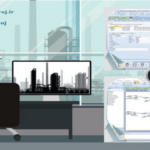
Comparison of Aspen Plus and HYSYS Software
مهر ۴, ۱۴۰۳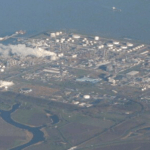
Gas Reception Unit in Refinery – Processes & Equipment
مهر ۵, ۱۴۰۳Introduction
A fluid that has particles with nano dimensions is called a nanofluid. These types of fluids are designed by suspended colloidal particles with nano dimensions in a base fluid. The base fluid that is usually used to prepare nano fluid is water, ethylene glycol and oil. Nanofluids have new properties that make them useful for heat transfer applications. These fluids show higher thermal conductivity and heat transfer coefficient than the base fluid.
Knowledge of the rheological behavior of nanofluid seems to be very important in order to decide on the suitability of nanofluid for heat transfer applications. There are two methods for preparing nanofluids: 1- two-step method 2- single-step method
Two-step method:
This method is widely used to prepare nanofluids. Nanoparticles, nanofibers, nanotubes or other nanomaterials in this method are first produced as dry powder by physical and chemical methods. In the second stage of the process, with the help of strong magnetic force stimulation, ultrasonic stimulation, high stress mixing, homogenization and ball milling, nano-sized powders are dispersed inside the fluid.
The two-step method is an economical way to produce nanofluids on a large scale; Because now the technologies of mixing nano powders for production at industrial levels have grown. Due to the high surface area and surface action of nanoparticles, these materials tend to form lumps. The most important method to increase the stability of nanoparticles in fluids is the use of surfactants. However, the efficiency of surfactants, especially for high temperature applications, is still a major concern.
One-step method:
In this method, the processes of drying, storing, transporting and dispersing nanoparticles are prevented, and as a result, the formed masses of nanoparticles are reduced and the stability of nanofluids increases. Single-step processes can disperse nanoparticles homogeneously and the particles can be stably suspended in the base fluid.
The use of heat exchangers with high efficiency is expanding in most small and large industries. Common energy-carrying fluids are fluids such as water, oils, and ethylene glycol. Therefore, there is a strong need to pursue and improve heat transfer fluids with a high thermal conductivity coefficient.
Advantages and applications
Heat transfer of nanofluid is better than base fluid; Because fine solid particles increase the heat conductivity of the mixture. Because heat transfer occurs on the surface of nanoparticles, it is desirable to use particles with a high specific surface area. Also, nanopowders have a higher specific surface compared to micron-sized particles.
On the other hand, the momentum of nanoparticles is very small. As a result, the momentum that they can transfer to the solid wall is very low and reduces the possibility of wear of components of heat exchangers, pipelines and pumps. These particles also have a high ability to move and move and create micro-displacement in the fluid and increase energy transfer in the fluid.
Also, because these particles are small, they have little weight and the possibility of settling in them is low. Reduction of sedimentation can be a problem in the use of suspensions; It means to remove the settling of particles. For example, spreading micron-sized particles in the microchannel will cause channel clogging.
In general, it can be said that nanofluid technology drives industries towards system miniaturization and, as a result, the design of lighter heat exchange systems. For example, to double the heat transfer coefficient of water, the pump power must be increased 10 times, but if a nanofluid with a thermal conductivity coefficient 3 times that of water is used, the heat transfer rate will be doubled.
Some of the advantages and potential capabilities of nanofluids are as follows:
- High specific surface area and subsequently more heat transfer surface between particles and fluids
- High dispersion stability due to the dominant effect of Brownian motion of particles
- Reduction of pump power compared to pure fluid in achieving heat transfer intensity
Simulation and modeling of nanofluids
In general, there are two different methods for modeling and investigating the increase of displacement heat transfer coefficient, the two-phase model and the single-phase model. The two-phase model is based on the concept of heat transfer in two phases, liquid and solid, but it requires long calculations and powerful computers.
The heat transfer coefficient increases with the decrease in the size of the particles, and this is not only due to the increase of the heat conduction coefficient due to the presence of nanoparticles, but also the random movement of the nanoparticles is considered an important factor in the increase of the heat transfer coefficient. . Maiga and colleagues studied the forced displacement of alumina-water and alumina-ethylene glycol nanofluids by the single-phase method in a circular tube and two parallel discs. The heat transfer coefficient increased by 63% and 45%, respectively. The increase in the heat transfer coefficient and viscosity of the dynamo was caused by the increase in shear stress in the wall.
Review studies:
Behzadmehr and his colleagues numerically investigated the forced displacement heat transfer in a circular tube with copper-water nanofluid. They used single-phase and mixed models and by comparing the three experimental values and the results of these models, they found that the accuracy of the mixed model is more than the single-phase model.
For the first time, Lotfi et al. used the Eulerian method for nanofluid simulation and compared the results with single-phase simulation and two-phase mixture model simulation. To simulate with the mixture model, they assumed that in a certain control volume, there is both volume percentage of base fluid and nanoparticles.
