In today’s world, the petrochemical industry is recognized as one of the fundamental pillars of economic and industrial development in countries. The complex and sensitive processes within this industry require the utilization of advanced technologies and precise simulation tools to optimize performance and enhance productivity. One of the critical tools in this regard is the Aspen Plus process simulator, which is acknowledged as a powerful instrument for the design, analysis, and optimization of chemical and petrochemical processes.
The Demethanizer is one of the key pieces of equipment in petrochemical processes, responsible for the separation of methane from other gases. The optimal performance of this device directly impacts the quality and purity of the products derived from the process. In this context, the dynamic analysis of the Demethanizer is essential for gaining a better understanding of the process behavior under various operating conditions and comprehending the system’s responses to sudden changes.
Demethanizer
The Demethanizer unit at the Imam Khomeini Petrochemical Complex is one of the key facilities in the separation and purification process of hydrocarbon gases. This unit is utilized in the production of light hydrocarbons from natural gas or gases obtained from petroleum processes.
1. Objective and Function:
– The primary objective of the Demethanizer is to separate methane from other light hydrocarbons, such as ethane, propane, and butane. This separation is typically performed to produce ethane as feedstock for petrochemical units and to recover methane as fuel.
2. Operating Process:
– The feed gas enters the Demethanizer unit and is introduced into the distillation column at a specific temperature and pressure. In this column, gases are separated based on their boiling points using distillation principles.
– Lighter gases (such as methane) exit from the top of the column, while heavier hydrocarbons (such as ethane and propane) are collected at the bottom of the column.
3. Key Components:
– Distillation Column: The heart of the Demethanizer unit where the separation takes place.
– Condensers and Reboilers: Used to control temperature and pressure and convert vapor to liquid and vice versa.
– Pumps and Compressors: For transporting and compressing gases.
4. Advantages:
– Optimal recovery and separation of hydrocarbons, leading to increased efficiency and reduced resource waste.
– Production of high-quality products that can be utilized as feedstock for other petrochemical units.
5. Challenges:
– Controlling temperature and pressure in the distillation column to prevent issues such as coking or the formation of deposits.
– The need for regular maintenance and repairs to maintain the efficiency and safety of the unit.
Dynamic Simulation:
To perform dynamic simulation, a steady-state simulation must first be conducted, and then the steady-state file is transferred to the dynamic environment. The steady-state simulation is carried out in
ASPEN PLUS. Initially, the components present in the process are selected, followed by the selection of a thermodynamic model. In this project, the Peng-Robinson equation of state is utilized. The list of selected components is shown in the figure below.
The flowchart of the methanol deactivation unit has been implemented in the ASPEN Plus software and is shown in the figure below.
In order to perform dynamic simulation, equipment related to pressure changes, such as pumps, compressors, and control valves, must be added to the simulation. For this purpose, control valves have been positioned at appropriate locations in the aforementioned simulation. After completing the steady-state simulation, the simulation file is transferred to the ASPEN Dynamics environment. In the ASPEN Dynamics software environment, suitable control loops are implemented, and subsequently, the performance of the control system is evaluated. The final structure is illustrated in the figure.
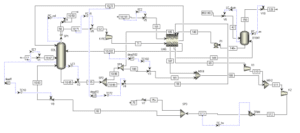
Installed Control Settings
The settings for the installed controls are as follows:
proportional controller with a gain of 2 is considered. For flow rate, a proportional-integral controller with a gain of 0.5 and a time constant of 0.3 minutes is used. For pressure controller, a proportional-integral controller with a gain of 20 and a time constant of 12 minutes is implemented. In the case of temperature, a proportional-integral controller is utilized, and the controller parameters are adjusted using the relay feedback method and the Tyreus-Luyben tuning settings.
Diagram of Changes in Molar Flow Rate
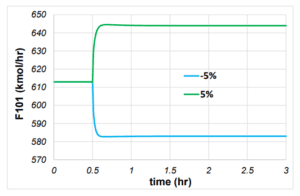
After applying the disturbance, we examine the changes in the important variables of the methanation process in the presence of the disturbance. The pressure control of the column is managed by a flow rate of 10-50. Considering that this flow is the vapor output from the column, it can effectively control the pressure of the column. The dynamic changes in the column pressure are illustrated in the figure.
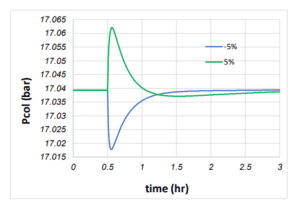
After the disturbance is applied to the process, the temperature controller of tray 16 in the column performs well and maintains the tray temperature at the specified value. The concentration of methane in the flow of 10-50 and the concentration of ethane in the flow of 10-75 are important variables in the methanation process. The concentrations of methane and ethane in the mentioned flows have not changed significantly in the presence of the input disturbance, and the control system has been able to mitigate the input disturbance effectively.
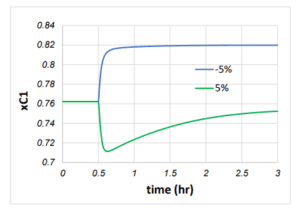
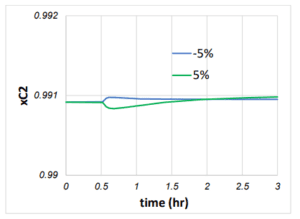
Conclusion
In this project, the dynamic simulation of the methanation process was studied using Aspen Dynamics software. The implemented control structure was examined for a feed flow variation of ±5%. In the presence of input disturbances to the system, the concentrations of methane and ethane in the product streams remain at acceptable levels.
Examples of Projects Completed With Aspen Plus
Stable and Dynamic Simulation of Styrene Unit with Aspen Plus
Static and Dynamic Simulation of 105, 106, 107 ASALOUYE with Aspen Plus
Dynamic Simulation of Heterogeneous Ethanol Dehydration
Dynamic Simulation of Demethanizer of BANDAR IMAM Pet. Co.
This project involves the dynamic analysis of the Demethanizer using
Aspen Plus software for the Imam Khomeini Petrochemical Company (BIPC) aimed at optimizing the methane separation process from other gases. This project has been implemented for the Imam Khomeini Petrochemical Company, and the license for this unit belongs to Linde. The results obtained from this analysis can contribute to improving system performance and increasing efficiency in production processes.