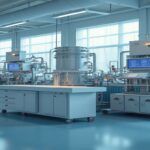
طراحی، خرید و ساخت تجهیزات آزمایشگاهی و نیمه صنعتی
آذر ۷, ۱۴۰۳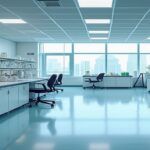
اصول طراحی و ساخت و اجرای سکوبندی آزمایشگاهی و پیاده سازی عملیاتی کلین روم
آذر ۱۳, ۱۴۰۳توضیحات
صنایع فولاد و ذوب آهن به عنوان یکی از صنایع بزرگ و پرمصرف، همواره با چالش کمبود آب و افزایش هزینههای انرژی دست و پنجه نرم میکنند. فرآیندهای تولید فولاد و ذوب آهن نیازمند حجم عظیمی از آب برای خنککاری و شستشو هستند. بازیابی بخار در این صنایع نه تنها به کاهش مصرف آب و انرژی کمک شایانی میکند، بلکه با کاهش هزینههای تولید، سودآوری واحدهای صنعتی را نیز بهبود میبخشد.
نیاز روزافزون به انرژی، به ویژه در صنایع سنگین مانند آهن و فولاد، یکی از چالشهای اصلی در دنیای امروز است. صنعت آهن و فولاد به عنوان یکی از انرژیبرترین صنایع، سهم قابل توجهی از مصرف انرژی را به خود اختصاص میدهد. مصرف بیرویه انرژی علاوه بر افزایش هزینههای تولید، به آلودگی محیط زیست و تخریب منابع طبیعی نیز منجر میشود.
اهمیت بازگردانی بخار هدر رفت در صنایع فولاد و ذوب آهن
بخار بهعنوان یکی از حاملهای انرژی مهم در صنایع مختلف، بهویژه در صنعت فولاد و ذوب آهن، نقش حیاتی ایفا میکند. فرآیندهای حرارتی و تولید فولاد مقادیر زیادی انرژی در قالب بخار تولید میکنند که اگر مدیریت درستی صورت نگیرد، هدر میرود. بازگردانی بخار هدر رفت با استفاده از سیستمهای کندانس و بازیابی انرژی میتواند منجر به کاهش چشمگیر هزینههای انرژی شود.
این موضوع، بهویژه در صنایعی که بهشدت به انرژی وابسته هستند، نهتنها از لحاظ اقتصادی بلکه از دیدگاه زیستمحیطی نیز اهمیت دارد. استفاده بهینه از بخار بازگرداندهشده، باعث کاهش مصرف سوختهای فسیلی و در نتیجه کاهش انتشار گازهای گلخانهای میشود، که میتواند به توسعه پایدار صنعت کمک کند. به عنوان مثال، در سیستمهای جدید هیبریدی، مصرف آب تا 88.3٪ کاهش یافته و این امر نشاندهنده پتانسیل بالای این سیستمها در کاهش هدر رفت منابع ارزشمند است.
ارزش آب و هدر رفت آب و بخار در صنایع
1- ارزش اقتصادی و محیط زیستی آب
آب به عنوان یکی از منابع حیاتی برای بقای بشر و رشد اقتصادی، نقشی کلیدی در توسعه پایدار دارد. در حالی که اکثر صنایع برای فرآیندهای تولیدی خود به آب نیاز دارند، هدر رفت آب در این صنایع میتواند تأثیرات گستردهای بر اقتصاد و محیط زیست داشته باشد.
شکل زیر مصرف معمول آب در یک کارخانه صنعتی را به تصویر میکشد. در صنعت، آب در مجموعهای از فعالیتها استفاده میشود که شامل موارد زیر است: فرآیندهای تولیدی مانند ادغام آب در محصول نهایی، شستشوی مواد خام یا محصولات نهایی؛ فرآیندهای پشتیبانی مانند آمادهسازی حلالها و دوغابها، تمیز کردن تجهیزات و محیط، و حذف یا تامین حرارت؛ مصارف غیرصنعتی مانند تامین نیازهای بهداشتی کارکنان؛ و کاربردهای محیطی مانند آبیاری فضای سبز.
