Introduction
Persian Gulf Star Refinery
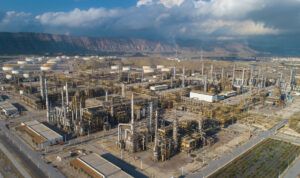
Process Description
Initial Preheating
Pre-fractionator Column
Second Preheating
The pre-fractionated condensates are reheated, raising their temperature to 227 degrees Celsius. This stage includes heat exchangers that utilize various products for heat transfer.
Input Heater of The Main Distillation Column
In this stage, the heated condensates are transferred to the input heater of the main distillation column, where they are mixed with a portion of the products from the bottom of the column to prevent excessive evaporation.
Main Distillation Column
The condensates enter the main distillation column, which contains 47 trays. Here, vapor and liquid come into contact, allowing for the separation of components based on their boiling points. Various products such as heavy naphtha, kerosene, and diesel are produced at this stage. The final products, including heavy naphtha, kerosene, and diesel, are directed to subsequent processing units, while a portion of the final product is transferred to storage tanks.

Simulation of CDU
Definition of Crude Oil Composition
The first step in the simulation process is defining the composition of the crude oil fed into the CDU. In Aspen HYSYS, the crude oil composition is input based on laboratory data or available information from the refinery. This composition includes the volumetric or weight percentages of various hydrocarbons and impurities.
Modeling The Distillation Process
In this stage, the atmospheric distillation column is modeled in Aspen HYSYS. This column typically consists of several trays or packing materials that facilitate the separation of crude oil components. Key parameters such as pressure, temperature, and flow rates of the inlet and outlet streams are configured in this section.
Setting Operational Conditions
Operational conditions, including the inlet temperature of the crude oil, column pressure, and reflux flow rates, are adjusted in the software. These parameters directly influence the quality and quantity of the output products.
Running The Simulation
After configuring the parameters, the simulation is executed. The results include the composition of the output products, temperature and pressure profiles at various points in the column, and the efficiency of the separation process.
Analyzing The Results
The simulation results are analyzed to evaluate the performance of the CDU. This analysis involves assessing separation efficiency, energy consumption, and the quality of the final products.
Optimization of CDU
Optimization of the Crude Distillation Unit (CDU) in Aspen HYSYS is aimed at improving efficiency, reducing energy consumption, and enhancing the quality of the final products. Several optimization strategies include:
Optimization of Operational Conditions
By adjusting parameters such as the inlet temperature of crude oil, column pressure, and reflux flow rates, optimal operational conditions can be achieved. This is typically done using the optimization tools available in Aspen HYSYS.
Heat Exchangers
Optimizing the heat exchanger network can lead to reduced energy consumption and improved process efficiency. In Aspen HYSYS, heat exchangers can be modeled and their performance analyzed.
Enhancement of Distillation Column Design
Modifying the number of trays or the type of packing in the distillation column can increase separation efficiency. Aspen HYSYS allows for the simulation and analysis of these design changes.
Heat Recovery
Implementing heat recovery systems can reclaim wasted energy in the process, thereby reducing overall energy consumption.
Predictive Control
Using predictive control systems in Aspen HYSYS can help improve process stability and reduce operational fluctuations.
Product Specifications
The following product specifications, which are controllable in the Atmospheric Distillation Unit (CDU), must be considered in the design of this unit:
LPG (Liquefied Petroleum Gas)
- Evaporation Temperature for 95% Volumetric: Maximum 2°C
-
C5 and Above (Volumetric): Maximum 1.7% (Note: C5+ in LPG must be adjusted such that the C5 content in the C4 stream from the LPG Splitter Unit does not exceed 1% by volume.)
