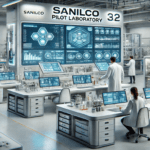
Design and Construction of Industrial Laboratory Pilots
دی ۶, ۱۴۰۳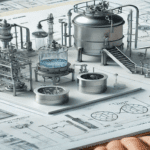
Design of Semi-Industrial and Laboratory-Scale Process
دی ۷, ۱۴۰۳Introduction
The Exploitation of laboratory pilots is a critical step in research and development as well as in optimizing industrial processes. This phase involves commissioning, operation, monitoring, and performance evaluation of equipment and processes on a small scale. The primary goal of using pilots is to accurately simulate operational conditions, collect relevant data, and ensure proper equipment performance before scaling up to larger industrial levels. This article explores the steps involved in utilizing laboratory pilots, the challenges faced, and optimal solutions for conducting this process effectively.
Objectives of Pilot Plant Systems in Industries
laboratory pilots is a pre-commercial production system that uses new technologies to produce small volumes of products based on innovative processes. The primary purpose of pilot plant systems is to identify and resolve process-related issues before scaling up to industrial production. These small-scale production systems are utilized to test and validate new technologies prior to commercialization. Generally, the main motivation for constructing and operating pilot plants is to explore and understand new technologies. Many advanced treatment and wastewater recycling processes, such as zero-liquid discharge systems and blowdown treatment of cooling towers or boilers, are initially tested in pilot plant systems.
Key Considerations for Successful Pilot Plant Operation
-
Simulation Before Construction
Simulating the pilot system before construction is essential. Modeling and simulation techniques may include:
-
- Chemical simulation studies
- Mathematical modeling
- Aspen Plus/HYSYS modeling
- Computational Fluid Dynamics (CFD)
- Finite Element Analysis (FEA)
-
Chemical Balance in the System
Reactions are inefficient until equilibrium is achieved.
-
Material Properties
- Materials should not affect reactions, degrade over time, or incur unnecessary costs.
- Fluids must maintain proper Reynolds numbers for heat transfer.
- Reaction temperatures must be controlled.
- Proper selection of piping and instrumentation is critical.
Pilot Plant Design Methods
Designing a pilot plant is a complex process directly linked to testing and optimizing production methods. The design approach depends on the industry type, specific testing goals, and project scale. Below are the primary methods for pilot plant design:
1. Process-Oriented Design
This method focuses primarily on production processes and their optimization. It is widely used in industries such as chemicals, pharmaceuticals, and oil & gas.
2. Product-based design
In this method, the pilot design is based on the characteristics of the final product. This method is commonly used in the food, pharmaceutical, and chemical industries where the final product has specific characteristics (such as particle size, chemical composition, or physical properties).
3. Modular Design
In this method, the pilot plant design is done in a modular manner. That is, the pilot plant is divided into different sections (modules), each section operating independently and can be changed based on the need.
4. Demand-Driven Design
This method is designed based on the specific needs and demands of the market and production. Here, pilot plants are built to test new processes with real production demand and are specifically built to solve problems or optimize processes.
5. Lab-to-Industry Design
This method is used to transfer a process from the laboratory scale to the industrial scale. In this case, the results obtained from the initial experiments on the laboratory scale are used to design the pilot.
The steps required to design and build a pilot system are:
1) Select your scale designer
2) Complete the design
3) Develop 3D modeling and simulation
4) Initiate automation in the pilot plant
5) Build and assemble the module
6) Install the completed system (can be in an existing facility)
It is important to note that pilot plants can only behave like, and even resemble, large-scale commercial units on a small scale. This misconception of uniformity can lead engineers to design their pilot facilities with the same equipment and specifications as commercial-scale plants. Although both systems use the same engineering principles and have similar electrical and control systems, this is a challenge because the results of pilot research can impose some unnecessary costs.
Pilot Plant Operations in Industry
Step-by-Step Pilot Plant Operation Operating a Laboratory Pilots is a complex process that includes various stages, from design and construction to testing, optimization, and scaling up to larger production systems. This article explores these stages and highlights key points in the operation of pilot plants.
1. Preparation and Initial Design (Pre-Commissioning)
- Process Design
Before construction and installation, the overall production process must be carefully designed. This includes defining key process parameters such as temperature, pressure, flow rates, and material ratios. Equipment and raw materials should be selected based on process needs and testing objectives. - Documentation and Standards Review
Safety, environmental, and quality standards must be reviewed and documented to ensure all stages are carried out safely and effectively.
2. Construction and Installation
- Site Selection
Choosing the right location is critical. The site should accommodate equipment installation and provide access to essential resources like water, electricity, and gas. - Equipment Installation and Calibration
Various components such as reactors, pumps, tanks, and control systems are installed and calibrated to ensure proper functionality during experiments. - Initial Testing of Installations
Before starting experimental production, systems must be tested to verify correct installation and identify any technical issues.
3. Initial Testing
- Pilot Startup
Small batches of raw materials are used to evaluate system performance and process flow. - Testing Temperature, Pressure, and Flow Rates
Heating, cooling, and purification systems are tested under varying conditions. - Analysis of Results
Data from initial tests is analyzed to optimize the process and make necessary adjustments.
4. Operational Phase and Optimization
- Process Adjustments
Process parameters such as temperature, pressure, material ratios, and reaction rates are optimized for maximum efficiency and quality. - Managing Variations
Continuous monitoring is essential to address fluctuations and ensure consistent operation. - Data Analysis
Data collected during operations is analyzed to fine-tune processes and improve performance.
5. Quality Control and Safety
- Material and Product Quality Control
Raw materials and final products undergo tests to measure composition, physical and chemical properties, and safety. - Environmental and Safety Standards
Safety systems must remain active at all times. Temperature, pressure, and environmental conditions must be carefully controlled. Staff must also undergo safety training to handle potential hazards.
6. Scalability Testing
- Simulating Large-Scale Production
Tests simulate larger production scales to evaluate whether the process can maintain performance when scaled up. - Cost and Resource Analysis
Economic evaluations, including energy consumption, raw material usage, and labor costs, are conducted to estimate the feasibility of large-scale production.
7. Feedback and Continuous Improvement
- Process Reviews and Improvements
Even after scaling up, processes should be monitored continuously, and feedback from real operations should be incorporated to improve cost efficiency, productivity, and quality. - Documentation and Reporting
All stages, changes, and findings should be documented, including daily reports, test results, and data analyses.
Benefits of Pilot Plant Operation
- Risk Reduction: Identifies potential issues in small-scale simulations before full-scale implementation.
- Cost Optimization: Reduces final production costs through process testing and optimization.
- Innovation and Technology Development: Provides a platform to test new technologies and production methods.
Challenges and Limitations of Pilot Plant Operations
- Scale Limitations
Pilot plants may not fully replicate the complexity of industrial-scale processes. - Economic Constraints
Setting up and maintaining a pilot plant requires significant investment, which can be challenging for some industries.
SANILCO Services
Pilot plants can be designed using different approaches, including process-oriented, product-focused, modular, demand-driven, or lab-to-industry methods. The choice of design depends on industry type and testing goals, which significantly influence the success of large-scale implementation.
Companies often require expert consultation and support to ensure the success of pilot plant design and operation. This is where SANILCO plays a critical role. SANILCO offers design, construction, and commissioning services for pilot plants across industries, helping companies scale their production processes efficiently and effectively.