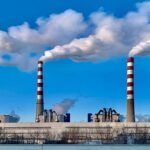
Conducting FEED Studies for Industrial and Execution Projects
مهر ۴, ۱۴۰۳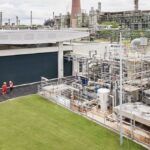
CO₂ Reduction and Syngas Production in Industry
مهر ۴, ۱۴۰۳Introduction
The oil, gas, petrochemical, power, and steel industries are critical to the global economy. However, these sectors are also significant contributors to greenhouse gas (GHG) emissions, which drive climate change. Optimizing processes in these industries can substantially improve efficiency while reducing GHG emissions. This article explores various methods that can be used to optimize these industries and mitigate their environmental impact.
Importance of Optimization
- Reducing Greenhouse Gas Emissions: Optimization in these industries can significantly cut down GHG emissions, helping to combat climate change.
- Cost Reduction: Many optimization initiatives can lead to cost savings, for example, by reducing energy consumption or minimizing waste.
- Increased Profitability: Enhancing efficiency and cutting costs can lead to higher profitability for these industries.
- Improved Competitiveness: Companies that are leaders in optimization can gain a competitive edge in the market.
- Job Creation: Optimization can result in new job opportunities, especially in areas such as new technologies, engineering services, and construction.
Challenges Ahead
- High Initial Costs: Some optimization measures may require substantial upfront investment.
- Technical Complexity: Certain optimization methods are technically complex and require specialized expertise.
- Resistance to Change: Employees and stakeholders may resist changes brought about by optimization efforts.
Solutions
- Government Support: Governments can encourage optimization through financial incentives and subsidies.
- Industry Collaboration: Companies can collaborate by sharing best practices and cooperating in research and development projects.
- Raising Awareness: Increased awareness of the benefits of optimization can encourage companies and stakeholders to adopt these measures.
Software Optimization
The oil, gas, petrochemical, and refinery industries are among the most complex and vital sectors in any country. Given the potential risks and economic considerations, optimizing processes in these industries is of paramount importance. Software plays a crucial role in managing and controlling these processes, and optimizing the use of software can lead to enhanced efficiency, cost reduction, improved safety, and environmental protection.
Process Simulation and Modeling
Software-based simulations are used to accurately model various processes in the oil, gas, petrochemical, and refinery industries. These tools allow engineers to simulate process behavior under different conditions, identifying optimal operating conditions for maximum efficiency and minimal cost.
Supply Chain Optimization
The supply chain in these industries is intricate and widespread. Optimizing this supply chain can result in significant cost reductions, increased inventory availability, and improved customer service. Numerous software solutions are available to help companies plan production, manage transportation, warehousing, and other supply chain activities.
Asset Management
Managing physical assets such as pipelines, storage tanks, pumps, and turbines is crucial in the oil, gas, petrochemical, and refinery industries. Asset management software can assist companies in tracking the condition of their assets, scheduling maintenance, and optimizing asset utilization.
Predictive Maintenance and Fault Management
Equipment failures in the oil, gas, petrochemical, and refinery sectors can result in significant financial and environmental losses. Predictive maintenance software analyzes sensor data and other sources to predict equipment failure, allowing companies to schedule preventative maintenance.
Energy Consumption Optimization
These industries are some of the largest energy consumers globally. Energy optimization software helps companies identify and reduce unnecessary energy use, leading to cost savings and reduced GHG emissions.
Example
Company X used process simulation software to model its refining processes. The software revealed that a slight adjustment in process settings could reduce energy consumption by 10%, leading to significant cost savings and a substantial reduction in GHG emissions.
Benefits of Software Optimization
- Increased Efficiency and Productivity
- Reduced Operating and Capital Costs
- Improved Safety and Environmental Performance
- Enhanced Product Quality
- Greater Customer Satisfaction
Common Optimization Software in the Oil, Gas, Petrochemical, and Refinery Industries
Aspen HYSYS
- One of the most popular process simulation software globally.
- Used for simulating a wide range of processes across various industries, including oil, gas, petrochemical, and refineries.
- HYSYS can simulate thermodynamic processes, adsorption, distillation, reactors, and heat exchangers.
