– شرایط محیطی: شرایط دما، فشار، و نرخ جریان در هر مرحله از فرآیند.
– تابع کنترل: نحوه کنترل و تنظیم پارامترهای فرآیند برای دستیابی به کیفیت مطلوب محصولات نهایی.
– انتخاب مواد: مشخصات مواد مورد نیاز برای ساخت تجهیزات به منظور مقاومت در برابر شرایط عملیاتی، نظیر خوردگی و دما.
– گزارشات آزمایشات مواد: آزمایشهای انجام شده بر روی مواد به منظور اطمینان از کیفیت و انطباق با استانداردها.
8. تجزیه و تحلیل ایمنی و زیستمحیطی:
– تحلیل خطر و ارزیابی ریسک (HAZOP): شناسایی و ارزیابی خطرات و ریسکهای مرتبط با فرآیند، همراه با راهکارهای پیشگری.
– مطالعه اثرات زیستمحیطی: تحلیل تأثیرات بالقوه فرآیند بر محیط زیست و پیشنهادات برای کاهش این تأثیرات.
9. محاسبات مهندسی:
– محاسبات حرارتی و موازنه جرم: انجام محاسبات حرارتی دقیق و موازنه جرم برای هر مرحله از فرآیند.
– شبیهسازی کامپیوتری: استفاده از نرمافزارهای شبیهسازی برای مدلسازی و بهینهسازی فرآیند.
10. برآورد هزینه:
– تحلیل هزینههای اجرایی: ارائه برآورد دقیق هزینهها برای طراحی، ساخت، و بهرهبرداری از تجهیزات و فرآیند.
– برنامههای مالی: چشمانداز هزینهها در طول زمان و تحلیل بازگشت سرمایه (ROI).
11. نحوه تست و راهاندازی:
– برنامه تست و راهاندازی: دستورالعملهای لازم برای آزمایش تجهیزات و سیستمها قبل از راهاندازی.
– تست عملکرد: مشخصات تست عملکرد برای اطمینان از اینکه تجهیزات طبق استانداردهای طراحی عمل میکنند.
12. مستندسازی و نگهداری:
– سندهای نگهداری و تعمیر: ایجاد راهنماها و فرایندهای نگهداری برای تجهیزات.
– مدارک آموزشی: مستندات آموزشی برای کارکنانی که با تجهیزات و فرآیندها کار میکنند به منظور ارتقاء ایمنی و عملکرد بهینه.
در واقع در حالت کلی، بسته طراحی فرایند (PDP: PROCESS DESIGN PACKAGE) به معنای فعالیتهایی است که به منظور ارائه نقشهها و اسناد مربوط به طراحی و ساخت از طرف ارائه دهنده تکنولوژی شامل:
- دادههای اولیه طراحی (Basic design)
- نمودار جریان فرایند (PDP)
- نمودار لوله کشی و ابزار دقیق (P&ID)
- برگه اطلاعات فرایند تجهیزات + لیست تجهیزات
- لیست تجهیزات آزمایشگاهی (Laboratory)
- توضیحات اینترلاک
- چیدمان کارخانه و چیدمان کلی تجهیزات
- معیارهای طراحی ایمنی
- لیست سیالات و کلاس لوله کشی
- الزامات ابزار
در فرآیند توسعه محصول (PDP)، استفاده از نمودارهای مختلف و اطلاعات دقیق در مورد تجهیزات و فرآیندها حائز اهمیت است. این ابزارها به تیمهای طراحی، مهندسی و تولید کمک میکنند تا شفافیت بیشتری در عملکرد و نیازهای پروژه داشته باشند. در ادامه، به چند نوع از این نمودارها و اطلاعات پرداخته میشود:
1. نمودار جریان فرآیند (Process Flow Diagram – PFD)
– تعریف: نمودار جریان فرآیند یک نمای کلی از مراحل مختلف یک فرآیند تولید را نمایش میدهد. این نمودار شامل ورودیها، خروجیها و مراحل تبدیل مواد در یک فرآیند است.