تلفات آب ممکن است بهدلیل تبخیر، نشت، تراکم، و یا تلفات در حین تولید و فرآیندهای جانبی رخ دهد. منابع تامین آب عمدتاً شامل شبکههای آبرسانی شهری، چاههای عمیق، و منابع آب سطحی هستند. با این حال، استفاده مجدد از پسابهای صنعتی چالشهای خاصی را بههمراه دارد، زیرا هر یک از مراحل و فرآیندهای تولید به کیفیت خاصی از آب نیاز دارند.
براساس گزارشها، مصرف آب در صنایع مختلف از جمله صنایع مواد شیمیایی (۶.۸% تا ۸.۷% از هزینهها) و فلزات پایه (۳.۳% تا ۵.۰%) تفاوت دارد. این دادهها نشاندهنده تأثیرات قابل توجه هزینههای آب بر اقتصاد صنایع است.
مصرف بالای آب در صنایع فولادی و کمبود نرخ بازیابی آب از مهمترین چالشها است. به عنوان مثال، میزان مصرف آب در صنایع فولادی هند حدود 3.5 متر مکعب به ازای هر تن فولاد تولید شده است، در حالی که تکنولوژیهای پیشرفته مانند آنچه که در Posco اجرا میشود، این میزان را تا 1.5 متر مکعب کاهش داده است. این مقایسه نشان میدهد که استفاده از تکنولوژیهای بهینهسازی مصرف آب میتواند به کاهش قابل توجه مصرف آب در صنایع منجر شود.
2- اهمیت آب در صنعت و نقش آن در تولید
آب به عنوان یک منبع طبیعی با ارزش، در تمامی فرآیندهای صنعتی نقشی کلیدی ایفا میکند. حدود 15 درصد از مصرف آب شیرین جهان برای اهداف تولید صنعتی است. این میزان در کشورهای صنعتی بیشتر است و در اروپا و آسیای مرکزی 30.7 درصد است. آب در هر مرحله از فرآیند تولید از جمله تولید محصول، شستشو، رقیق کردن، تجهیزات خنک کننده و حمل و نقل کالا استفاده می شود.
صنایع سنگینی مثل فولاد و ذوب آهن برای تولید محصولات خود به مقدار زیادی آب نیاز دارند. این آب در فرآیندهای مختلفی مثل خنککاری تجهیزات استفاده میشود. هدر رفت آب در این صنایع هزینههای زیادی را به همراه دارد و به محیط زیست نیز آسیب میرساند. به عنوان مثال، تولید هر تن فولاد به هزاران لیتر آب نیاز دارد. بنابراین، مدیریت صحیح آب در این صنایع بسیار مهم است. با استفاده از روشهای نوین و فناوریهای جدید میتوان مصرف آب را کاهش داده و از هدر رفت آن جلوگیری کرد. این کار علاوه بر کاهش هزینهها، به حفظ محیط زیست نیز کمک میکند.
3- مقایسه مصرف آب در صنایع مختلف (با تمرکز بر فولاد و ذوب آهن)
مصرف آب در صنایع مختلف به میزان پیچیدگی فرآیندها و نیاز به کنترل دما و حرارت بستگی دارد. به طور کلی، صنایع پتروشیمی، تولید نیرو، و صنایع فولاد از بزرگترین مصرفکنندگان آب هستند. به ویژه، صنایع فولاد و ذوب آهن به دلیل نیاز به سیستمهای خنککننده و تولید بخار، مصرف آب بسیار بالایی دارند. در مقایسه با دیگر صنایع، تولید هر تن فولاد نیاز به حدود 2.66 متر مکعب آب دارد، در حالی که این مقدار برای صنایع تولید مواد شیمیایی یا پالایشگاهها به طور میانگین کمتر است
برای مثال، در صنعت فولاد، آب برای خنکسازی مواد مذاب، تمیزکاری تجهیزات، و تولید بخار استفاده میشود. در این فرآیندها، آب به سرعت داغ میشود و در صورتی که سیستمهای بازگردانی آب وجود نداشته باشد، هدر رفت آب به صورت بخار بسیار بالاست. از طرف دیگر، در صنایعی که مصرف آب کمتر است (مانند تولیدات الکترونیکی یا مواد غذایی)، مدیریت آب کمتر به دلیل حجم پایین مصرف اهمیت پیدا میکند.