ProSim
- A powerful software for process simulation and optimization.
- ProSim features an intuitive and user-friendly interface.
- The software offers a wide range of capabilities for process simulation, sensitivity analysis, and optimization.
UniSim
- Comprehensive software for process simulation and management.
- UniSim includes a full suite of tools for process simulation, data management, analysis, and optimization.
- Widely used across industries, including oil, gas, petrochemical, and refineries.
Petrosim
- Specialized software for refining process simulation and optimization.
- Petrosim includes a complete suite of tools for simulating refinery units, analysis, and optimization.
- Designed specifically to meet the needs of the refining industry, it can be effectively used for simulating complex refining processes.
AVEVA SimCentral
- An integrated platform for simulation, process management, and engineering.
- SimCentral offers a complete set of tools for process simulation, data management, analysis, optimization, and engineering.
- Suitable for a wide range of industries, including oil, gas, petrochemical, and refineries.
Supply Chain
- SAP Supply Chain Management
- Oracle E-Business Suite
Asset Management
- IBM Maximo Asset Management
- GE Digital Asset Management
- Schneider Electric EcoStruxure Asset Management
- Siemens PlantSight
Predictive Maintenance and Fault Management
- Many of the asset management tools mentioned also serve predictive maintenance purposes.
Energy Optimization
- Many process simulation tools like HYSYS and UniSim have modules for energy optimization.
- Specialized software like Schneider Electric PowerSCADA and Siemens Energy Manager are also available for this purpose.
By integrating advanced software tools into the operations of oil, gas, petrochemical, and refining industries, companies can significantly improve efficiency, reduce emissions, and enhance overall operational performance.
Optimization of Design, Operations, and Process Control in Production
Now, let’s delve deeper into the optimization of the oil, gas, petrochemical, power plant, and steel industries, focusing on three key areas: design optimization, operational optimization, and process control optimization.
Design Optimization
1. Equipment Design:
- Use of Modern CAD/CAM Software: Advanced CAD/CAM software allows for more precise and optimized equipment design, minimizing errors and resource waste during manufacturing and production phases.
- Stress and Fatigue Analysis: By applying stress and fatigue analysis, weaknesses and stress points in the equipment design can be identified and adjusted to enhance strength and longevity.
- Material Selection: Choosing the right materials based on operational conditions and technical requirements plays a crucial role in improving the efficiency, durability, and stability of equipment.
2. Process Design:
- Modeling and Simulation: Using process simulation software enables virtual modeling of production processes, identifying the most efficient paths for maximizing output, minimizing energy consumption and emissions, and ensuring high product quality.
- Control and Monitoring System Design: The implementation of smart control and monitoring systems provides real-time, precise oversight of production processes, helping operators monitor effectively and react promptly to any issues.
- Supply Chain Management Design: Optimizing the supply chain through ERP and SCM systems ensures timely access to high-quality raw materials, reducing costs and increasing overall production efficiency.
Operational Optimization
1. Asset Management:
- CMMS Implementation: A Computerized Maintenance Management System (CMMS) enables proactive scheduling and execution of preventive maintenance programs, preventing equipment breakdowns, production halts, and additional costs.
- Operational Data Analysis: By collecting and analyzing operational data, inefficiencies can be identified, and necessary improvements can be made to enhance production performance.
- Risk Management: Implementing risk management systems helps identify, assess, and manage risks associated with production processes, preventing disruptions and financial losses.
2. Energy Consumption Optimization:
- Use of Energy-Saving Technologies: Adopting modern technologies like heat recovery systems, LED lighting, and high-efficiency drives significantly reduces energy consumption in production processes.
- Process Optimization for Higher Efficiency: Reviewing and adjusting production processes can eliminate energy waste and increase overall efficiency.
- Incentive Programs for Energy Saving:
- Reward Programs: Offering rewards for employees based on energy-saving achievements encourages the adoption of more efficient practices.
- Energy-Saving Competitions: Organizing competitions among company departments to save energy fosters a competitive spirit, motivating employees to strive for further reductions in energy consumption.
- Educational Programs: Providing necessary training on energy-saving practices helps employees understand the importance of reducing energy consumption and adopting appropriate behaviors.
