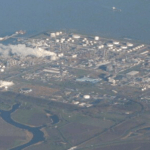
Gas Reception Unit in Refinery – Processes & Equipment
مهر ۵, ۱۴۰۳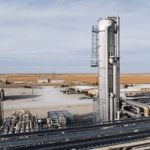
MEG Regeneration Unit
مهر ۵, ۱۴۰۳Gas Sweetening Unit
This unit is known by various names such as MDEA, gas operations, sweetening, etc., and is present in each Train. (Train originally means “train” or “railway,” and it is called this because the units are arranged consecutively.) Since there are four Trains in phases 2 and 3, there are four sweetening units in these two phases. In other words, as previously mentioned, phase 2 includes Trains 1 and 2, and phase 3 includes Trains 3 and 4. Since each Train has a sweetening unit installed, the sweetening unit in Train 1 is named 101, the unit in Train 2 is named 201, and similarly, the sweetening units in Trains 3 and 4 are named 301 and 401, respectively.
Main Purpose of the Sweetening Unit
The main goal of this unit is to remove hydrogen sulfide gas (H2S) from the incoming sour and wet gas. This gas is mixed with the main gas from unit 100 and compressed by the Off.Gas compressors from the Condensate Stabilization unit and delivered to the Trains. The removal of H2S is done using MDEA (Methyl-Diethanolamine), which is specifically used for effectively absorbing H2S from natural gas.
Gas Separation Process
The sour gas entering from the HP Separators, with a pressure of 2/69 Barg and a temperature of 24°C, enters the liquid collection vessel. Here, the liquid particles are separated from the gas and sent to the condensate stabilization unit. The outgoing gas then enters a coalescer filter and is directed to the Amine Absorber column for the sweetening process.
Amine Absorber Column
The absorber column, which is of tray-type with 30 trays, facilitates contact between the gas entering from the bottom and the clean amine (Lean Amine) from the top. The sweetened gas exits from the top of the column and moves to the dehydration unit. Meanwhile, the rich amine (Rich Amine) exits from the bottom and is sent to the Flash Drum for gas separation.
Amine Regeneration Process
After gas separation, the rich amine enters the amine/amine exchangers, where it comes into contact with the hot, clean amine. The rich amine then enters the amine regeneration column at 110°C. This column is also tray-type with 24 trays, and the incoming amine is injected onto the 23rd tray.
Temperature and Pressure Control
The working temperature of the amine regeneration column varies between 111°C at the top and 132°C at the bottom. temperature control is done by the steam from the reboiler. clean amine, after regeneration, is cooled in the amine/amine exchangers and finally enters the Amine Surge Tank at 45°C.
Managing Foaming Phenomenon
One of the potential issues in the absorber columns is foaming, which can be caused by solid particles or hydrocarbons present in the incoming gas. To prevent foaming, anti-foam is intermittently injected into the amine feed line.
Skimming Procedure
If hydrocarbons are present in the absorber column, the skimming procedure is performed to remove them. This is done by using dedicated skimming lines at the bottom of the absorber and Flash Drum to drain the hydrocarbons.
Specifications for the Sweetened Gas
The sweetened gas must meet the following specifications:
- H2S content of about 3 ppm by volume.
- CO2 content of about 2 molar percent.
- Mercaptan content of about 15 mg/m3.
Amine Filtration Units
Amine filtration units are used to purify the amine and separate solid particles and insoluble hydrocarbons. The amine first passes through the Precoat filter, where any solid particles, such as iron sulfide, are removed. Then, the amine goes through a charcoal filter and a cartridge filter to remove hydrocarbon particles and particles larger than one micron, ensuring no foaming occurs in the absorber column.