صنایع فولاد و مصرف آب
مصرف آب در صنعت فولاد به چندین عامل وابسته است از جمله تکنولوژیهای به کار رفته در تولید و نوع فرآیندها. به عنوان مثال، در روش کوره بلند (Blast Furnace) که یکی از پرکاربردترین روشها در تولید فولاد است، آب به منظور خنکسازی کوره و خنک کردن شمشهای فولادی در جریان تولید مصرف میشود. طبق گزارشها، میزان مصرف آب در این فرآیند بسیار بیشتر از روشهای دیگر است، اما در روشهای جدیدتر نظیر کورههای قوس الکتریکی (Electric Arc Furnace)، مصرف آب به طور چشمگیری کاهش یافته است.
در جدول زیر، مقایسه مصرف آب در صنایع مختلف به همراه صنعت فولاد ارائه شده است:
صنعت | مقدار آب مصرفی به ازای تولید (لیتر/تن) |
فولاد | 15,000 – 50,000 |
سیمان | 2,000 – 5,000 |
مواد غذایی | 1,000 – 2,500 |
نساجی | 8,000 – 12,000 |
به طور خاص، در صنایع فولاد و ذوب آهن، هدر رفت آب به دلیل عدم استفاده بهینه و عدم پیادهسازی فناوریهای نوین، به یک چالش جدی تبدیل شده است. برآوردها نشان میدهد که هدر رفت آب در این صنایع میتواند تا 30 درصد مصرف کل آب را شامل شود.
طبق تخمینهای انجام شده، بیش از 10 درصد از کل آب مصرفی در صنایع فولاد به صورت بخار از دست میرود و این میزان در کارخانههای قدیمی و با تکنولوژیهای کمتر کارآمد ممکن است بیشتر نیز باشد.
4- چالشهای محیط زیستی مصرف بالای آب
مصرف زیاد آب در صنایع، به ویژه صنایع فولاد، علاوه بر افزایش هزینههای عملیاتی، تاثیرات زیستمحیطی مهمی نیز به دنبال دارد. به دلیل استفاده از حجم بالای آب، صنایع فولادی به یکی از اصلیترین عوامل آلایندههای آبی تبدیل شدهاند. در بسیاری از کشورها، تخلیه آب آلوده به رودخانهها و منابع طبیعی به دلیل عدم تصفیه مناسب یکی از مشکلات زیستمحیطی عمده است. آلودگی آب ناشی از فلزات سنگین، مواد شیمیایی، و حرارت بالا در صنایع فولاد میتواند اکوسیستمهای محلی را به شدت تحت تاثیر قرار دهد.
از سوی دیگر، هدر رفت آب در این صنایع نه تنها باعث از دست رفتن منابع طبیعی با ارزش میشود، بلکه با توجه به شرایط کمبود آب در بسیاری از مناطق جهان، به ویژه در کشورهایی مانند ایران که با بحران آب مواجه هستند، مشکلات اجتماعی و اقتصادی جدی نیز به همراه دارد. به همین دلیل، توجه به مدیریت مصرف آب و استفاده از تکنولوژیهای بازگردانی و کندانس بخار اهمیت بیشتری پیدا میکند.
وضعیت آب در ایران
1- منابع آبی ایران
ایران کشوری خشک و نیمهخشک است که با کمبود شدید آب مواجه است. منابع آبی سطحی (رودخانهها، دریاچهها) و زیرزمینی (سفرههای آب زیرزمینی) این کشور به دلیل خشکسالی، بهرهبرداری بیرویه و تغییرات اقلیمی به شدت کاهش یافتهاند.
