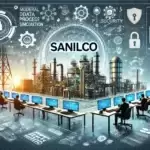
SANILCO Industrial Process Company is a Leader in Industrial Simulation with a Commitment to Privacy
آذر ۱۹, ۱۴۰۳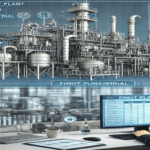
Exploitation of laboratory pilots in industry
دی ۶, ۱۴۰۳Introduction
Industrial laboratory pilots are designed as small-scale tools to simulate and test industrial processes before implementation on a large scale. These units help industries and companies to evaluate the performance of their production processes and optimize them. In addition, pilots are vital tools for reducing financial and operational risks and enabling the development of innovative products and technologies.
The use of laboratory pilots makes it possible to accurately and controllably evaluate the performance of raw materials, adjust operational parameters, and test chemical reactions and mechanical processes. These systems are also used as educational and research tools in universities and research centers to train students and carry out scientific projects.
Given the importance of pilots in reducing production costs and risks, their design must be carried out carefully to ensure reliable and scalable results. In this article, we will examine the importance of pilots, their key features, design and construction stages, and their applications in various industries.
Key Features of Effective Pilot Plants
Effective pilot plants possess a set of characteristics that make them ideal for simulating complex processes and conducting precise experiments. Some of these key features include:
-
High Flexibility
Pilot plants should be easily adjustable to accommodate variations in operational parameters such as temperature, pressure, and flow rate. This flexibility allows for testing a wide range of scenarios.
-
Advanced Control Systems:
Accurate control systems and intelligent measurement instruments ensure continuous monitoring of the pilot plant’s performance. These systems enable data logging and analysis.
-
Scalability
The design of a pilot plant should facilitate easy scaling up to larger production capacities. This is crucial for testing processes before full-scale industrial production.
-
Enhanced Safety
Safety is paramount in the design and construction of pilot plants. The use of heat and pressure-resistant materials and safety systems to prevent leaks or explosions is essential.
-
Modular Design
Modular pilot plants allow for the addition or removal of different components, offering greater flexibility for process modifications and optimization.
-
High-Quality Materials
To ensure durability and optimal performance, high-quality materials such as stainless steel or robust polymers should be used in the construction of pilot plants.
Applications of Pilot Plants in Various Industries
Pilot plants play a crucial role in research, development, and optimization of industrial processes across various industries. These scaled-down versions of production facilities serve as experimental platforms for testing new materials, processes, and products. Key applications include:
-
Product Development: Pilot plants help in developing new products by allowing for small-scale production and testing.
-
Catalyst Evaluation: Catalysts, essential for many chemical reactions, can be evaluated for their performance and efficiency in pilot plants.
-
Process Optimization: Pilot plants enable the fine-tuning of process parameters to improve product quality and reduce costs.
-
Reaction Testing: Chemical reactions can be studied under controlled conditions to understand their kinetics and thermodynamics.
Specific Applications in Industries:
- Chemical Industry: Pilot plants are used for developing new chemicals, optimizing reaction conditions, and scaling up processes.
- Pharmaceutical Industry: Pilot plants are essential for formulation development, scale-up, and quality control in the pharmaceutical industry.
- Food Industry: Pilot plants help in developing new food products, optimizing processing conditions, and ensuring product safety.
- Oil and Gas Industry: Pilot plants are used for testing new extraction and refining processes, as well as for evaluating the performance of catalysts and adsorbents.
- Environmental Industry: Pilot plants are used for developing new technologies for wastewater treatment, air pollution control, and waste management.
Benefits of Pilot Plants:
- Reduced Risk: Pilot plants allow for risk mitigation by identifying potential problems and optimizing processes before full-scale production.
- Process Optimization: Pilot plants can be used to identify bottlenecks, improve efficiency, and reduce costs.
- Material Testing: The properties and compatibility of raw materials can be evaluated in pilot plants.
- Product Development: Pilot plants accelerate the development of new products by enabling rapid prototyping and testing.
- Training and Research: Pilot plants provide valuable hands-on experience for engineers and researchers.
Design Considerations for Pilot Plants:
The design of a pilot plant must balance flexibility, accuracy, and cost. Key considerations include:
- Flexibility: The ability to easily modify the pilot plant to test different processes and products.
- Accuracy: The ability to accurately measure and control process variables.
- Cost: The need to minimize capital and operating costs.
