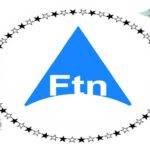
Class GAMBIT-Fluent-Fortran
مهر ۱۱, ۱۴۰۳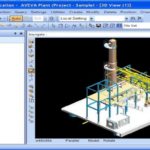
PDMS Project; The Best 3D Modeling Software
مهر ۱۱, ۱۴۰۳Introduction
Propane cooling is a process in which propane is used as a refrigerant in heating, ventilation, air conditioning (HVAC), and industrial processes. This substance is known for its high thermal properties, suitable boiling point, and environmental compatibility, making it a popular choice for cooling systems. These characteristics allow propane to function effectively as a refrigerant in processes such as refrigerators and air conditioning systems. Due to propane’s low boiling point, these systems can operate at lower temperatures, providing greater efficiency.
Important Points about Propane Cooling:
1. Safety: Propane is a flammable gas and must be handled and stored with caution. Systems using propane should be equipped with appropriate safety measures.
2. Efficiency: Propane’s excellent performance at low temperatures makes it a refrigerant used in various industrial and commercial cooling systems.
3. Advantages: Compared to many other refrigerants, propane has a lower environmental impact and can be considered an eco-friendly option.
4. Regulations: The use of propane as a refrigerant may be subject to specific regulations, so local and national conditions must be considered.
Propane Cooling Unit:
This unit, known as the propane cooling unit, comprises one unit per train, totaling four units for two phases (phases 2 and 3). The primary purpose of designing unit 111 is to meet and store the refrigerant material needs for use in unit 105, which is responsible for dew point control and mercaptan removal. This unit includes three different cooling degrees:
– 22°C for use in the Wet Gas Chiller.
– 5°C for use in the Depropaniser Condenser and also in the Butane Cooler.
– 30°C to balance the thermal load in the Cold Box.
The operation in this unit is based on a closed-loop system, where propane used for cooling gas in various parts of unit 105 (vaporized propane) exits the top of each of the three heat exchangers—namely the Butane Cooler, Depropaniser Condenser, and Wet Gas Chiller—then it exits the Flash Drum and enters the Suction Drums in the first, second, and third stages of a three-stage Centrifugal Compressor. The propane is compressed to a pressure of Barg 22 and a temperature of 80°C, and then it is totally condensed and enters the Propane Surge Drum. From there, it operates in a closed loop under gravity for use in unit 105.
This loop is designed to provide 444 m³/hr of liquid propane at 60°C and 21 Barg pressure to unit 105, which corresponds to the refrigerant material needed for processing operations for 500 MMSCFD of gas. Another feature of this unit is the use of a three-stage compressor powered by an electric motor, which includes a Gear Box and a component known as the Inlet Guide Vane (IGV). The main task of the Gear Box is to regulate the speed between the motor and the compressor, while the IGV adjusts the flow at the suction part of the compressor, thereby managing the input gas amount and consequently the compressor load. The IGV, located at the first stage compressor inlet, regulates the incoming flow for this stage.
Conclusion
In conclusion, propane cooling is recognized as an effective and environmentally friendly method in HVAC systems and refrigerators. Its suitable thermal properties and ability to operate at low temperatures make propane an attractive choice. With increasing attention to environmental issues and the search for safer alternatives to traditional refrigerants, propane will continue to be a sustainable and efficient option in the cooling industry.