میزان بارش سالانه در ایران به طور متوسط 250 میلیمتر است که کمتر از یک سوم میانگین جهانی بارشها است. بر این اساس، ایران به عنوان کشوری با منابع آبی محدود شناخته میشود که بخش عمدهای از آب مصرفی آن از منابع زیرزمینی و روانابهای سطحی تأمین میشود.
اما مشکل اصلی این است که توزیع منابع آبی در سطح کشور به صورت یکنواخت نیست. مناطق شمالی کشور به دلیل بارشهای بیشتر دارای منابع آبی فراوانتری هستند، در حالی که مناطق مرکزی و شرقی با بحران شدید کمبود آب مواجهاند.
2- بحران کمبود آب و اهمیت حفظ آن در صنایع
بر اساس گزارشهای سازمان حفاظت محیط زیست ایران، میانگین بارش سالانه در کشور به کمتر از یکسوم میانگین جهانی رسیده و این مسأله موجب شده تا وضعیت منابع آبی به یک بحران ملی تبدیل شود.
در این راستا، صنایع بزرگ مانند فولاد و ذوب آهن که نیاز زیادی به آب برای خنکسازی و تولید بخار دارند، تأثیرات زیادی بر مصرف آب کشور داشتهاند. این صنایع به دلیل مصرف بالای آب، از جمله عوامل اصلی هدر رفت منابع آبی در کشور محسوب میشوند.
طبق آمار، صنایع فولادی ایران به تنهایی به طور میانگین سالانه میلیونها متر مکعب آب مصرف میکنند و این در حالی است که بسیاری از این آبها به دلیل استفاده ناکارآمد هدر میروند. از این رو، بهینهسازی مصرف آب در این صنایع و استفاده از تکنولوژیهای بازگردانی آب به عنوان یکی از راهکارهای اساسی برای کاهش بحران آب در ایران مطرح است.
3- راهکارهای مقابله با بحران آب در ایران
بحران کمبود آب در ایران تنها محدود به تأثیرات اقتصادی و زیستمحیطی نیست، بلکه از نظر اجتماعی نیز پیامدهای جدی به دنبال دارد. در بسیاری از مناطق، کمبود آب منجر به مهاجرت اجباری کشاورزان و صنعتگران به مناطق دیگر شده است. همچنین، اختلافات اجتماعی بر سر توزیع منابع آبی، به ویژه در مناطق کمآب، افزایش یافته است.
یکی از راهکارهای مهم برای مقابله با بحران آب در ایران، سرمایهگذاری در فناوریهای نوین مدیریت آب در صنایع است. استفاده از سیستمهای بازیابی و بازگردانی آب، به ویژه در صنایع فولاد و ذوب آهن که از بزرگترین مصرفکنندگان آب در کشور محسوب میشوند، میتواند به کاهش مصرف آب و حفظ منابع آبی کمک کند.
همچنین، تصفیه و استفاده مجدد از آبهای مصرفی و بهرهبرداری از منابع آب شور و بازیافت آب دریا میتواند به عنوان راهکارهای مؤثر برای کاهش وابستگی به منابع آب شیرین مطرح شوند.
آب کولینگ و خواص آن
آب کولینگ (Cooling Water) به سیستمی اطلاق میشود که در آن از آب به عنوان یک واسطه برای انتقال و جذب گرما استفاده میشود. این روش بهطور گسترده در صنایع مختلف، بهویژه صنایع سنگین مانند فولاد و ذوبآهن، نیروگاهها و پتروشیمیها برای خنکسازی تجهیزات و فرآیندها به کار گرفته میشود. آب کولینگ با گردش مداوم در سیستمهای خنککننده مانند برجهای خنککننده، مبدلهای حرارتی، و کندانسورها، نقش اساسی در حذف گرمای اضافی تولید شده در فرآیندهای صنعتی ایفا میکند.
خواص شیمیایی و فیزیکی آب
آب به دلیل ویژگیهای منحصر به فرد زیر، به عنوان یکی از بهترین مایعات برای خنکسازی در صنایع مختلف استفاده میشود:
- ظرفیت گرمایی بالا: آب میتواند مقدار زیادی گرما را جذب کند بدون اینکه دمای خود را به شدت افزایش دهد.
