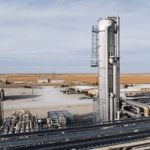
MEG Regeneration Unit
مهر ۵, ۱۴۰۳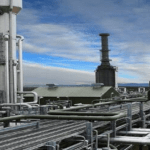
Dehydration and Mercury Removal Unit
مهر ۵, ۱۴۰۳Introduction
This unit, known as the Gas Condensate Stabilization Unit, primarily aims to produce stabilized gas condensates. It separates light hydrocarbon compounds to achieve an RVP of 10 psia in summer and 12 psia in winter. This occurs after the condensates are mixed with C5+ liquids from Unit 105. The unit also separates water and glycol from the gas condensates while stabilizing them. Feed for this unit comes from Unit 100, the Reception Facilities.
Gas Condensate Stabilization Unit
Feed Inlet and Initial Stages
The gas condensates, mixed with water and glycol, enter the unit at around 15–18°C. Initially, the feed passes through two heat exchangers. As a result, the temperature rises to about 50°C by exchanging heat with the stabilized condensates produced within the unit. Additionally, another heat exchanger is available for cases when the inlet temperature is too low.
Separation of Glycol and Water
The gas condensates and glycol, now at 50°C, enter the first vessel called the Preflash Drum. Due to the pressure drop to 27 bar, some gas is produced and is transferred via a pipeline to the Suction Drum of the second stage of the Off-Gas compressor. At this point, the glycol is separated from the gas condensates, and after exiting the bottom of the drum and passing through a filter, it is sent to Unit 102 (MEG Regeneration) for recovery.
Salt Removal Using Desalter
The gas condensates, now at 65°C, are sent to a vessel called the Desalter. In this vessel, fresh water is mixed with the gas condensates, and under the influence of a 12KV electrical current, the salts present in the gas condensates are removed. These salts dissolve in the water, which is then sent to Unit 102 for separation and recovery. The stabilized gas condensates, under pressure of 40 bar and at a temperature of 61°C, exit the Desalter and are sent to the Condensate Stabilizer Column.
Functioning of the Condensate Stabilizer
In the Condensate Stabilizer Column, the gas condensates are boiled using a Reboiler operated by high-pressure steam (HP Steam). The stabilization process involves separating light from heavy hydrocarbons. During this process, some gas (light compounds) is produced and exits the top of the column at a pressure of 9 barg, after which it is sent to the Suction Drum of the first stage of the Off-Gas compressor.
Temperature Control and Heat Exchange
The stabilized condensates exit from the bottom of the column at 177°C. Afterward, they pass through a heat exchanger where the temperature drops to 127°C. They enter another exchanger, the Preheater, where they exchange heat with raw condensates. As a result, the temperature further drops to approximately 113°C. These cooled condensates are then sent to an air cooler for additional cooling.
Transfer of Stabilized Condensates to Storage
Now at 35–40°C, the stabilized condensates flow into a vessel known as the Condensate Degassing Drum. Afterward, two pumps transfer them to Unit 143 for storage and export. These condensates must meet specific criteria, such as having an RVP of 10 psia in summer and 12 psia in winter. If they fail to meet these specifications, they are sent to the Off-Spec section for reprocessing. From there, they are re-injected into Unit 103.
Off-Spec Management and Material Recovery
The gas produced during the stabilization process in Unit 103, from both the top of the column and the Preflash Drum, is pressurized by the Off-Gas compressor. In the first stage, the compressor increases the gas pressure from 9 barg to 27 barg. Then, the gas moves to the Suction Drum of the compressor’s second stage. Here, gas released from the liquids in the Preflash Drum mixes with gas from the first stage. In the second stage, the compressor boosts the gas pressure to around 70 bar. Finally, this gas is injected into the HP Separator inlet in Unit 100.