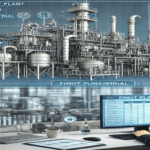
بهره برداری از پایلوت آزمایشگاهی در صنعت
دی ۶, ۱۴۰۳
دپارتمان آب و پساب شرکت مهندسی فرآیند آنیل پارس
دی ۸, ۱۴۰۳مقدمه
در فرآیندهای صنعتی، طراحی و ساخت تجهیزات فرآیندی مختلف برای مرحله تولید اهمیت ویژهای دارد. این تجهیزات، شامل راکتورها، برجها، میکسرها، اسکرابها و سیکلونها، نقش حیاتی در بهینهسازی عملکردها، کاهش هزینهها و افزایش بهرهوری ایفا میکنند. پیش از ورود این تجهیزات به خط تولید، آزمایشهای اولیه در بررسیهای کوچکتر و آزمایشگاهی انجام میشود تا عملکرد و کارکرد آنها به دقت ارزیابی شود.
پروژههای آزمایشگاهی و نیمهصنعتی (پایلوت) مراحل اولیه طراحی و توسعه این تجهیزات فرآیندی را تشکیل میدهند. در این مراحل، مهندسان میتوانند شرایط فرآیند را شبیهسازی کرده و مشکلات بالقوه را شناسایی کنند، قبل از اینکه این تجهیزات فرآیندی به ساختهای بزرگتر منتقل شوند. این فرآیندها به مهندسان این امکان را میدهند که فرآیندهای پیچیده را در محیطی کنترلشده و در مقیاس کوچکتر تست کنند و به این ترتیب، خطرات و چالشهای احتمالی را کاهش دهند.
در این مقاله به بررسی طراحی و عملکرد تجهیزات فرآیندی در صنایع مختلف در مقیاس آزمایشگاهی و نیمه صنعتی میپردازیم
ساخت تجهیزات صنعتی در مقیاس آزمایشگاهی و نیمهصنعتی
فرآیند ساخت تجهیزات فرآیندی صنعتی در مقیاس آزمایشگاهی و نیمهصنعتی شامل چندین مرحله کلیدی است که به مهندسان این امکان را میدهد تا عملکرد تجهیزات فرآیندی را قبل از تولید انبوه ارزیابی کنند. این مراحل به شرح زیر است:
1. طراحی اولیه
در این مرحله، ایدههای اولیه برای تجهیز مورد نظر توسعه مییابند. مهندسان با توجه به نیازهای فرآیند و مشخصات فنی، طراحی مفهومی را ایجاد میکنند. این طراحی شامل انتخاب مواد، ابعاد و ویژگیهای عملکردی است.
2. شبیهسازی
پس از طراحی اولیه، از نرمافزارهای شبیهسازی برای پیشبینی رفتار تجهیز در شرایط مختلف استفاده میشود. این شبیهسازیها به شناسایی نقاط ضعف و قوت طراحی کمک میکند و امکان اصلاحات قبل از ساخت را فراهم میآورد.
3. ساخت نمونه اولیه (مقیاس آزمایشگاهی)
یک نمونه کوچک از تجهیز طراحی شده ساخته میشود. این نمونه به طور دقیق برای آزمایش در شرایط کنترلشده آماده میشود. هدف این مرحله ارزیابی عملکرد واقعی تجهیزات فرآیندی به صورت فیزیکی است.
4. آزمایش و ارزیابی
نمونه اولیه تحت آزمایشهای مختلف قرار میگیرد تا عملکرد و کارایی آن بررسی شود. نتایج این آزمایشها به شناسایی مشکلات و نیاز به اصلاحات کمک میکند.
5. طراحی نهایی
پس از ارزیابی نمونه اولیه، طراحی نهایی با در نظر گرفتن بازخوردهای بهدستآمده از آزمایشها اصلاح میشود. این طراحی باید برای ساخت در مقیاس بزرگتر مناسب باشد.
6. ساخت مقیاس نیمهصنعتی
در مرحله بعد، تجهیز در مقیاس نیمهصنعتی ساخته میشود. این تجهیز به گونهای طراحی میشود که شبیه به نسخه نهایی در مقیاس صنعتی باشد. هدف از این مرحله، آزمایش عملکرد تجهیز در شرایط نزدیک به واقعیت تولید است.
7. آزمایش در شرایط واقعی
تجهیز نیمهصنعتی تحت شرایط عملیاتی واقعی قرار میگیرد. این آزمایشات به شناسایی چالشها و مشکلات احتمالی در تولید انبوه کمک میکند و اطمینان میدهد که تجهیز آماده ورود به بازار است.
