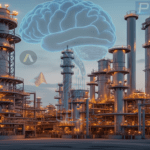
Application of Artificial Intelligence in Process Engineering
آذر ۶, ۱۴۰۳
The Challenge of Water and Steam Waste in the Steel and Iron Smelting Industries
آذر ۹, ۱۴۰۳Introduction
Laboratory and semi-industrial equipment play an essential role in research and development in various engineering fields, especially in chemical and oil and gas engineering. These devices allow researchers and engineers to simulate chemical processes on smaller scales and obtain more precise scientific data. The design, purchase and manufacture of these equipments require technical and specialized knowledge in order to meet the needs of laboratories in the best possible way.
Due to the ever-increasing advances in science and technology, choosing the right and quality equipment can help to improve the performance of the laboratory and increase the accuracy of the test results. Therefore, paying attention to details in the process of designing and manufacturing this equipment is of great importance.
Among the key equipment in this field, we can mention reactors, ovens, distillation devices and other advanced tools. As the heart of chemical processes, reactors allow chemical reactions to take place under controlled conditions. Ovens are also used for drying and heating samples. Distillation devices are particularly important as a tool for separating different compounds in the production and purification processes of chemicals.
Design of Semi-Industrial Units
The design of semi-industrial units is an important and complex process. which includes a set of engineering steps and principles. These types of units are usually on a smaller scale than full industrial units and on a larger scale than small workshops. In the following, some key aspects of the design of these units are discussed:
1. Analysis of Needs
– Identification of goals: determining the main goals of the semi-industrial unit, including the type of products, production capacity and target market.
– Market analysis: examining the needs of customers and competitors to determine the required products and services.
2. Process Design
– Choosing technology: choosing the right technology for the production of goods according to the volume of production and costs.
– Material flow: designing an efficient system for the movement and storage of raw materials and finished products.
3. Equipment Design
– Selection of machinery: identification and selection of machinery and equipment necessary for production. This includes main equipment, peripherals and control systems.
– Designing control systems: creating automatic control systems to optimize processes and reduce errors.
4. Space Design
– Unit layout: designing a suitable layout for equipment and work spaces in order to increase productivity and safety.
– Work environment: attention to creating a safe and comfortable work environment for employees.
5. Cost Management
– Cost estimation: calculation of investment costs, operational costs and equipment maintenance costs.
– Economic analysis: conducting economic analysis to evaluate profitability and return on investment.
6. Standards and Rules
– Compliance with standards: ensuring that the design is in accordance with national and international standards.
– Environmental considerations: paying attention to the environmental effects and complying with the laws related to environmental protection.
7. Testing and Optimization
– Testing: producing the initial sample and checking performance and efficiency.
– Process optimization: using feedback to improve and optimize the design.
Oil, Gas and Petrochemical Laboratory
The oil, gas and petrochemical laboratory is one of the suitable laboratory environments that are used to test the components of products such as fuel, crude oil, gas, oil, and crude oil, which requires specialists with suitable equipment and supplies for this work.
List of Oil, Gas and Petrochemical Laboratory Equipment
Currently, oil, gas and petrochemical laboratory equipment includes various tools that are generally divided into two categories: rotary laboratory equipment (such as turbines, compressors, and pumps) and stationary equipment (such as storage sources).
But in general, this laboratory equipment includes the following:
Petroleum and petrochemical laboratory equipment that are used to control the quality and test of petroleum materials and products (such as grease, oil, gasoline, wax, and diesel) are mentioned in the following section.
Petrochemical Laboratory
The petrochemical laboratory is also one of the most common and suitable laboratory environments that are always used to test and test petrochemical aspects (such as measuring characteristics related to behavior and physics, flash point, viscosity, etc.) of special equipment and petrochemical laboratory equipment.
It should be noted that when analyzing and testing the chemical properties of petrochemical materials, it is better to use elemental analyses such as sulfite analyzers, combustion analyzers, and mass spectrometers. For physical tests and analyses, devices such as flash point testers, rheometers, and viscometers should be used.
Laboratory Reactor
A laboratory reactor is a device in a laboratory where raw materials are converted into products during chemical reactions. In this device, parameters such as pressure and pH can be controlled at the same time as controlling the temperature of the materials in the reaction container. Laboratory reactors have different types such as discontinuous, semi-continuous and tubular.
In fact, the chamber laboratory reactor is designed to carry out chemical reactions that are carried out simultaneously with temperature and pressure control. In the laboratory, this device has a tank to pour the materials that need to react chemically and create the product material. and a mechanical stirrer for mixing these materials. The reactions inside the reactor are carried out under controlled conditions of temperature and certain pressure. The reactions of composition, decomposition and transformation are among the reactions that are carried out in this device.
