Introduction
In the fast-paced world of industry and technology, hydrogen has gained a special place as a clean energy carrier and a raw material for many chemical products. To produce this valuable element, various methods exist, one of the most important being “steam methane reforming” ، In this process, methane (CH4), which is abundantly found in natural gas, reacts with steam (H2O) at high temperatures (700 to 900 degrees Celsius) in the presence of a nickel catalyst, converting into hydrogen (H2) and carbon monoxide (CO). This chemical reaction is like a molecular dance where methane and steam molecules pair up and eventually yield hydrogen and carbon monoxide molecules.
Advantages of Steam Methane Reforming:
-
Production of High-Purity Hydrogen
Hydrogen produced in steam methane reforming has a high purity and can therefore be used in various applications such as ammonia production, fertilizers, fuel cells, and oil refining.
-
Production of Carbon Monoxide
Carbon monoxide produced from this process is an important raw material for synthesizing methanol, formic acid, and other chemicals.
-
Simplicity and Efficiency
Steam methane reforming is a relatively simple and efficient process that can be used to produce hydrogen and carbon monoxide on various scales.
-
Ability to Use Various Methane Sources
This process is highly flexible and can use various methane sources, such as natural gas, biogas, and coal, to produce hydrogen and carbon monoxide.
Description of The Gas Reforming Process and Methanol Synthesis
In the following, we have first provided a detailed description of the common reforming process in industry and methanol synthesis; then, using industrial data, we conducted a simulation. The mentioned process is multi-stage and includes the following stages:
First Stage: Pre-Purification and Steam Reforming
At first, natural gas enters the pipeline with a pressure of 11 bar, and then the pressure is increased to 30 bar by the compressor. Next, return gas with a high concentration of hydrogen is added to this mixture. But before entering the heart of the process, i.e. steam reforming, existing impurities, especially sulfur, must be removed. For this purpose, natural gas is desulfurized and its sulfur concentration reaches less than 0.05 ppm. In this step, desulfurized natural gas is mixed with steam and preheated and then enters the pre-reformer reactor. In this reactor, hydrocarbons in natural gas are converted into hydrogen, carbon oxide and methane. The outlet temperature of the reformer is 920 degrees Celsius, which indicates the high heat of this chemical reaction.
Second Stage: Cooling and Compression
After steam reforming, the process gas, which contains a mixture of hydrogen, carbon monoxide, methane, and water vapor, leaves the reformer. To facilitate the next steps, the temperature of this gas is cooled to 41 degrees Celsius. Next, the synthesis compressor comes into action and increases the pressure of the process gas to 80 bar.
Third Step: Synthesis of Methanol
At this stage, we see the conversion of hydrogen and carbon dioxide into methanol. Methanol synthesis reactors are where these chemical reactions take place. In these reactors, the following equations are carried out in the presence of catalysts:
CO2 + 3H2 → CH3OH + H2O
CO + H2O → CO2 + H2
The result of these reactions is crude methanol and residual process gases. Methanol reactors are Boiling Water Reactor type and boiling water is used to control the reaction temperature. After passing through the reactors, the synthesis gas is cooled to 65°C.
Fourth Step: Separation of Methanol
Process Overview
In this stage, crude methanol is separated from the synthesis gas. The remaining gases, including hydrogen, carbon monoxide, and methane, are recycled back to the methanol reactor to be reused in the production cycle. The extracted crude methanol is sent to purification and distillation units to remove impurities and water, producing pure methanol.
Key Process Points:
- Steam-to-carbon ratio in reforming is 2.5.
- The pre-reformer catalyst contains nickel.
- The methanol synthesis loop is designed for a maximum pressure of 105 bar.
- Three methanol reactors operate in parallel, and two feed/exit heat exchangers also operate in parallel.
- Purified synthesis gas contains minor impurities such as inert gases and off-gases from the methanol synthesis process.
- A separation unit is used to separate impurities from crude methanol.
- The gas reforming and methanol synthesis process is a complex, multi-stage process that requires:
- Advanced equipment and technology.
- High energy consumption.
- Production of greenhouse gases like carbon dioxide.
- Expensive and sensitive catalysts.
Despite these challenges, this process plays a crucial role in methanol production, which has numerous applications in various industries, including the production of synthetic resins, solvents, fuels, and chemicals. Research is ongoing to improve this process and increase efficiency, reduce energy consumption, and decrease greenhouse gas emissions.