- رسانایی حرارتی بالا: آب گرما را به سرعت منتقل میکند که به کنترل بهتر دما کمک میکند.
- ویسکوزیته پایین: آب به راحتی در لولهها جریان مییابد و انرژی کمتری برای پمپاژ نیاز دارد.
- خاصیت حلالیت: آب میتواند بسیاری از مواد را در خود حل کند که در برخی موارد مفید و در برخی موارد مشکلساز است.
- پایداری شیمیایی: آب در شرایط صنعتی مختلف پایداری خوبی دارد.
نقش کولینگ در کاهش مصرف انرژی و حفظ تجهیزات
آب کولینگ علاوه بر خواص فیزیکی و شیمیایی خود، تأثیر مستقیم و قابلتوجهی بر کاهش مصرف انرژی و بهینهسازی عملکرد تجهیزات صنعتی دارد. در صنایع بزرگی مانند فولاد و ذوبآهن، که فرآیندهای تولید با دمای بالا و مصرف انرژی سنگین همراه است، مدیریت مؤثر دما یکی از عوامل کلیدی در کاهش مصرف انرژی و افزایش بهرهوری است.
- کاهش مصرف انرژی: استفاده از آب کولینگ به دلیل ظرفیت بالای جذب گرما، باعث کاهش نیاز به استفاده از سایر روشهای خنکسازی پرهزینه میشود. سیستمهای کولینگ آبی در مقایسه با روشهای خنکسازی مبتنی بر هوا یا روغن، توانایی بیشتری در جذب و دفع سریع گرما دارند، که این موضوع به کاهش مصرف انرژی در فرآیندهای خنکسازی کمک میکند. این مسئله در صنایع سنگین مانند فولاد، که نیاز به خنکسازی مداوم تجهیزات دارند، اهمیت ویژهای دارد. به عنوان مثال، کاهش دمای کورههای ذوب با استفاده از آب کولینگ باعث کاهش مصرف سوخت و انرژی مورد نیاز برای تولید حرارت میشود.
- حفظ تجهیزات و کاهش خرابیها: خنکسازی مناسب به افزایش عمر مفید تجهیزات صنعتی و کاهش هزینههای نگهداری کمک میکند. در صنایعی مانند فولاد و ذوبآهن، که تجهیزات تحت فشار حرارتی بسیار بالایی قرار دارند، استفاده از آب کولینگ باعث جلوگیری از آسیبهای حرارتی و خرابیهای مکانیکی میشود.
- بهینهسازی فرآیندهای صنعتی: یکی دیگر از نقشهای مهم آب کولینگ در صنایع، بهینهسازی فرآیندهای تولیدی است. به عنوان مثال، در فرآیند تولید فولاد، کنترل دما از طریق سیستمهای کولینگ باعث بهبود کیفیت محصول نهایی، افزایش راندمان تولید و کاهش مصرف مواد اولیه میشود.
- حفظ منابع آبی و محیط زیست: استفاده از سیستمهای خنکسازی آبی علاوه بر کاهش مصرف انرژی، به حفظ منابع آبی نیز کمک میکند. در سیستمهای کولینگ بسته، آب بهصورت مداوم در حال گردش است و پس از خنکسازی دوباره به چرخه تولید بازمیگردد. این موضوع باعث میشود که مقدار زیادی از آب هدر نرفته و به محیط زیست بازگردد.
قیمت و هزینههای آب کولینگ
1- هزینههای مربوط به تأمین و تصفیه آب کولینگ
هزینههای مرتبط با تأمین و تصفیه آب کولینگ به عنوان یکی از مهمترین عوامل در تعیین هزینههای عملیاتی صنایع به شمار میروند. مکانیزم قیمتگذاری کامل برای آب کولینگ باید شامل هزینههای منابع، هزینههای زیستمحیطی و هزینههای فرصت باشد تا قیمت آب به درستی تعیین شود.