Process Control Optimization
1. Control and Monitoring Systems:
- DCS Systems: Distributed Control Systems (DCS) allow precise control and real-time optimization of production processes.
- SCADA Systems: Supervisory Control and Data Acquisition (SCADA) systems enable remote monitoring and control of production processes, improving oversight.
- PLC Systems: Programmable Logic Controllers (PLC) allow for automated control and sequencing of production operations.
2. Control Algorithm Optimization:
- Advanced Control Algorithms: Implementing advanced control algorithms such as fuzzy control, neural control, and adaptive control can significantly enhance the accuracy and efficiency of control systems.
- Control Parameter Optimization: Fine-tuning control parameters ensures optimal control system performance, preventing fluctuations and instability in production processes.
- Control Data Analysis: Collecting and analyzing control data helps identify weaknesses and inefficiencies in control systems, facilitating improvements.
Conclusion
Optimizing design, operations, and process control in oil, gas, petrochemical, power plant, and steel industries is key to enhancing efficiency, productivity, reducing costs, and increasing the dynamism of these sectors. By employing innovative and advanced solutions, industries can effectively overcome challenges and move toward a sustainable and profitable future.
Optimization for Greenhouse Gas Emission Reduction
As discussed earlier, the oil, gas, petrochemical, power plant, and steel industries play a critical role in the global economy. However, they also contribute significantly to greenhouse gas emissions and are recognized as major contributors to global warming.
Reducing greenhouse gas emissions in these industries is vital to combating climate change and preserving the planet for future generations. Optimization is the key to achieving this goal. Through innovative and advanced solutions, processes can be optimized to reduce energy consumption, prevent resource waste, and consequently curb greenhouse gas emissions.
This article delves deeper into optimization in oil, gas, petrochemical, power plant, and steel industries, focusing on reducing greenhouse gas emissions.
Oil, Gas, and Petrochemical Industry
1. Refinery Process Optimization:
-
Carbon Capture and Storage (CCS):
- Example: The “Boundary Dam” project in Canada captures 1 million tons of CO2 annually from a coal-fired power plant’s chimney and stores it underground.
- Benefits: This technology effectively eliminates CO2 emissions from oil, gas, and petrochemical refining processes.
-
Hydrogen as an Energy Carrier:
- Example: “Japan Petroleum Exploration” is developing projects to produce and use hydrogen as a clean fuel in refineries.
- Benefits: Hydrogen can completely replace fossil fuels, bringing greenhouse gas emissions to zero.
-
Burner Optimization:
- Example: The National Iranian Oil Company has reduced greenhouse gas emissions significantly by optimizing burners in its facilities.
- Benefits: Optimizing burners prevents the waste of natural gas and methane, which is a potent greenhouse gas.
2. Pipeline Optimization:
-
Leak Reduction:
- Example: “Saudi Aramco” actively monitors and fixes leaks in its pipelines using advanced technologies like flying robots and laser sensors.
- Benefits: This helps prevent the wastage of natural gas, methane, and environmental pollution.
-
High-Efficiency Pipelines:
- Example: “TransCanada” uses pipelines with a smooth internal coating in its Keystone XL pipeline, reducing friction and helping save energy, which lowers greenhouse gas emissions.
- Benefits: This greatly reduces pipeline losses and prevents natural gas wastage.
-
Underground Gas Storage:
- Example: Germany uses underground natural gas storage to store excess gas produced in summer for use in winter.
- Benefits: This helps maintain grid stability and prevents gas wastage during periods of surplus production.
Power Plants
1. Electricity Generation Process Optimization:
-
Renewable Energy Sources:
- Example: China is investing heavily in renewable energy sources like solar and wind power, and the share of these sources in its electricity generation is steadily increasing.
- Benefits: Using renewable energy instead of fossil fuels can significantly reduce greenhouse gas emissions from power plants.
-
Combustion Process Optimization:
- Example: “Duke Energy” has increased the combustion efficiency in its power plants using advanced control systems, significantly reducing greenhouse gas emissions.
- Benefits: Optimizing combustion processes effectively reduces fuel consumption and minimizes emissions.
