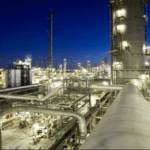
Ethane Purification
مهر ۱۱, ۱۴۰۳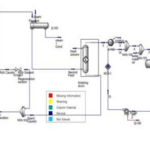
Caustic Recovery
مهر ۱۱, ۱۴۰۳Introduction
The butane purification unit plays a vital role in the processing of hydrocarbons, aiming to remove impurities such as carbon dioxide and water from butane gas. The effective operation of this unit is essential for improving the overall quality of petroleum products and meeting stringent industrial standards. By carefully managing parameters such as temperature and pressure, the butane purification unit significantly contributes to enhancing product yield and optimizing refinery performance.
Butane Purification Unit
This unit is of particular importance because butane, as one of the liquid hydrocarbons, is utilized across various industries, including petrochemicals, fuel production, and other industrial applications.
Main Processes in the Butane Purification Unit:
1. Separation of Impurities: The primary goal of this unit is to eliminate impurities such as water, carbon dioxide, and other unwanted compounds from butane. This is typically achieved using absorption columns and separation tanks.
2. Conversion of Sour Butane to Dry Butane: After purification, sour butane is transformed into dry butane, which possesses higher quality and is more suitable for various applications, including exports and chemical production.
3. Control of Operating Parameters: Temperature, pressure, and other operational factors are meticulously controlled to ensure the production of high-quality products and maximize production efficiency.
Importance of the Butane Purification Unit:
– Improvement of Petroleum Product Quality: This unit aids in producing high-purity butane, which is crucial for specific applications.
– Compliance with Industrial Standards: Proper purification ensures that the produced products can meet global standards.
– Economics and Efficiency: Optimizing processes and reducing production costs lead to increased economic efficiency in the oil and gas industry.
The objective of this unit is to remove mercaptans, water, and CO2 from butane. The feedstock is sour butane from unit 107, and the products are dry butane directed to unit 148, along with a caustic solution containing mercaptans, which is directed towards unit 113. Based on the design, a caustic solution (NaOH) with a concentration of 15% to 20% is used for the purification of sour butane. After absorbing mercaptans, the caustic solution is further purified and recovered in unit 113, then reintroduced into the cycle. The sweetened butane, after drying, is routed for storage to unit 148.
To separate mercaptans from butane, an extraction process is utilized in which butane gas and caustic flow in a countercurrent manner through a tower known as the extractor. This liquid-liquid extraction process occurs at a temperature of 40°C and a pressure of 9 bar. Caustic enters the tower from the top tray (tray 15), while butane enters from the bottom. After separating the mercaptans, butane exits from the top of the tower (post mass transfer and absorption of mercaptans by the caustic solution). It is then washed with water in a settler to isolate any potentially carried-over caustic solution from the extraction process, and is directed toward a sand filter for filtration. Following dewatering and drying, performed in a bed filled with molecular sieves, the filtered gas is directed towards unit 148 for storage.
Conclusion
Considering the objectives and performance of the butane purification unit, it can be concluded that this unit not only plays a key role in enhancing the quality and purity of butane, but it is also an essential component in the hydrocarbon supply chain. The optimal performance of this unit, through suitable operational conditions and the use of modern technologies, results in the production of high-quality dry butane that is usable in petrochemical industries and international markets. Furthermore, continual improvements in purification processes and a better understanding of operational parameters can lead to increased productivity and reduced production costs.