– اجزاء:
– مراحل مختلف فرآیند به صورت نمادهای استاندارد (مانند دایره، مستطیل).
– جریان مواد و انرژی بین مراحل.
– نقاط ورودی و خروجی.
– کاربرد: در مراحل اولیه طراحی، به عنوان ابزاری برای تجزیه و تحلیل روند تولید و شناسایی نقاط بحرانی
نمونه نقشههای PFD
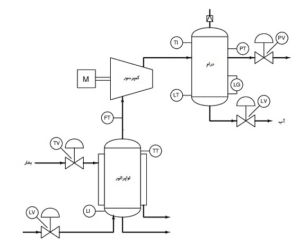
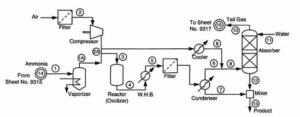
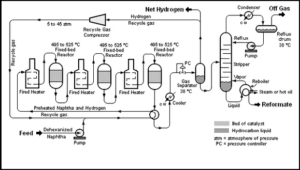
2. نمودار لولهکشی و ابزار دقیق (Piping and Instrumentation Diagram – P&ID)
– تعریف: P&ID به تصویرسازی اجزاء سیستمهای لولهکشی و ابزارهای کنترلی و اندازهگیری پرداخته و به تفکر مهندسی کمک میکند.
– اجزاء:
– پایپها و اتصالات.
– سوپاپها، سنسورها و ابزار دقیق.
– کنترلرها و سایر تجهیزاتی که در فرآیند استفاده میشوند.
– کاربرد: برای شناسایی و نامگذاری تجهیزاتی که نیاز به کنترل و نظارت دارند و همچنین شفافسازی نحوه ارتباط بین آنها
نمونه نقشه های P&ID
نمودار فرآیند و ابزار دقیق ، ادامه منطقی طرح جریان است زیرا در مورد آخر ، کلیه اطلاعات لازم برای ساخت و بهره برداری کارخانه فراهم می شود. هر واحد مهندسی تخصصی با استفاده از یک سمبل شناسی شناخته شده بین المللی (به عنوان مثال سری 5 ISA S) بخش هایی از صلاحیت خود را با درج در این طرح تکمیل یا توسعه می دهد:
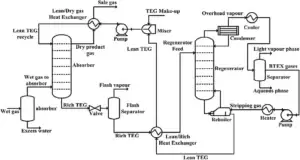
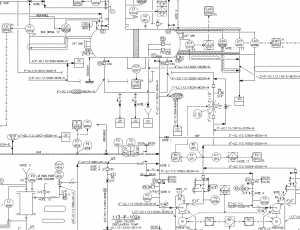
نمونه طراحی نقشههای انجام شده توسط APIPCO
طراحی مدارک، دانش فنی و نقشه های BFD ،PFD ،PID ،UFD واحد خالص سازی اتیلن گلایکل ها
طراحی نقشه های دانش فنی تولید سوربیتان
طراحی 2 بعدی P&ID و PFD در نرم افزار Auto-CAD به صورت کاملا تخصصی
3. اطلاعات فرآیند تجهیزات
– تعریف: شامل مشخصات دقیق هر قطعه از تجهیزات، نظیر ظرفیت، عملکرد، نوع ماده ساخت و دیگر ویژگیهای فنی میشود.
– اجزاء:
– شماره شناسایی و نام تجهیزات.
– مشخصات فنی و عملکرد (مانند دما، فشار، و ظرفیت).
– شرایط نگهداری و تعمیر.
– کاربرد: برای اطمینان از انتخاب و استفاده صحیح از تجهیزات در فرآیند تولید.
4. تجهیزات آزمایشگاهی
– تعریف: فهرستی از تجهیزات و ابزارهایی که در آزمایشها و کنترل کیفیت محصول استفاده میشوند.
