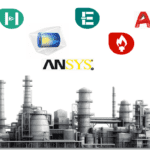
Process Design Simulation Software
مهر ۲۶, ۱۴۰۳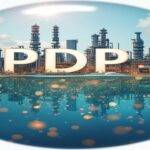
Providing PDP in Petrochemical and Refinery Units by APIPCO
مهر ۲۶, ۱۴۰۳Introduction
Bioethanol production has been studied in the last two decades due to the need to find alternative renewable fuels. However, the production of ethanol from food raw materials has created debates about its production due to direct competition with food. Currently, research is focused on lignocellulosic biomass for the following reasons:
High availability
Relatively low cost
Its indirect food uses
Several lignocellulosic materials have been experimentally evaluated in ethanol production, including:
Almond skin, corn kernels, corn fiber, corn stalks, pine pulp, chopped pine, rice straw, sugar cane. bagasse, willow, spruce, and…
Bioethanol Production Steps
The bioethanol production process consists of five stages:
Pretreatment (first hydrolysis)
Cellulose hydrolysis (second hydrolysis)
Concentration and detoxification
Fermentation
Separation
Various Pretreatment Technologies
Various pretreatment technologies have been developed with the aim of disrupting the lignocellulosic complex, including mechanical, thermal, steam explosion, hot liquid water. (LHW), acidic, alkaline, oxidative, combined thermal and acidic, combined thermal and alkaline, ammonia and carbon dioxide pretreatment (AFEX). The most widely studied method among the mentioned ones is pretreatment with dilute acid (DA) and with steam explosion.
Also the US Department of Energy National Renewable Energy Laboratory (NREL), which is currently developing technology to produce ethanol from biomass. has preferred DA pretreatment to design its process alternatives.
One of the most promising methods is pretreatment with liquid hot water (LHW) or thermohydrolysis. Laser et al pointed out that under optimal conditions, this method with dilute acid pretreatment but without adding acids. or produce comparable hydrolysis neutralization wastes. In addition, this technology also shows high recovery rates of pentoses and little or no inhibitor production.
Description of Bioethanol Production Process
The first unit in Figure 1 (simulation of ethanol production) is a crusher used for size reduction. The final diameter of the expected particles in this unit is 1 mm. After grinding, the raw materials are subjected to acid hydrolysis at a temperature of 170 degrees Celsius for 10 minutes.
Or they are pre-treated with hot liquid water at 220 degrees Celsius for 10 minutes. which enables the conversion of hemicellulose to pentose, which is mainly xylose. Furfural and HMF were considered as the only byproducts of this operation. Because the fermentability of hydrolyzates has an inverse relationship with the concentration of these compounds.
After pre-treatment, the solid part (cellulose and lignin) is separated from the hydrolysis and sent to the second hydrolysis. where cellulose conversion is done at 200°C for 3 minutes. And in the detoxification stages, the purpose of which is to prepare the substrate for fermentation.
The effect of inclusion or exclusion of sugar concentration on ethanol yield and energy consumption was analyzed. At this stage, the liquid part is also treated with calcium hydroxide at 60°C for 30 minutes to reduce the concentration of furfural and HMF, which are more inhibitory compounds for fermentation. The detoxification effluent is later neutralized with sulfuric acid.
The main stage of the whole ethanol production process is fermentation. that the flow of sugars from the previous steps are converted into ethanol by the recombinant bacteria ZM4 (pZB5) at a temperature of 33 degrees for 30 hours. Finally, the ethanol produced by continuous distillation is separated and used in molecular sieve columns to dehydrate ethanol.
Process Configuration
The ethanol production process configuration presented in this work is only applicable to Z. mobiliz ZM4 (pZB5). Any variation from the case used indicates a reorganization of the design and fermentation conditions. Using a different fermentation microorganism also requires a new model.
And perhaps simultaneous adsorption of hexoses and pentoses is not possible. The changing effect of the microorganism depends on the ability to grow on glucose or xylose as a single carbon source. In this sense, if only one sugar is absorbed. An additional microorganism and a fermentation unit will be required to fully utilize the sugars.
The Main Stage of The Process: Fermentation
For the fermentation of sugars, the mathematical model developed by Leksawasdi et al. Two layers (xylose and glucose) were used for fermentation. The authors suggested using this model at 33°C for 30 hours.
They obtained experimental parameters of a kinetic model of fermentation. in which the recombinant bacterium Zymomonas mobiliz ZM4 (pZB5) is able to absorb glucose and xylose simultaneously. Models for operating units such as mills, filters, heat exchangers and distillation columns are not described in detail. Because these are included and well explained in Aspen Plus.
Process Simulation
The scheme of the simulated bioethanol process is shown in Figure 1.
Figure 1. Flow chart of fuel ethanol production from rice husk using LHW or DA pretreatment
1. Stone crusher, 2. First-stage hydrolysis, 3. Filter to separate unhydrolyzed fibers, 4. Second-stage hydrolysis, 5. Filter to separate lignin, 6. Evaporator for concentration of sugars, 7. Cooler, 8. Detoxification reactor, 9. Neutralization reactor, 10. Filter for gypsum separation, 11. Fermentation, 12. Concentration column, 13. Rectification column, 14. Molecular sieves for ethanol dehydration, 15. Product tank.
LHW and DA pretreatments present the same configuration with the only difference in the first hydrolysis conditions.
Simulation Method
Simulation of technological configurations (ethanol production from rice husk using DA and LHW). It was done using Aspen Plus (Aspen Technology Inc., USA). The main input data used for process simulation are shown in Table 1.