در مجموع، ساخت تجهیزات صنعتی در مقیاس آزمایشگاهی و نیمهصنعتی فرآیندی سیستماتیک و دقیق است که به مهندسان این امکان را میدهد تا با اطمینان بیشتری تجهیزات را برای تولید در مقیاس بزرگ آماده کنند. این مراحل به کاهش ریسک و بهینهسازی فرآیند طراحی و تولید کمک میکنند.در ادامه به بررسی چند تجهیز مهم صنعتی میپردازیم و هرکدام از آن ها را در شرایط آزمایشگاهی و نیمه صنعتی بررسی میکنیم .
طراحی و ساخت برج تقطیر در مقیاس آزمایشگاهی و نیمهصنعتی
برجهای تقطیر از جمله تجهیزات کلیدی در فرآیندهای جداسازی مواد شیمیایی هستند که در صنایع مختلف، از جمله نفت، گاز و شیمیایی مورد استفاده قرار میگیرند. طراحی و ساخت این برجها در مقیاس آزمایشگاهی و نیمهصنعتی مراحل خاصی دارد که در ادامه به آنها پرداخته میشود.
1. طراحی اولیه
تحلیل فرآیند: در این مرحله، مهندسان ابتدا نیازهای فرآیند را تحلیل کرده و دادههای مربوط به ترکیب مواد، دما، فشار و نرخ جریان را جمعآوری میکنند.
انتخاب نوع برج: بسته به نوع مواد و نیازهای جداسازی، نوع برج (مانند برجهای تقطیر پیوسته یا ناپیوسته) انتخاب میشود.
2. شبیهسازی
مدلسازی: با استفاده از نرمافزارهای شبیهسازی مانند Aspen Plus یا HYSYS، رفتار برج تقطیر در شرایط مختلف پیشبینی میشود. این شبیهسازیها به مهندسان کمک میکند تا پارامترهای بهینه مانند تعداد طبقات و نوع سطح را تعیین کنند.
تحلیل کارایی: نتایج شبیهسازی برای تحلیل کارایی و بازده تقطیر مورد استفاده قرار میگیرد.
3. ساخت نمونه اولیه (مقیاس آزمایشگاهی)
ساخت برج مقیاس کوچک: یک نمونه اولیه از برج تقطیر در مقیاس آزمایشگاهی ساخته میشود. این برج معمولاً از مواد شفاف یا نیمهشفاف تهیه میشود تا مشاهده فرآیندهای داخلی آسانتر باشد.
اجزای برج: اجزای برج شامل طبقات، سینیها یا پرکنها و سیستمهای تغذیه و جمعآوری محصول است.
4. آزمایش و ارزیابی
آزمایش در شرایط کنترلشده: نمونه اولیه تحت آزمایشهای مختلف قرار میگیرد. دما، فشار و نرخ جریان به دقت کنترل میشود تا عملکرد برج در شرایط مختلف ارزیابی شود.
جمعآوری دادهها: دادههای مربوط به کارایی تقطیر، بازده جداسازی و کیفیت محصولات جمعآوری میشود.
5. طراحی نهایی
اصلاحات بر اساس نتایج: پس از تحلیل دادهها، طراحی نهایی برج با در نظر گرفتن نیازهای بهینهسازی و بازخوردهای بهدستآمده از آزمایشها اصلاح میشود.
6. ساخت مقیاس نیمهصنعتی
ساخت برج در مقیاس بزرگتر: برج تقطیر در مقیاس نیمهصنعتی ساخته میشود. این تجهیز به گونهای طراحی میشود که مشابه نسخه نهایی در مقیاس صنعتی باشد.
توسعه زیرساختها: زیرساختهای لازم برای تامین، کنترل و جمعآوری مواد در این مرحله فراهم میشود.
7. آزمایش در شرایط واقعی
آزمایش عملیاتی: برج نیمهصنعتی تحت شرایط عملیاتی واقعی قرار میگیرد. این آزمایشات برای ارزیابی عملکرد برج در مقیاس بزرگ و شناسایی چالشهای احتمالی انجام میشود.
بازخورد و اصلاحات: نتایج این آزمایشات به مهندسان کمک میکند تا هرگونه مشکلات احتمالی را شناسایی و اصلاح کنند.
