeling
In this stage, the ammonia production process, which includes various units such as steam reforming, carbon monoxide conversion, carbon dioxide separation, and ammonia synthesis, is modeled in Aspen Plus software. Real data from industrial units, including temperature, pressure, and material flow, are input into the software.
Performance Analysis
After modeling, Aspen Plus analyzes the performance of the process. This analysis involves examining the efficiency of the reactions, energy consumption, heat losses, and the production of the final product. Through this analysis, engineers can identify areas that require improvement.
Optimization
In this stage, using the optimization tools available in Aspen Plus, process parameters such as temperature, pressure, and feedstock ratios are adjusted to enhance process efficiency. For instance, modifications may be made to the operational conditions of steam reforming or ammonia synthesis to reduce energy consumption and increase ammonia production.
Validation Parameters
The validation parameters for the ammonia production process in the Soleyman and Lordegan petrochemical complexes consist of a set of criteria and key performance indicators used to ensure the proper and optimized functioning of ammonia production units. These parameters assist engineers and specialists in evaluating the process from technical, operational, and qualitative perspectives, ensuring that the system operates according to design specifications and standards.
Key Validation Parameters in the Ammonia Production Process
Operational Parameters
Temperature and Pressure: The temperature and pressure at various stages of the process, such as steam reforming, carbon monoxide conversion, and ammonia synthesis, must be accurately controlled and monitored. These parameters have a direct impact on the efficiency of the reactions and the quality of the final product.
Material Flow: The flow of raw materials, such as natural gas, steam, and air, should align with the initial design to ensure that the process operates correctly.
Feedstock Ratio: The ratio of feedstocks in the reactions (such as the hydrogen to nitrogen ratio in ammonia synthesis) must be carefully controlled to maximize process efficiency.
Quality Parameters
Synthesis Gas Purity: The purity of the synthesis gas (hydrogen and nitrogen) must be checked prior to its entry into the ammonia synthesis reactor to ensure that impurities are minimized.
Ammonia Concentration: The concentration of ammonia in the final product should comply with established standards to guarantee product quality.
Impurities: The level of impurities in the final product (such as water, CO2, and other gases) must be examined to ensure that the product meets technical specifications.
Importance of Monitoring These Parameters
Monitoring these parameters in the validation process assists the Soleyman and Lordegan petrochemical complexes in:
Optimizing Process Performance: By precisely controlling operational parameters, process efficiency is enhanced, and production costs are reduced.
Ensuring Product Quality: By evaluating quality parameters, it is ensured that the final product conforms to the desired standards.
Reducing Energy Consumption: By optimizing energy parameters, energy consumption is lowered, and productivity is increased.
Complying with Environmental Regulations: By controlling pollutant emissions, petrochemical facilities can operate in accordance with environmental regulations.
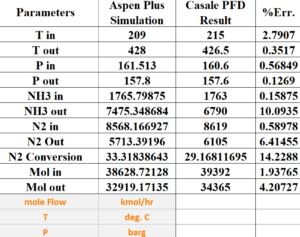
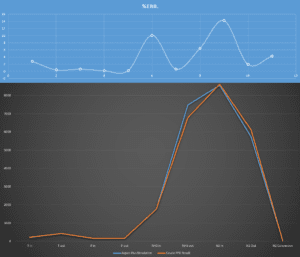
Casale License
The Casale license is a technology and technical knowledge offered by the Swiss company Casale SA. It is primarily utilized in the chemical and petrochemical industries. This license is applied for various processes such as the production of ammonia, methanol, urea, and other chemicals. In petrochemical facilities like the Sulayman and Lordegan complexes, the Casale license is typically used to optimize production processes and enhance efficiency.
In petrochemical plants such as those in Masjed Soleyman and Lordegan, the Casale license can be employed to optimize ammonia, methanol, and urea production processes. These technologies assist these complexes in producing high-quality products with reduced energy and raw material consumption, while simultaneously lowering operational costs. Additionally, by decreasing pollutant emissions, these petrochemicals can achieve their environmental goals.
SANILCO
SANILCO is a reputable and experienced firm in the industrial sector, engaged in various areas including design, simulation, optimization, and economic evaluation. This company has significant expertise and experience, particularly in simulating industrial processes.
Among the notable projects of this company are the simulation of ammonia production processes for the petrochemical plants in Masjed Soleyman and Lordegan. These activities demonstrate the commitment and capability of Anil Pars Process Industry in providing innovative and optimized solutions for the petrochemical industry and related sectors.
Examples of Completed Projects
Aspen Plus Simulation of Ammonia Production Unit
Simulation and Optimization of T-3802 of LORDEGAN Pet. Co.
Conclusion
The simulation of the ammonia production process in the petrochemical complexes of Masjed Soleyman and Lordegan using Aspen Plus software yielded significant results. This simulation, conducted by Anil Pars Process Industry Company, analyzed and optimized various stages of ammonia production, aiding in the identification of strengths and weaknesses within the processes.
The results demonstrated that through precise modeling and the conducted simulations, it is possible to optimize energy consumption, reduce production costs, and enhance productivity. Additionally, this research can contribute to the reduction of pollutants and the improvement of environmental conditions in these complexes.
Ultimately, the simulations carried out in this project serve as an effective tool for managerial decision-making and the development of optimization strategies in the petrochemical industry. They can also provide a solid foundation for future projects in this field.