– اجزاء:
– تجهیزات اندازهگیری (مانند ترازوها، میکروسکوپها و کروماتوگرافها).
– ابزارهای تست (مانند تجهیزات غیر مخرب و تست مقاومت).
– کاربرد: برای بررسی و ارزیابی کیفیت مواد، فرآیندها و محصولات نهایی.
5. نمودارهای فرآیند کیفی (Quality Process Diagrams)
– این نمودارها به مراحل کنترل کیفیت در فرآیند تولید پرداخته و شامل معیارها و استانداردهای کنترل کیفیت میشوند.
نمونه شبیهسازی صنعتی انجام شده توسط APIPCO
شبیه سازی واحد تولید اتیل استات با ظرفیت 2400 تن در سال (300 کیلوگرم در ساعت)
شبیه سازی واحد 02 (NHT) و ارزیابی امکان سنجی استحصال بنزن از خوراک نفتا
شبیه سازی اسپن پلاس واحد ریفرمینگ پتروشیمی رازی
اهمیت و کاربردهای PDP
– راهنما برای پیمانکاران و مهندسان: PDP به عنوان یک منبع کلیدی اطلاعاتی برای پیمانکاران و مهندسان فراهم میآورد تا کارهای خود را به درستی و بر اساس استانداردهای علمی و صنعتی انجام دهند.
– مدیریت پروژه: کمک به مدیران پروژه در پیشبینی مشکلات و چالشهای احتمالی و برنامهریزی برای آنها.
– گزارشدهی و مستندسازی: تسهیل فرآیند گزارشدهی به مدیران ارشد و سهامداران در مورد پیشرفتها و مشکلات پروژه.
– تضمین کیفیت: فراهم کردن مبنای مستند برای تضمین کیفیت محصولات و تجهیزات، افزایش اطمینان در فرآیند تولید.
– شفافسازی فرآیندها: کمک به تجزیه و تحلیل و درک صحیح از جریان کار و عملکرد تجهیزات.
– شناسایی نقاط بحرانی: کمک در شناسایی نقاطی که نیاز به نظارت و کنترل بیشتری دارند.
– استاندارد سازی: ایجاد یک استاندارد برای ارزیابی و پیمایش فرآیند تولید.
– بهبود تصمیمگیری: فراهم کردن اطلاعات لازم برای تصمیمگیری بهتر در طراحی و توسعه محصول.
استفاده از این ابزارها و اطلاعات در طراحی و توسعه محصولات میتواند به افزایش کیفیت، کاهش هزینهها و بهبود کارایی منجر شود.
نتیجهگیری
پکیج طراحی فرآیند یک ابزار کلیدی در مهندسی و مدیریت پروژههای صنعتی است. که با ارائه اطلاعات دقیق و جامع در مورد تمامی جوانب یک فرآیند، به ایمنی، کیفیت و موفقیت پروژه کمک میکند. این گذشتهنگری و توجه به جزئیات نهتنها به بهبود عملکرد پروژههای صنعتی کمک میکند، بلکه ریسکهای بالقوه را نیز به حداقل میرساند.
4 دیدگاه
PDP چه تاثیری بر کاهش هزینه ها در صنایع پتروشیمی و پالایشگاهی دارد
روز بخیر
PDP با بهینه سازی فرآیندها، کاهش ضایعات و افزایش بهره وری می توانند به طور قابل توجهی هزینه های تولید را کاهش دهند. این طرح همچنین به شناسایی و حذف مراحل غیر ضروری در تولید کمک میکند.
سلام و خسته نباشید
عالی بود. میخواستم بدونم میتونید منابع یا اطلاعات بیشتری در این موضوع رو به اشتراک بزارین؟
درود
سلامت باشین
ممنون از لطفتون. بله خوشحال میشم بتونم کمکتون کنم منابعی رو به زودی به ایمیلتون ارسال میکنم اگر سوال خاصی دارید بفرمایید تا بهتر بتونم کمک کنم.