طراحی و ساخت برج تقطیر در مقیاس آزمایشگاهی و نیمهصنعتی فرآیندی پیچیده و دقیق است که به مهندسان این امکان را میدهد تا با اطمینان بیشتری برجها را برای تولید در مقیاس بزرگ آماده کنند. این فرآیند شامل مراحل طراحی، شبیهسازی، ساخت، آزمایش و اصلاح است که به بهینهسازی عملکرد و کارایی برجهای تقطیر کمک میکند.
طراحی و ساخت راکتور در مقیاس نیمه صنعتی و آزمایشگاهی
۱. طراحی راکتور
۱.۱. انتخاب نوع راکتور
- راکتور بستر ثابت (Fixed Bed Reactor): برای واکنشهای کاتالیزی که نیاز به تماس زیاد بین فازهای گاز و جامد دارند.
- راکتور بستر سیال (Fluidized Bed Reactor): برای فرآیندهایی که نیاز به تماس مداوم و همگن بین فازهای مختلف دارند.
- راکتور جریان پیوسته (Continuous Stirred Tank Reactor, CSTR): برای واکنشهای مایع-مایع که نیاز به همزدن مداوم دارند.
- راکتور ناپیوسته (Batch Reactor): برای واکنشهایی که نیاز به زمان اقامت طولانیتر و کنترل دقیقتر دارند.
۱.۲. محاسبات طراحی
- زمان اقامت: تعیین زمان اقامت مواد در راکتور برای بهینهسازی میزان تبدیل.
- نرخ جریان مواد: محاسبه نرخ جریان مواد ورودی و خروجی برای کنترل فرآیند.
- انتخاب مواد ساخت: انتخاب موادی که در برابر شرایط عملیاتی مقاوم باشند، مانند دما و فشار بالا و خوردگی.
۱.۳. طراحی اجزا
- بدنه راکتور: طراحی ابعاد و انتخاب مواد ساخت بدنه با توجه به مقاومت در برابر حرارت و فشار.
- سیستم همزن: طراحی سیستم همزن (در صورت نیاز) برای ایجاد همگنی در مخلوط واکنش.
- مبدلهای حرارتی: طراحی مبدلهای حرارتی برای کنترل دمای واکنش.
۲. نرمافزارهای مورد استفاده در طراحی
۲.۱. نرمافزارهای CAD (طراحی به کمک کامپیوتر)
- AutoCAD: برای ترسیم و طراحی نقشههای دو بعدی و سه بعدی تجهیزات.
- SolidWorks: برای مدلسازی سه بعدی و تحلیل المان محدود قطعات و سیستمها.
- ANSYS: برای تحلیل استرس و شبیهسازی جریان گازها و مایعات در تجهیزات.
۲.۲. نرمافزارهای شبیهسازی فرآیند
- Aspen Plus: برای شبیهسازی فرآیندهای شیمیایی و بهینهسازی پارامترهای طراحی.
- COMSOL Multiphysics: برای شبیهسازی چندفیزیکی و تحلیل همزمان جریان، انتقال حرارت و واکنشهای شیمیایی.
- ChemCAD: برای طراحی و بهینهسازی فرآیندهای شیمیایی و تحلیل دینامیکی راکتورها.
۳. ساخت راکتور
۳.۱. انتخاب مواد ساخت
- مواد مقاوم به حرارت و خوردگی: استفاده از موادی مانند فولاد ضد زنگ، آلیاژهای نیکل یا پوششهای محافظتی برای جلوگیری از خوردگی.
- مواد سبک و مستحکم: استفاده از موادی که علاوه بر مقاومت، وزن کمی داشته باشند تا بهراحتی قابل حمل و نصب باشند.
۳.۲. فرآیند ساخت
- برش و جوشکاری: استفاده از تکنیکهای برش دقیق و جوشکاری برای ساخت اجزا.
- مونتاژ اجزا: مونتاژ قطعات ساخته شده به همراه نصب تجهیزات جانبی مانند همزنها، مبدلهای حرارتی و سنسورها.
- آزمون نشتپذیری: انجام آزمونهای نشتپذیری برای اطمینان از عدم نشتی در راکتور.
۴. آزمون و اعتبارسنجی
۴.۱. آزمون عملکردی
- آزمون تبدیل: انجام آزمونهای تبدیل برای ارزیابی کارایی راکتور در واکنشهای شیمیایی.
- آزمون دما و فشار: بررسی اینکه دما و فشار در سراسر راکتور بهطور یکنواخت توزیع میشود.
۴.۲. اعتبارسنجی
- تطابق با استانداردها: اطمینان از اینکه راکتور با استانداردهای زیستمحیطی و ایمنی مطابقت دارد.