-
Carbon Capture and Storage (CCS):
- Example: The “Petra Nova” project in Texas captures CO2 from a coal-fired power plant chimney and stores it underground.
- Benefits: This technology can effectively eliminate CO2 emissions from fossil-fuel-based power plants, especially coal-fired ones.
2. Grid Optimization:
-
Demand Management:
- Example: The “SmartRate” program by “Pacific Gas & Electric” offers consumers discounts during low-demand times, encouraging them to use less electricity during these hours.
- Benefits: This effectively reduces peak electricity demand, minimizes the need for fossil-fuel-based electricity generation, and lowers greenhouse gas emissions.
-
Grid Capacity Enhancement:
- Example: The European Union is investing in smart grid development and upgrading grid infrastructure to facilitate the transmission of renewable energy-generated electricity.
- Benefits: This helps prevent the waste of electricity generated from renewable sources and promotes the integration of more renewable energy into the grid.
Steel and Iron (MIDREX Process)
1. Melting and Casting Process Optimization:
-
High-Efficiency Melting Technologies:
- Example: “Tata Steel” in India uses high-efficiency electric arc furnaces and heat recovery systems in its steel melting processes, significantly reducing energy consumption and greenhouse gas emissions.
- Benefits: This effectively increases the efficiency of the melting process, preventing excessive energy consumption and emissions.
-
Use of Materials with Less Waste:
- Example: “SSAB” in Sweden uses steel scrap as the raw material in its steel production process, reducing the need for iron ore extraction and processing, which in turn minimizes greenhouse gas emissions.
- Benefits: Using scrap instead of raw materials helps conserve natural resources and reduce waste.
2. Gas Treatment Process Optimization:
- Example: “Baosteel” in China uses advanced gas treatment systems to remove pollutants from the flue gases of its steel melting process.
- Benefits: This effectively improves air quality and prevents the release of harmful greenhouse gases such as methane.
Conclusion
Optimizing the oil, gas, petrochemical, power plant, and steel industries with a focus on reducing greenhouse gas emissions plays a vital role in combating climate change and preserving the planet for future generations. By leveraging innovative and advanced solutions such as renewable energy, process optimization, and energy efficiency, significant reductions in greenhouse gas emissions can be achieved, paving the way toward a sustainable and healthy future.
Optimization: A Step Towards Improving Efficiency and Reducing Energy Consumption
Optimizing energy consumption in industries plays a key role in improving efficiency, reducing costs, preserving natural resources, and overall moving towards a sustainable future. With innovative and advanced solutions, the excessive use of energy in these industries can be curbed, significantly boosting their dynamism and profitability. In this article, we delve deeper into energy optimization in the oil, gas, petrochemical, power, and steel industries.
Oil, Gas, and Petrochemical
Optimizing Refining Processes
-
Using High-Efficiency Heat Exchangers:
- Example: ExxonMobil, by using high-efficiency heat exchangers in its refineries, has significantly reduced heat loss and energy consumption.
- Benefits: This can effectively increase refinery process efficiency and minimize fuel consumption.
-
Advanced Monitoring and Control Systems:
- Example: Shell employs advanced monitoring and control systems to accurately monitor and control its refinery processes, preventing energy and raw material waste.
- Benefits: This can enable real-time energy optimization and prevent inefficiencies and wastage in the refining process.
-
Optimizing Separation Processes:
- Example: BP has optimized the separation processes in its refineries using modern methods like membrane and adsorption, reducing energy consumption and improving efficiency.
- Benefits: This can significantly reduce energy consumption in separation processes, contributing to more precise and higher-quality refining of raw materials.
Pipeline Optimization
-
Insulating Pipelines:
- Example: The National Iranian Gas Company, by insulating its gas transmission pipelines, has effectively reduced heat loss and gas wastage.
- Benefits: This can efficiently save energy and reduce greenhouse gas emissions.
-
Using Leak Detection Systems:
- Example: Saudi Aramco employs advanced leak detection systems to accurately and quickly identify and fix pipeline leaks, preventing gas loss and environmental pollution.
- Benefits: This can effectively prevent gas wastage and air pollution, helping preserve natural resources.