- Safety: Ensuring the safe operation of the pilot plant.
- Scalability: The ability to scale up the process to a larger production scale.
Design and Construction of Industrial Pilot Plants:
The design and construction of an industrial pilot plant involve a systematic approach that includes:
- Process Definition: Clearly defining the process to be studied.
- Equipment Selection: Selecting appropriate equipment based on process requirements.
- Layout Design: Developing a layout that maximizes efficiency and safety.
- Instrumentation and Control: Installing appropriate instrumentation and control systems.
- Safety Systems: Incorporating safety features to protect personnel and equipment.
- Commissioning: Testing and validating the pilot plant before operation.
Defining the Objectives and Requirements of a Pilot Plant
The initial step in designing a laboratory pilot plant is to define the project’s objectives and requirements. In this phase, the research and development team must precisely outline the experimental goals. These objectives might encompass:
- Testing new production processes: Experimenting with novel technologies and production processes destined for large-scale industrial production.
- Optimizing existing processes: Fine-tuning process parameters to enhance production efficiency.
- Evaluating product quality: Assessing product quality on a small scale and identifying necessary modifications to align with industry standards.
Requirements should be meticulously specified to ensure the appropriate allocation of equipment, human resources, and time for the project. These requirements might include factors such as temperature, pressure, material type, environmental conditions, and more.
Designing the Pilot Process
In this stage, engineers and process specialists must create a detailed design for the laboratory pilot plant. The pilot design should encompass all system components, including equipment, machinery, control systems, and automation processes.
Key factors in pilot process design:
- Selecting suitable equipment: Choosing laboratory equipment like tanks, pumps, heating and cooling systems, and measurement devices is crucial.
- Control and monitoring systems: Designing control and monitoring systems to measure and regulate process parameters (e.g., temperature, pressure, flow, pH).
- Process integration: Ensuring all production stages operate seamlessly and harmoniously.
Selecting Raw Materials
The raw materials used in the laboratory pilot plant must adhere to industrial quality and technical specifications. Selecting appropriate raw materials for testing is essential to ensure that the results obtained in the laboratory can be scaled up to industrial production.
In this phase, it is crucial to examine the chemical, physical, and engineering properties of raw materials and their impact on the pilot process. In particular, the material composition should not interfere with the experimental process and should avoid issues like precipitation, corrosion, or unwanted reactions.
Designing Safety and Environmental Systems
In pilot plant design, safety systems are paramount. Pilot plants must be designed to mitigate potential hazards such as chemical spills, explosions, burns, or environmental contamination.
Safety system components:
- Fire detection and suppression systems: Advanced systems for detecting and extinguishing fires.
- Ventilation systems: Designing adequate ventilation to prevent the accumulation of hazardous gases.
- Personal protective equipment: Such as gloves, safety goggles, and specialized clothing.
Equipment Construction and Installation
Following the complete design of the pilot process, equipment construction and installation can commence. In this phase, all laboratory equipment is constructed and installed in accordance with the initial design. This stage involves:
- Constructing physical components: Building tanks, pipes, pumps, heating and cooling systems, and other mechanical equipment.
- Installing control and measurement systems: Installing sensors, transmitters, and monitoring and control systems.
In this phase, the technical team must ensure that all equipment is installed to safety and performance standards and that there are no defects in equipment operation.
Testing and Validation
After constructing and installing the pilot plant, initial tests must be conducted to assess system performance. These tests include:
- Functional tests: Evaluating the operation of equipment and processes under real-world operating conditions.
- Safety tests: Assessing and testing safety systems to ensure a safe environment.
- Quality tests: Examining the quality of the final product and evaluating its physical and chemical properties.
In this phase, test results are collected and analyzed to identify any issues or flaws in the process and address them promptly.
Process Optimization and Modification
Finally, after conducting tests and validations, process optimization may be necessary. This optimization can involve changes in temperature, pressure, raw material composition, or the use of new equipment.
This stage can be repeated multiple times to achieve the desired outcome. Since pilots are typically conducted on a smaller scale than industrial production, leveraging this opportunity to make changes and improvements before mass production is crucial.
Documentation and Scale-Up
After process optimization, the pilot plant results must be thoroughly documented and prepared for industrial-scale transfer. This documentation includes process details, operating instructions, technical designs, and test reports.