- مستندسازی: تهیه مستندات دقیق شامل نقشههای طراحی، مشخصات مواد و دستورالعملهای عملیاتی و نگهداری.
طراحی و ساخت راکتور در مقیاس نیمه صنعتی و آزمایشگاهی نیازمند دقت و دانش فنی بالاست. استفاده از نرمافزارهای طراحی و شبیهسازی میتواند به بهبود کارایی و عملکرد راکتورها کمک کند و اطمینان حاصل شود که تجهیزات تولیدی با استانداردهای زیستمحیطی و ایمنی مطابقت دارند.
طراحی و ساخت میکسر در مقیاس نیمه صنعتی و آزمایشگاهی
میکسرها ابزارهای کلیدی در فرآیندهای صنعتی و آزمایشگاهی هستند که برای همگنسازی و اختلاط مواد مختلف استفاده میشوند. طراحی و ساخت میکسر در مقیاس نیمه صنعتی و آزمایشگاهی به دلیل اهمیت در بهبود کیفیت محصولات و کارایی فرآیندها بسیار مهم است.
۱. طراحی میکسر
۱.۱. انتخاب نوع میکسر
- میکسر پرهای (Blade Mixer): مناسب برای موادی با ویسکوزیته پایین و متوسط.
- میکسر پیچشی (Screw Mixer): برای مواد با ویسکوزیته بالا و مخلوطهای خشک.
- میکسر دورانی (Rotary Mixer): برای مخلوطهای با ذرات بزرگتر و حجیم.
- میکسر همزن مغناطیسی (Magnetic Stirrer): مناسب برای مخلوطهای کوچک در مقیاس آزمایشگاهی.
۱.۲. محاسبات طراحی
- سرعت همزدن: تعیین سرعت مناسب برای همزدن و جلوگیری از تشکیل توربولانس ناخواسته.
- توان مورد نیاز: محاسبه توان مورد نیاز موتور برای به حرکت درآوردن پرهها یا پیچها.
- ویسکوزیته مواد: تعیین ویسکوزیته مواد برای انتخاب نوع و اندازه پرهها.
۱.۳. طراحی اجزا
- پرهها و پیچها: طراحی شکل و اندازه پرهها یا پیچها برای افزایش کارایی اختلاط.
- بدنه میکسر: طراحی ابعاد و مواد ساخت بدنه با توجه به مقاومت در برابر سایش و خوردگی.
- سیستم انتقال نیرو: طراحی سیستم انتقال نیرو برای اطمینان از انتقال صحیح و کارآمد توان به پرهها.
۲. نرمافزارهای مورد استفاده در طراحی
۲.۱. نرمافزارهای CAD (طراحی به کمک کامپیوتر)
- AutoCAD: برای ترسیم و طراحی نقشههای دو بعدی و سه بعدی تجهیزات.
- SolidWorks: برای مدلسازی سه بعدی و تحلیل المان محدود قطعات و سیستمها.
- ANSYS: برای تحلیل استرس و شبیهسازی جریان مایعات در میکسر.
۲.۲. نرمافزارهای شبیهسازی فرآیند
- Aspen Plus: برای شبیهسازی فرآیندهای شیمیایی و بهینهسازی پارامترهای طراحی.
- COMSOL Multiphysics: برای شبیهسازی چندفیزیکی و تحلیل همزمان جریان، انتقال حرارت و واکنشهای شیمیایی.
- FLUENT: برای شبیهسازی دینامیک سیالات محاسباتی (CFD) و تحلیل جریانهای پیچیده در میکسر.
۳. ساخت میکسر
۳.۱. انتخاب مواد ساخت
- مواد مقاوم به سایش و خوردگی: استفاده از موادی مانند فولاد ضد زنگ یا پلیمرهای مقاوم به شیمیایی.
- مواد سبک و مستحکم: انتخاب موادی که علاوه بر مقاومت، وزن کمی داشته باشند تا بهراحتی قابل حمل و نصب باشند.
۳.۲. فرآیند ساخت
- برش و جوشکاری: استفاده از تکنیکهای برش دقیق و جوشکاری برای ساخت اجزا.
- مونتاژ اجزا: مونتاژ قطعات ساخته شده به همراه نصب تجهیزات جانبی مانند موتور و سیستم انتقال نیرو.
- آزمون عملکردی: انجام آزمونهای عملکردی برای اطمینان از کارایی و همگنی اختلاط.