-
Optimizing Pumping Stations:
- Example: TransCanada, by using high-efficiency pumps and smart control systems at its oil pipeline pumping stations, has significantly reduced energy consumption.
- Benefits: This can help save energy in the crude oil transmission process and lower operating costs.
Power Plants
Optimizing Power Generation Processes
-
Using High-Efficiency Turbines:
- Example: Siemens produces high-efficiency turbines for combined cycle power plants, significantly reducing fuel consumption and greenhouse gas emissions.
- Benefits: This can effectively improve power generation efficiency, saving resources, and reducing air pollution.
-
Heat Recovery Systems:
- Example: General Electric (GE) uses heat recovery systems in its power plants to capture waste heat from the power generation process and use it for heating water and pre-heating air for turbines, increasing efficiency.
- Benefits: This can efficiently save fuel and reduce greenhouse gas emissions.
-
Flue Gas Treatment Systems:
- Example: Mitsubishi Hitachi Power Systems uses advanced flue gas treatment systems to remove pollutants like particulate matter, sulfur oxides, and nitrogen oxides from smokestacks, helping improve air quality.
- Benefits: This can effectively prevent air pollution and harmful gas emissions into the environment.
Electricity Grid Optimization
-
Demand Management:
- Example: Pacific Gas & Electric (PG&E) encourages consumers to use less electricity during peak demand hours through demand management programs, promoting grid stability.
- Benefits: This can effectively prevent overloading the grid during peak demand hours and reduce power generation costs.
-
Smart Grid Technologies:
- Example: Enel in Italy uses smart grid technologies to accurately monitor and control its electricity grid in real-time, effectively preventing blackouts and voltage drops.
- Benefits: This can effectively enhance the stability and reliability of the electricity grid, preventing disruptions and power outages.
-
Integration of Renewable Energy Sources:
- Example: Germany, with significant investment in the development of renewable energy sources like solar and wind, steadily increases the share of these resources in its power generation, significantly reducing greenhouse gas emissions.
- Benefits: This can effectively diversify power generation sources, reduce dependence on fossil fuels, and move toward a sustainable, environmentally friendly future.
Energy Consumption Optimization
-
Utilization of Heat Recovery Systems:
- Example: Tata Steel in India uses heat recovery systems to recover waste heat from steel melting furnaces and utilizes it for heating water and preheating the air entering the furnaces.
- Benefits: This can significantly reduce energy consumption and increase the efficiency of the steel production process.
-
Use of LED Lighting:
- Example: US Steel has significantly reduced electricity consumption and minimized greenhouse gas emissions by replacing traditional lighting with LED lighting in its factories.
- Benefits: LED lighting has very low energy consumption and a much longer lifespan compared to traditional bulbs, contributing to economic savings and reducing greenhouse gas emissions.
-
Use of High-Efficiency Motors:
- Example: Nippon Steel in Japan employs high-efficiency motors in its equipment and machinery, significantly reducing electricity consumption and minimizing greenhouse gas emissions.
- Benefits: High-efficiency motors can effectively reduce energy consumption in various steel production processes.
Final Conclusion
Optimizing industries is a crucial step towards enhancing efficiency, sustainability, and profitability across various industrial sectors. By employing innovative solutions and advanced technologies, production processes can be optimized, energy consumption can be reduced, greenhouse gas emissions can be minimized, and a sustainable future can be achieved.
Benefits of Optimizing Oil, Gas, Petrochemical, Steel, and Power Industries:
- Increased Efficiency: Optimizing processes can reduce waste, increase yield, and save costs.
- Reduced Energy Consumption: Utilizing renewable energy sources and high-efficiency technologies can significantly lower energy consumption.
- Reduced Greenhouse Gas Emissions: Optimizing processes and using clean energy sources can significantly help mitigate climate change.
- Increased Sustainability: By optimizing resource consumption and minimizing environmental impacts, long-term sustainability can be achieved.
- Increased Profitability: By saving costs, increasing yields, and expanding into new markets, profitability can be enhanced.
Taking steps to optimize industries not only benefits the environment but can also be advantageous for companies and their stakeholders. By investing in industry optimization, a sustainable and prosperous future can be achieved while also increasing profitability.