Differences Between Laboratory pilots, Industrial Unit and Laboratory Unit
Laboratory pilots, industrial unit, and laboratory unit are all research and production environments used for testing and developing new processes and products. However, each has its own specific features and purposes. The following explains the differences among these three types of environments:
1. Laboratory Pilot
A laboratory pilot refers to an intermediate scale of experiments, typically smaller than industrial production but larger than laboratory tests. It is specifically designed to simulate industrial processes under controlled conditions for evaluating and testing new ideas, processes, and innovative techniques before implementing them on an industrial scale.
Features:
- Smaller Scale: Laboratory pilots is smaller in scale compared to an industrial unit but larger than laboratory experiments. This scale allows researchers to test industrial processes in conditions closer to reality.
- Testing and Optimization Purpose: It is primarily used to simulate industrial processes on a smaller scale, examine material properties, and assess the efficiency of devices and processes.
- Limited Duration: Laboratory pilots are usually set up temporarily for a specific test or experiment and are not intended for long-term use.
- Lower Cost: The smaller scale reduces costs, enabling researchers to perform initial tests without incurring high expenses for full-scale production.
Example:
A chemical plant may establish a laboratory pilot to test a new chemical reaction, simulating its yield and potential problems before implementing it on a larger scale.
2. Industrial Unit
An industrial unit refers to a large factory or facility that conducts production processes on a large scale with high efficiency. These units are typically designed for mass production, and everything—from size and cost to complexity—operates at an industrial level.
Features:
- Large Scale: Industrial units are mainly designed for mass production and operate on a very large scale, carrying out production processes continuously.
- Mass Production: The primary goal of these units is to produce large quantities of products at lower costs.
- Stability: Processes used in industrial units are usually fixed and standardized, designed for stable and high-quality production.
- High Costs: Setting up and maintaining an industrial unit typically requires significant investments due to its large scale and complex equipment.
Example:
An automobile manufacturing plant that produces thousands of cars per day is an example of an industrial unit where processes are carried out continuously on a large scale.
3. Laboratory Unit
A laboratory unit is a research environment primarily designed for conducting experiments and scientific investigations. These environments are commonly used for material analysis, examining physical and chemical properties, and performing laboratory tests.
Features:
- Small Scale: A laboratory unit operates on a much smaller scale compared to a laboratory pilot and industrial unit. These environments are typically designed for precise and controlled experiments.
- Focus on Research and Development: Laboratory units are specifically designed for scientific and experimental research. The main goal is to test and evaluate the properties of materials, processes, and products.
- Precise Equipment: Laboratory units usually require advanced and precise equipment for measurement and data analysis.
- Time-Consuming: Experiments conducted in laboratory units often require more time for analysis and evaluation.
Example:
A chemical laboratory where researchers study the chemical properties of a new material is an example of a laboratory unit designed for the detailed analysis of a substance.
Key Differences
Scale and Purpose:
- Laboratory pilots: Operates at a medium scale, aiming to simulate processes on a smaller scale.
- Industrial Unit: Operates at a very large scale, designed for mass production.
- Laboratory Unit: Operates at a much smaller scale, focusing on scientific research and precise experiments.
Focus on Production or Research:
- Industrial Unit: Focuses on high-efficiency production.
- Laboratory pilots: Focuses on testing and optimizing new processes.
- Laboratory Unit: Designed for scientific research and detailed analysis.
Costs:
- Industrial Unit: Requires high costs due to large scale and advanced equipment.
- Laboratory pilots: Keeps costs lower compared to industrial units due to its smaller scale.
- Laboratory Unit: Often involves high costs for precise equipment and in-depth analysis.
Pilot Laboratory Design and Services by SANILCO
SANILCO, as a leader in the design and construction of Laboratory pilots, offers specialized services to assist companies and researchers across various industrial and scientific fields. These services are particularly valuable for research and development processes, testing, and optimization of new products and processes.
SANILCO provides customized pilot designs tailored to the specific needs of each project, along with technical and engineering consultations, construction and installation of pilots, testing and optimization, and post-launch support. The design process includes selecting suitable equipment, advanced control systems, and high-quality materials to conduct precise experiments.
SANILCO’s engineering team provides technical consultations regarding the selection of the most appropriate production and testing processes, laboratory system design, and troubleshooting during experiments. After the design phase, SANILCO handles the construction and installation of pilots at the customer’s site and offers support and maintenance services to ensure the continuous and proper functioning of the pilot laboratories.
These services help companies and researchers test and optimize their new processes before full-scale industrial implementation.