Laboratory Reactor Components
The components of the laboratory reactor are boiler, heat exchanger (condenser), separator (separator), inputs and outputs, electric motor, valves and instruments. Its first component is a tank as mentioned. into which the reactants are poured. The desired gas is introduced into this reactor by paths called purging. The motor and propeller inside the reactor provide the possibility of mechanical stirring of the reacting materials.
A two-purpose control system (increasing or decreasing temperature), fixing the device is built into this device. In this way, by increasing the solution inside this reactor, the temperature decreases and cooling is done by the cooling coil. But when we have a temperature decrease in the reactor, the thermal jacket outside the reactor can gradually increase the temperature of the solution inside the device, in other words, the heating of these materials is done by the reactor body. Also, a pressure reducing valve (Relief) is installed in this device, which works in case of high pressure inside the reactor.
Types of Laboratory Reactors
Discontinuous Laboratory Reactor:
This reactor is used in the chemical industry and for the production of chemicals, where there is no entry or exit of any material during the chemical reaction. The working method in this reactor is that with the introduction of reactants. And carrying out the reaction during the reaction, the discharge of substances that did not participate in the reaction is carried out. This reactor has a simple structure. It has a small control system and is used in long-term chemical reactions.
Semi-Continuous Laboratory Reactor:
The semi-continuous laboratory reactor has a mixing tank and equipment similar to the continuous reactor. But in this reactor, unlike the continuous reactor, raw materials can be added to it and the product can be regenerated. In this reactor, raw materials can be added in a small amount at the beginning, and then, as the reaction progresses, more materials can be added to it little by little.
Plug Flow Laboratory Reactor:
In the plug flow reactor, the chemical reaction and conversion of raw materials into products is more than the performance of the reactor. Also, continuous and stable flow is done inside it. and the flow of liquids in it, in the form of solid branches. and it is a piston, and the reaction time is the same in all the sections of the pipes. The supply of driving forces in plug flow reactors decreases with the progress of the reaction, and this characteristic is similar to a batch reactor. In the tubes of this type of reactors, liquids can have a smooth or turbulent flow, and the turbulent flow is preferred to the smooth flow due to the improvement of heat transfer.
Mixed Industrial Reactors:
In the mixed industrial reactor, the materials are mixed in the tank after entering it, and then they leave the reactor after staying inside it for a certain period of time. In these reactors, the temperature can be easily controlled and this is their characteristic. Also, in chemical reactions that require a lot of stirring, the mixed reactor is used.
Fluidized Bed Reactor:
The working method in the fluidized bed reactor is the passage of a liquid or gas through the solid granular material, which leads to the suspension of the solid material due to the high speed of passage. In this case, the solid behaves like a liquid and it is called fluidization process. This property of liquefying the solid, by passing at high speed, is one of the important properties of the fluidized bed reactor. This type of reactor is widely used in industry.
Laboratory Distillation
One of the separation processes used to separate liquid compounds based on differences in their boiling points is distillation. Laboratory distillation is typically performed on a small scale for research and educational purposes. In this type of process, specific tools are used, such as:
– Distillation Apparatus: This includes a condenser, and a collection vessel.
– Heating: Usually achieved with a burner or electric hot plate to heat the liquid.
Laboratory distillation can be divided into two types:
– Simple: Used for separating liquids with boiling points that differ by more than 25 degrees Celsius.
– Fractional: Used for separating liquids with close boiling points, utilizing a distillation column.
The semi-industrial type can also be divided into two forms:
– Continuous: In this method, liquids are continuously fed into the system, and the separation process occurs continuously.
– Batch: In this method, liquids are introduced into the system at designated intervals, and separation occurs after each batch is completed.
Batch Tray Distillation Column (Glass)
Device Specifications
Glass distillation column
Glass product tanks
Feed tanks made up glass
Cribriform tray
Boiler with heating element
Condenser
Rotameter for flow control
Temperature thermocouples
Sampling valves
Valves, links and pipes
Electrical box including displays and keys
Batch distillation refers to the use of distillation in batches, meaning that a mixture is distilled to separate it into its component fractions before the distillation still is again charged with more mixture and the process is repeated. This is in contrast with continuous distillation where the feedstock is added and the distillate drawn off without interruption. Batch distillation has always been an important part of the production of seasonal, or low capacity and high-purity chemicals. It is a very frequent separation process in the pharmaceutical industry
Automatic Distillation
This product is used for automatic measurement of distillation according to ASTM D86 standard for petroleum products at atmospheric pressure, ASTM D850 standard for industrial aromatic hydrocarbons and related materials, ASTM D1078 for volatile organic liquid distillation range.
Oil Vacuum Distillation Equipment
Vacuum Distillation device is used to measure the distillation number of oil at a temperature of 400 degrees under vacuum, which is in accordance with the ASTM D1160 standard.
Pour Point & Cloud Point Tester
The device for determining Pour Point and Cloud Point is in accordance with ASTM D97 and ASTM D2500 standards.