They also assumed that each phase has its own velocity vector. They tested the nanofluid containing AlO23 with an average diameter of 42 nm in a circular tube. The diameter of the pipe was 45 mm and its length was 970 mm. Reynolds number changed between 700 and 1800. It was assumed that the heater has a power equal to 300 watts. The simulation results were calculated for two different axial distances from the inlet. In this simulation, the single-phase method and the Euler model show the values of the Nusselt number to be lower than what it is.
Methods of increasing nanofluid stability
Based on the studies, in addition to using a lower mass percentage for nanofluids, there are three general methods to increase the stability of nanofluids.
1- Addition of surfactants: Adding surfactants to nanofluids is a simple and cost-effective way to increase the stability of nanofluids. Surfactants significantly affect the surface characteristics of the system. These materials contain a hydrophilic polar end and a hydrophobic end, usually a hydrocarbon chain.
Surface active substances are divided into four categories based on the composition of the hydrophilic head:
A) A non-ion that does not have a charged group in the hydrophilic head.
b) Anion with negative charge group
C) Cation with positive charged group
d) Amphoter, whose hydrophilic head charge can be positive or negative. To choose the appropriate surfactant, it should be noted that if the base fluid is polar, surfactants with hydrophilic head and otherwise surfactants which are soluble in oil are used. Although the use of surfactants is one of the common ways to improve the stability of nanofluids, adding these substances to nanofluids may cause problems such as creating foam and reducing the thermal conductivity of nanofluids. Also, the destruction of the bond between the surfactant and the nanoparticle at temperatures above 60 degrees Celsius, the stability of the nanofluid is lost.
2. Control: pH stability of a nanofluid is directly related to its electrokinetic properties. In such a way that if there is a high charge density on the surface of the nanoparticles, the nanoparticles will be stable in the fluid due to the electrostatic repulsion force. Therefore, it is possible to achieve optimal stability by adjusting the pH of nanofluid.
3. Ultrasonic vibration: In order to increase the stability of nanofluid, ultrasonic vibrators can be used.
Key properties of nanofluids
Among the key features of nanofluids that have been discovered so far are thermal conductivities that are much higher than conventional suspensions, the existence of a non-linear relationship between thermal conductivity and the concentration of carbon nanotubes in nanofluids, as well as the strong dependence of thermal conductivity on temperature and a significant increase in flux. called critical heat.
Each of these features in their place are very desirable for thermal systems and together, make nanofluids the best candidates for the production of liquid-based coolants. These findings also clearly show the existence of fundamental limitations in conventional heat transfer models for solid/liquid suspensions.
Among the factors of heat transfer in nanofluids are: the movement of nanoparticles, the liquid layered molecular surface at the interface between liquid and particles, projectile heat transfer in nanoparticles and the effect of nanoparticle clustering are among the factors of heat transfer in nanofluids.
A new project aimed at discovering the key parameters, which are missing in the existing theories and fundamental concepts of nanofluid heat transfer enhancement mechanisms, as well as discovering the theoretical basis for the abnormal increase in thermal conductivity of nanofluids was conducted in July 2000 with the support of the US Department of Energy and the Energy Science Center. The base was approved.
Discussion and results
According to what was mentioned above, nanofluid can be mentioned as a potential medium for heat transfer in various industries, including oil and petrochemical industries. Based on the researchers’ findings, it can be said that the heat transfer coefficient generally increases with the increase of Reynolds number, and at constant Reynolds number, the displacement heat transfer coefficient of nanofluid is greater than that of pure water fluid.
Also, the friction coefficients of nanofluid at constant Reynolds are in good agreement with the friction coefficients of pure water. Perhaps this is due to the use of very low volume density of nanoparticles in the base fluid, which did not cause many changes in the behavior of the fluid. This means that nanofluid does not cause a large pressure drop in practice and there is no need to replace or strengthen the pump.
In nanofluids, due to the small size of the particles, the problems caused by corrosion, impurity and pressure drop are greatly reduced, and the stability of fluids against sedimentation is significantly improved. Due to the high conductivity coefficient of nanoparticles, by distributing them in the base fluid, they increase the thermal conductivity coefficient of the fluid, which is considered one of the basic parameters of heat transfer. Also, nanoparticles improve mass transfer, but the exact mechanism of this phenomenon has not been determined yet and more research is needed. Due to the unique properties of nanofluids, they have many applications, and one of the most important of them is in heat transfer.
conclusion
The increase in thermal conductivity related to nanotubes is a step beyond the predictions made by existing theories. Recently, researches have been conducted on metal nanofluids containing copper nanoparticles with a diameter of less than 10 nm that were dispersed in ethylene glycol. By using the collected results, it has been possible to develop a new model of energy transfer in nanofluids, which depends on the nanoparticle size, structure and dynamic effect on the thermal properties of nanofluids.
This way of connecting different scientific disciplines and joint projects will lead to the discovery of new frontiers in thermophysics research for design and engineering in the field of cooling production. Research on nanofluids could lead to an unexpected breakthrough in liquid/solid hybrid systems for countless engineering applications, including cooling for cars and heavy trucks. One of the main effects of this research is to increase energy efficiency, make thermal systems smaller and lighter, reduce operational costs and clean the environment.