۴. آزمون و اعتبارسنجی
۴.۱. آزمون عملکردی
- آزمون اختلاط: انجام آزمونهای اختلاط برای ارزیابی کارایی میکسر در همگنسازی مواد.
- آزمون استرس: بررسی اینکه میکسر تحت شرایط مختلف بهطور یکنواخت عمل میکند.
۴.۲. اعتبارسنجی
- تطابق با استانداردها: اطمینان از اینکه میکسر با استانداردهای زیستمحیطی و ایمنی مطابقت دارد.
- مستندسازی: تهیه مستندات دقیق شامل نقشههای طراحی، مشخصات مواد و دستورالعملهای عملیاتی و نگهداری.
طراحی و ساخت اسکرابر در مقیاس آزمایشگاهی
اسکرابرها یکی از ابزارهای مهم در کاهش آلودگی هوای ناشی از فرآیندهای صنعتی هستند. آنها قادر به حذف ذرات معلق و گازهای سمی از جریانهای گازی هستند و در صنایع شیمیایی، فلزات و نفت و گاز بسیار مورد استفاده قرار میگیرند.
۱. انتخاب نوع اسکرابر: اسکرابرها به دو دسته اصلی تقسیم میشوند: اسکرابرهای تر و اسکرابرهای خشک. اسکرابرهای تر از مایعات برای جذب آلایندهها استفاده میکنند، در حالی که اسکرابرهای خشک از مواد جامد جاذب برای جذب آلایندهها بهره میبرند.
۲. طراحی اسکرابر
- بررسی نیازها: اولین گام در طراحی اسکرابر، بررسی نیازهای خاص فرآیند است. این نیازها شامل نوع آلایندهها، میزان جریان گاز، و شرایط عملیاتی مانند دما و فشار است.
- انتخاب مواد ساخت: انتخاب مواد مقاوم به خوردگی و سایش برای ساخت بدنه اسکرابر. برای مثال، فولاد ضد زنگ یا پلاستیکهای مقاوم به مواد شیمیایی.
- ابعاد و ساختار: طراحی ابعاد و ساختار اسکرابر براساس محاسبات دقیق مهندسی. این شامل تعیین قطر و ارتفاع اسکرابر و نیز محل نصب نازلها و ورودیها است.
۳. محاسبات و شبیهسازی
- نرخ جذب: محاسبه نرخ جذب آلایندهها با استفاده از معادلات شیمیایی و دینامیکی.
- مدلسازی سهبعدی: ایجاد مدل سهبعدی از اسکرابر با استفاده از نرمافزارهای CAD مانند SolidWorks و AutoCAD.
- شبیهسازی فرآیند: انجام شبیهسازیهای دینامیک سیالات محاسباتی (CFD) با استفاده از نرمافزارهایی مانند ANSYS Fluent برای بهینهسازی جریان و عملکرد اسکرابر.
۴. ساخت و مونتاژ
- برش و جوشکاری: انجام عملیات برش و جوشکاری قطعات با دقت بالا.
- مونتاژ نهایی: مونتاژ قطعات به همراه نصب تجهیزات جانبی مانند پمپها و نازلها.
- آزمون نشتپذیری: انجام آزمونهای نشتپذیری برای اطمینان از عدم وجود نشتی در سیستم.
۵. آزمون و راهاندازی
- آزمون عملکردی: انجام آزمونهای عملکردی برای ارزیابی کارایی اسکرابر در شرایط عملیاتی واقعی.
- تنظیم و کالیبراسیون: تنظیم و کالیبراسیون تجهیزات برای اطمینان از عملکرد بهینه.
طراحی و ساخت اسکرابر در مقیاس نیمه صنعتی و آزمایشگاهی یک فرآیند پیچیده و چند مرحلهای است که نیازمند دانش مهندسی دقیق و استفاده از نرمافزارهای پیشرفته شبیهسازی و طراحی است. با رعایت این مراحل، میتوان اسکرابرهایی با کارایی بالا و عمر مفید طولانی تولید کرد
طراحی و ساخت سیکلون در مقیاس نیمه صنعتی و آزمایشگاهی
سیکلونها یکی از مهمترین تجهیزات در جداسازی ذرات معلق از جریانهای گازی هستند. آنها به دلیل کارایی بالا و ساختار سادهشان در صنایع مختلف مانند صنایع معدنی، شیمیایی و غذایی استفاده میشوند.