Naphtha
- Reid Vapor Pressure at 37.8°C: 48.3 to 55.2 kPa
- ASTM D86 98% Distillation: Maximum 183°C
- Temperature Gap between Naphtha and Kerosene: Minimum 3°C
Jet A-1 (Jet Fuel)
- ASTM D86 98% Distillation: Maximum 237°C
- Flash Point: Minimum 38°C
- Specific Gravity at 15°C: 0.775 to 0.830
- Freezing Point: Maximum -47°C
Gas Oil
- Design Case:
- ASTM D86 95% Distillation: Maximum 360°C
- ASTM D86 98% Distillation: Maximum 380°C
- Specific Gravity at 15°C: 0.820 to 0.840
- Flash Point: Minimum 54.5°C
- Alternate Case:
- ASTM D86 95% Distillation: Maximum 340°C
- ASTM D86 98% Distillation: Maximum 360°C
- Specific Gravity at 15°C: 0.820 to 0.840
- Flash Point: Minimum 54.5°C
-
Temperature Gap between Gas Oil and Jet A-1:
In this case, the requirement for the temperature gap between Gas Oil and Jet A-1 is relaxed, and an overlap of up tأo 12°C between these two products is acceptable.
Design of The Condensate Distillation Unit (CDU)
The Condensate Distillation Unit (CDU) is designed to meet all the product specifications outlined in Section 6.0 of this document. The following configuration has been considered for the design of the CDU:
- Prefractionator Column with a Fired Heater Reboiler
- Main Fractionator Column with 3 Pumparounds, Stripping Steam, and Bottom Recycle to the Main Fractionator Feed Heater
- Stabilizer Column with a Steam Reboiler
Design Details
- Prefractionator Column:
- This column is equipped with 28 trays and a fired heater reboiler.
-
The operating pressure at the top of the column is set at 3.0 kg/cm² (absolute), and the overhead condenser is designed as a total condenser.
-
The primary purpose of this column is to separate unstabilized naphtha (with an initial boiling point (IBP) up to 110°C) from the top and the heavier cuts (TBP 110°C +) from the bottom, while minimizing the leakage of LPG components.
Main Fractionator Feed Furnace
The Main Fractionator Feed Furnace is designed to control the vaporization rate within the design limits by recycling a portion of the main fractionator bottom stream. This ensures optimal heat distribution and efficient operation of the distillation process.
Main Fractionator Column
- The Main Fractionator Column is equipped with 47 trays, 3 pumparounds, and stripping steam at the bottom.
-
The operating pressure at the top of the column is maintained at 2.2 kg/cm² (absolute), and the overhead condenser is designed as a total condenser.
-
The duties of the pumparounds and the stripping steam rate are optimized to maximize the production of naphtha and gas oil while minimizing energy consumption.
Kerosene Stripper Column
- The Kerosene Stripper Column consists of 6 trays and a thermosyphon reboiler.
- The reboiler is responsible for achieving the required flash point of the product and maximizing naphtha production.
- The energy required for the reboiler is supplied by the main fractionator bottom recycle stream and the residue product stream.
Gas Oil Stripper Column
- The Gas Oil Stripper Column is designed with 6 trays and utilizes stripping steam.
- The stripping steam rate is adjusted to ensure the required flash point of the product and to maximize naphtha production.
Stabilizer Column
- The Stabilizer Column is equipped with 38 trays and a thermosyphon reboiler.
-
The operating pressure at the top of the column is set at 10.0 kg/cm² (absolute), and the overhead condenser is designed as a total condenser.
-
The column configuration is optimized to control the C5 content in the LPG stream and the C4 content in the stabilized naphtha, ensuring compliance with the required specifications.
Examples of Completed Projects
Simulation and Optimization of STAR Oil Refinery Distillation
Simulation of Crude Oil Distillation Unit (CDU) with Aspen Hysys
Conclusion
The simulation of the CDU unit at the Persian Gulf Star Refinery in Aspen HYSYS is a powerful tool for analyzing and optimizing the performance of this unit. Using this software, operational conditions can be optimized, energy consumption can be reduced, and the quality of products can be improved. The crude oil distillation unit at the Persian Gulf Star Refinery holds significant economic and industrial importance and is recognized as a successful model in the development of oil refining processes in the country. The simulation and optimization of the crude oil distillation unit at the Persian Gulf Star Refinery using Aspen HYSYS enable precise analysis and optimization of the system’s performance, potentially leading to innovative methods for enhancing efficiency and reducing costs. This process allows engineers to make better decisions in the design and management of industrial units.