Simulation of Industrial Reforming Unit Using Aspen Plus
In this industrial project, we investigate the simulation of an industrial reforming unit using Aspen Plus version 14. Aspen Plus was chosen due to the integration of simulation resources and its database, allowing us to compare simulation results more accurately. In this simulation, no solid metallic compounds were used. Instead, the Soave-Redlich-Kwong (SRK) equation was used to estimate the behavior of gaseous and liquid compounds in the system. The information used for the simulation includes flow information, equipment specifications, and operating conditions from Petrochemical FAN AVARAN documents and data. In this project, we examine the simulation of this complex process using Aspen Plus version 14. Aspen Plus, due to the integration of simulation resources and its database, is a suitable tool for a more accurate comparison of simulation results.
Pre-Treatment Stage:
In this stage, natural gas enters the separation unit, and the condensates present in it are separated, The table below compares the input natural gas flow (stream 2000) to the unit with the simulation.
The Gas is Then Divided Into Two Parts:
one part for furnace fuel and the other part for reforming feed. The reforming feed is preheated, and its pressure is increased to improve process efficiency and protect the catalysts.
Desulfurization Stage: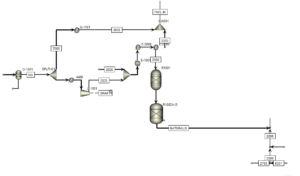
Due to The Sensitivity of Catalysts to Sulfur, Desulfurization is Done in Three Stages:
First step: removal of hydrogen sulfide
Second step: demercaptanization
The third step: removing the remaining sulfur compounds
In the simulation, two reactors have been used for desulfurization.
Reforming Stage:
In this step, the desulfurized feed is mixed with steam. The steam to carbon ratio is adjusted to optimize the process. The mixture of feed and steam enters the Pre-Ref reactor. In this reactor, ethane in the feed is converted to methane. Then, in the main reforming reactor (Gibbs reactor), methane reacts with water vapor and hydrogen, carbon monoxide and carbon dioxide are produced. The simulation results are consistent with industrial data.
Cooling and Compression Stage:
Cooling and Compression
The high-temperature effluent from the reformer is cooled to prevent equipment damage. Condensates present in the synthesis gas are separated from the bottom of the separator. The cooled synthesis gas is cooled again, and its condensates are separated before entering the methanol synthesis reactor. Finally, before entering the synthesis reactor, the pressure is increased in two stages using compressors. In the first stage, the pressure is increased to 60 bar, and in the second stage, after cooling and separating the water present in the gas, the pressure is increased to 80 bar.
Methanol Synthesis Stage:
Synthesis gas flow along with the return flow of synthesis gas enters the methanol synthesis kinetic reactor. Reactor temperature, height and diameter of tubes are adjusted to optimize the process. In this reactor, hydrogen and carbon monoxide are converted into methanol and water with the presence of a catalyst.
Methanol Separation Step: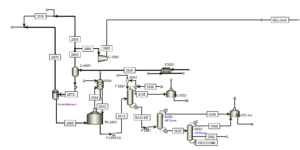
Methanol Synthesis and Separation
The effluent from the methanol synthesis reactor is cooled and passed through a heat exchanger. The synthesis gases present in the stream are separated from the top and returned to the synthesis reactor. Methanol, along with water, is removed from the bottom of the separator. The crude methanol is purified in three RadFrac columns, producing 96 tons per hour of methanol with a purity of 99.9%.
Validation Results
As mentioned, this simulation was conducted using official information from Petrochemical FAN AVARAN. The best parameter for validating the reforming reactor is the results of the outlet streams and comparing them with industrial data. The table below shows the validation results of the outlet stream from two reforming reactors in the simulation (stream 2320).
Based on the results reported in the tables, the average percentage error obtained from the simulation is 2.9%. This error value is acceptable for the simulation of an industrial process , This error value is very good and indicates that the simulation is accurate and the assumptions used in the software are correct.
This simulation was also conducted to evaluate and validate a design and evaluation project of an integrated process for the simultaneous production of hydrogen and synthesis gas for methanol production with an industrial sample.
Conclusion:
The simulation of an industrial reforming unit using Aspen Plus is an important step towards a deeper understanding of this complex process and its optimization for more efficient and sustainable methanol production. Using this powerful tool, it is possible to more effectively reduce energy consumption, minimize pollution, and improve the quality of the final product. It also provides the best solutions to improve efficiency and reduce energy consumption.
Simulation of The Reforming Process With Aspen Plus Software
In this project, the simulation of an industrial reforming process at Petrochemical FAN AVARAN for methanol production has been modeled using Aspen Plus version 14.