۱. اصول عملکرد سیکلونها سیکلونها بر اساس نیروی گریز از مرکز عمل میکنند. وقتی جریان گاز وارد بدنه سیکلون میشود، به صورت مارپیچی به سمت پایین حرکت میکند. این حرکت مارپیچی باعث میشود ذرات معلق به دیوارههای سیکلون برخورد کرده و به سمت پایین سقوط کنند، در حالی که گاز تمیز از بالا خارج میشود.
۲. انتخاب نوع سیکلون انتخاب نوع سیکلون براساس نیازهای فرآیندی و ویژگیهای ذرات معلق انجام میشود. سیکلونها به دو دسته کلی تقسیم میشوند:
- سیکلونهای با کارایی بالا: برای ذرات ریز و سبک.
- سیکلونهای با کارایی متوسط: برای ذرات بزرگتر و سنگینتر.
۳. طراحی سیکلون
- انتخاب ابعاد مناسب: انتخاب قطر و ارتفاع سیکلون براساس میزان جریان گاز و نوع ذرات معلق.
- محاسبات سرعت: تعیین سرعت ورودی و خروجی گاز برای بهینهسازی جداسازی ذرات.
- انتخاب مواد ساخت: استفاده از موادی که در برابر سایش و خوردگی مقاوم باشند، مانند فولاد ضد زنگ یا پلیمرهای مقاوم.
۴. نرمافزارهای مورد استفاده در طراحی
- SolidWorks: برای مدلسازی سهبعدی و بررسی استحکام سازهای.
- ANSYS Fluent: برای شبیهسازی جریان گاز و عملکرد سیکلون با استفاده از دینامیک سیالات محاسباتی (CFD).
- AutoCAD: برای طراحی نقشههای دو بعدی و سه بعدی از سیکلون.
۵. ساخت و مونتاژ سیکلون
- برش و جوشکاری: استفاده از تکنیکهای برش لیزری و جوشکاری دقیق برای ساخت بدنه سیکلون.
- مونتاژ اجزا: مونتاژ قطعات به همراه نصب تجهیزات جانبی مانند نازلهای ورودی و خروجی.
- آزمون نشتپذیری: انجام آزمونهای نشتپذیری برای اطمینان از عدم وجود نشتی در سیکلون.
۶. آزمون و ارزیابی
- آزمون جداسازی: ارزیابی کارایی سیکلون در جداسازی ذرات معلق در شرایط عملیاتی واقعی.
- تنظیم و بهینهسازی: تنظیم پارامترهای عملیاتی برای بهبود عملکرد سیکلون.
سیکلونها ابزارهای کارآمدی برای جداسازی ذرات معلق از جریانهای گازی هستند و طراحی و ساخت آنها نیازمند دقت و دانش فنی بالاست. استفاده از نرمافزارهای طراحی و شبیهسازی به بهبود کارایی و عملکرد سیکلونها کمک میکند و اطمینان میدهد که تجهیزات فرآیندی تولیدی با استانداردهای زیستمحیطی و ایمنی مطابقت دارند
نتیجه گیری
طراحی و ساخت تجهیزات فرآیندی در مقیاس نیمه صنعتی و آزمایشگاهی یک فرآیند پیچیده و چند مرحلهای است که نیازمند دانش عمیق مهندسی و آشنایی با ابزارها و نرمافزارهای مدرن است. در این مقالهها به بررسی طراحی و ساخت اسکرابر، سیکلون، میکسر و راکتور پرداختیم
نرمافزارهای طراحی و شبیهسازی: استفاده از نرمافزارهای CAD مانند AutoCAD و SolidWorks برای مدلسازی سهبعدی و نرمافزارهای شبیهسازی مانند ANSYS Fluent و Aspen Plus و Aspen Hysys برای شبیهسازی دینامیکی و بهینهسازی فرآیندها از اهمیت بالایی برخوردار است.
آزمون و اعتبارسنجی: تمام تجهیزات فرآیندی باید پس از ساخت تحت آزمونهای دقیق عملکردی و نشتپذیری قرار گیرند تا از عملکرد صحیح و تطابق با استانداردهای زیستمحیطی و ایمنی اطمینان حاصل شود.
در نهایت، طراحی و ساخت این تجهیزات نه تنها نیازمند دانش فنی و مهندسی بالاست، بلکه نیازمند توجه دقیق به جزئیات و استفاده از تکنیکها و ابزارهای مدرن است. با رعایت این نکات میتوان تجهیزات فرآیندی کارآمد و مطمئنی را در مقیاس نیمه صنعتی و آزمایشگاهی تولید کرد که نه تنها در تحقیقات و توسعه، بلکه در بهبود فرآیندهای صنعتی نیز مؤثر هستند