Flash Point Device
It is a device for measuring the ignition point of petroleum products, including diesel, fuel oil, oil and petroleum products. which exists in different models and according to ASTM D92 and ASTM D93 standards, it is available in different models of fully automatic and semi-automatic flash points and manual flash points.
Freezing Point Measuring Device
The Freezing Point device is used to measure the freezing point of petroleum materials in negative temperature, which is in accordance with the ASTM D1177 standard.
Hot Plate
Hot plate is one of the widely used laboratory equipments used in laboratory environments. which is generally used as a thermal plate to mix and dissolve solutions and heat samples in laboratory containers.
Application of Hot Plate
Laboratory Heater
Heaters are another type of laboratory equipment that, when combined with a magnetic stirrer, perform similarly to a magnetic hot plate. Essentially, this laboratory device, considered a type of magnetic hot plate, is used for heating and dissolving solutions. Moreover, this device is currently available in various types, including stirrer laboratory heaters, industrial heaters, laboratory heaters with special coatings.
It is worth mentioning that when using a laboratory heater, the device’s temperature should be set between 100 to 750 degrees Celsius, using power with a voltage of 120 to 480 volts.
Laboratory Oven
One of the laboratory equipments are laboratory ovens, which are also called laboratory ovens. This tool is used in different situations.
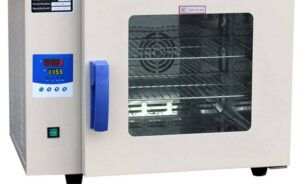
This device is used for sterilizing or drying glass or metal devices in the laboratory. The working method of this device is that metal items that have been cleaned in advance. We put it in the machine at a temperature of 180 degrees Celsius for 2 hours. And with the help of the heat of this tool, they are sterilized and dried. The method of sterilizing these devices is to increase the temperature in the oven. The moisture present in these glassware evaporates and as a result stops the biological activity and as a result the instruments are sterile.
Spray Dryer
Gas Chromatography
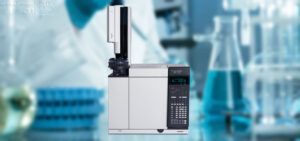
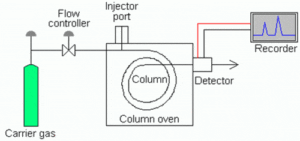
Viscometer
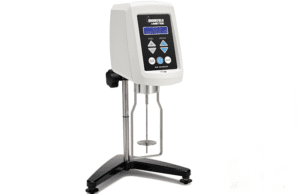
Bomb Calorimeter
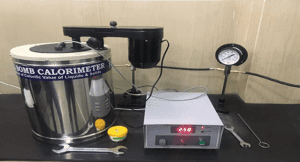
Sulfur Analyzer
One of the most important quality control factors in petroleum products is the amount of sulfur in them. Sulfur is known as a pollutant in petroleum products. And it can produce polluting gases such as SO2 when burning. Therefore, reducing and controlling the amount of sulfur in petroleum products is of particular importance. Sulfur analyzers are used to accurately determine the amount of sulfur in crude oil, refined products and natural gas. These devices measure the amount of sulfur using various techniques such as X-ray fluorescence spectrometry.
Design and Manufacturing of Equipment
1. Materials and Material Selection
2. Ergonomic Design
3. Control and Monitoring Systems
4. Safety Standard
5. Scalability
6. Environmental Considerations
7. Modern Technologies
8. Quality Monitoring and Control
9. Maintenance and Repairs
10. Continuous Development
Anil Pars Industrial Process Company
Anil Pars Industry Process Company proudly operates in the field of designing, engineering and manufacturing laboratory and semi-industrial equipment. This company provides innovative and efficient solutions in the field of petrochemical and chemical industries by using a team of experienced engineers and specialists with world-class technical knowledge.
Our goal is to improve the quality and efficiency of laboratory and semi-industrial equipment so that customers can achieve their research and production goals in the best possible way. By conducting comprehensive studies and analyzing the needs of customers, we design and produce equipment suitable for the specific processes of each industry. Our equipment is at the highest standards in terms of performance, safety and durability. Using the best raw materials and advanced technologies, we offer products that not only have high performance, but also ensure reliability and sustainability.
Conclusion
The design and manufacturing of laboratory and semi-industrial equipment is considered one of the fundamental pillars of the petrochemical industry. This equipment is used to facilitate research and development processes, scientific experiments, and the production of chemical materials. Designing this equipment requires in-depth knowledge in the fields of chemistry, engineering, and safety standards.
The selection of appropriate and durable raw materials that can withstand various conditions, as well as conducting precise tests for validating performance and safety, are other critical stages in this process. With technological advancements, laboratory and semi-industrial equipment is moving towards automation and the use of innovative technologies, which enhances precision and efficiency. Ultimately, the design and manufacturing of this equipment not only contribute to improving quality and productivity in the petrochemical industry but also play a vital role in sustainable development and environmental protection.