Simulations were performed considering a raw material requirement of 240 tons per day, for a plant capacity of approximately 100,000 liters of anhydrous ethanol per day. Part of the data of the physical properties of the components needed for the simulation was obtained from Wooley and Putsche. And the Hayden equation of state is used to model the vapor phase.
The initial characteristics of the distillation columns were estimated using the DSTWU shortcut method available in Aspen Plus. With this information and the results of the static analysis, the exact calculation of the distillation columns was carried out using the RadFrac Aspen Plus model. which is based on mass, balance, mass and heat (MESH).
The estimation of energy consumption was based on the thermal energy required by heat exchangers, boilers and related units. DA and LHW were simulated using batch reactors with kinetic expressions. The second hydrolysis was simulated using a batch reactor with kinetic expressions for cellulose hydrolysis.
Detoxification and fermentation of sugars, including user subroutines, were simulated by the Matlab Excel interface to solve the mathematical model. A circulating fluidized bed combustor/turbogenerator (CFBC/TG) system was also analyzed as a cogeneration technology.
Economic Analysis
Economic analysis was performed by the Aspen Icarus Process Evaluator package (Aspen Technology, Inc., USA). This analysis was calculated in dollars for a 10-year period with an annual interest rate of 16.02%, taking into account the straight-line depreciation method and an income tax of 33%.
The price of rice shell was estimated at $5 per ton only considering the transportation cost of this type of material. Cost of lime and sulfuric acid was 0.08 per kg and 0.09 per kg, respectively. Manpower of operator and supervisor was 2.14 per hr and 4.29 per hour respectively. The cost of electricity, potable water, and low pressure steam was $0.038 per kilowatt hour, $1.25 per cubic meter, and $8.18 per ton, respectively. (All prices are in dollars).
Using design information provided by Aspen Plus and user-introduced data for specific conditions, for example project location, the above software estimates the capital costs of process units as well as operating costs among other valuable data.
Simulation Results
The main results of the flow composition obtained from the simulations are shown in Table 2.
Both pretreatments achieved complete hemicellulose conversion. However, with DA significant cellulose conversion of 31.20% was achieved in the pretreatment. DA is added due to its catalytic effect on cellulose hydrolysis.
It showed higher sugar yield (40.61%) than LHW (30.87%). The presence of acid in the reaction medium had a greater effect on cellulose hydrolysis than higher temperature. But despite this presence of acid, glucose and xylose were dehydrated to HMF and furfural, respectively.
Investigating The Influencing Factor on The Performance of Bioethanol
The concentration of sugars affects the performance of ethanol. When the concentration unit is not considered. In fact, the total concentration of sugar is equal to 37 grams per liter. Lower ethanol efficiency was obtained for DA and LHW, 319.26 and 286.33 liters/ton, respectively.
The effect of concentration of sugars in LHW pretreatment was greater by achieving a 15% increase in ethanol yield. yield obtained from simulations was higher than that reported (236 L/t) for sugarcane bagasse ethanol through dilute acid hydrolysis and hexose fermentation.
The higher yield was attributed to additional utilization of pentose for ethanol production by recombinant bacteria. Capacity of the plant to produce ethanol from rice husk, considering the calculation basis of 240 tons of rice husk per day, was about 80,000 liters per day with sugar concentration and 70,000 liters per day without concentration.
The Main Drawback of This Process
An important parameter in ethanol production from lignocelluloses is energy consumption. This has always been one of the main drawbacks of this type of process. Table 3 shows the net energy consumption of the evaluated cases with and without co-generation of energy.
As expected, the highest energy consumption was obtained when the concentration of sugars (glucose- and xylose-rich hydrolysates) was considered. (See Figure 1 of Unit 6). The contribution of energy consumption by stages is shown in Figure 2.
For both pretreatment technologies evaluated, it was found that Pretreatment and concentration of sugars require most of the total energy of ethanol production. Separation in terms of energy was only relevant when the concentration of sugars was not taken into account. When pretreatment technologies are compared. LHW shows higher energy consumption than DA.
The effect of sugar concentration on downstream energy consumption can be seen in Figure 2. When the concentration of sugars was included, the energy consumption of the fermentation and separation steps for DA and LHW decreased by 68 and 54%, respectively. Only DA pretreatment with simultaneous energy production and no sugar concentration had lower energy consumption than ethanol energy value (21.20 MJ/L). that 39 kg allowed the production of 11.3 kW of electricity per liter of ethanol produced, in addition, the heat generated from the system replaced 32% and 30% of the total energy required for DA and LHW pretreatments with sugar concentrate, respectively.
Conclusion
According to this article The energy requirement for pretreatment is a strong criterion in evaluating the ethanol production process from lignocellulosic biomass. Because it shows the main part of energy demand. Simulation done. And the investigations in this work showed that DA and LHW are efficient processes. But if the simultaneous production of energy is not implemented, these pre-treatment methods are not applicable for the industry due to the need for a large amount of energy.
The cost of producing ethanol from rice husks is highly dependent on energy consumption. However, if a co-production system is included. Energy needs are met and production costs are significantly reduced. Furthermore, when the sale of electricity was considered as a co-product, the cost of ethanol production became competitive compared to that obtained for conventional feedstocks.
These results strongly depend on the composition of lignocellulosic materials used. For example, rice husk contains more lignin than sugarcane bagasse, which means that more energy is obtained from the former in the combustion process. Aspen Plus has proven to be a powerful tool capable of modeling and evaluating complex processes such as ethanol.