- هزینههای تأمین آب:
این هزینهها به قیمت آب به دست آمده از منابع طبیعی مانند رودخانهها، دریاچهها و چاهها بستگی دارد. هزینه تأمین آب معمولاً با توجه به موقعیت جغرافیایی و نوع منبع آب متغیر است. برای مثال، در مناطقی که آب کمیابتر است، قیمت آب خام میتواند به طور قابل توجهی افزایش یابد.شامل هزینههای مرتبط با پمپاژ و انتقال آب از منبع به محل استفاده است.
- هزینههای تصفیه آب:
تجهیزات تصفیه: برای اطمینان از اینکه آب مورد استفاده در سیستمهای کولینگ عاری از آلودگی و مواد مضر باشد، نیاز به تجهیزات تصفیه وجود دارد. این تجهیزات شامل فیلترها، سیستمهای تبادل یونی و تصفیههای شیمیایی است که هزینههای بالایی دارند. فرآیند تصفیه آب نیاز به انرژی دارد، که این خود به هزینههای عملیاتی اضافه میکند.
مطالعه بازار در مورد هدر رفت آب و بخار در صنایع فولادی
1- بررسی هدر رفت آب و بخار در صنایع فولادی
مطالعات نشان میدهد که هدر رفت آب و بخار در صنایع فولادی بهطور مستقیم بر هزینههای تولید و اثرات زیستمحیطی تاثیر میگذارد. در سیستمهای سنتی خنککاری، مصرف آب بهطور چشمگیری بالاست. هدر رفت بخار در صنایع فولادی یکی از مشکلات رایج است که منجر به افزایش هزینههای تولید و کاهش بهرهوری انرژی میشود. بر اساس آمارهای موجود، حدود 20 تا 30 درصد بخار تولیدشده در برخی صنایع فولادی به دلایل مختلف از جمله نشتی سیستمها، عدم بازیابی بهینه و مشکلات فنی هدر میرود.
برای مثال، در ایران، بحران آب و افزایش هزینههای انرژی، اهمیت بازیابی بخار و آب در صنایع را بیشتر کرده است. این امر بهویژه در صنایعی که به شدت به منابع آب و انرژی وابسته هستند، از جمله صنعت فولاد و ذوب آهن، تاثیر زیادی بر بهرهوری اقتصادی و محیط زیستی دارد.
طبق گزارشهای سازمان جهانی انرژی، صنایع فولاد و ذوب آهن در سالهای اخیر به عنوان یکی از بزرگترین مصرفکنندگان آب در سطح جهانی شناخته میشوند. به طور متوسط، برای تولید هر تن فولاد، بین 1.5 تا 6.0 متر مکعب آب نیاز است. همچنین، در این صنایع، هدر رفت بخار میتواند به بیش از 20% از بخار تولیدی برسد. این رقم به معنای هدر رفت میلیاردها دلار در هزینههای انرژی و منابع آب است.
2- تخمین هزینههای ناشی از هدر رفت بخار در صنایع فولاد و ذوب آهن
تخمین هزینههای ناشی از هدر رفت آب و بخار به شناسایی اثرات اقتصادی و مالی این هدر رفتها کمک میکند. هزینههای ناشی از هدر رفت بخار در این صنایع شامل موارد زیر است:
بخار به عنوان یک منبع انرژی حیاتی در فرایندهای تولید فولاد استفاده میشود. هزینه تامین و تصفیه آب به عوامل متعددی مانند محل، نوع منبع آب، و زیرساختهای مورد نیاز بستگی دارد و میتواند بسیار متغیر باشد.
در ایالات متحده، سیستمهای عمومی آب که از آبهای زیرزمینی استفاده میکنند، به دلیل نیاز به پمپاژ بیشتر، حدود 31٪ هزینههای انرژی بیشتری نسبت به سیستمهایی که از آبهای سطحی استفاده میکنند، دارند. انرژی مورد نیاز برای تصفیه و توزیع آب در سیستمهای شهری معمولاً حدود 80٪ کل هزینهها را شامل میشود.
چالشها و مشکلات هدر رفت آب و بخار در صنایع فولاد و ذوب آهن
1- چالشهای<strong> هدر رفت بخار در صنایع فولاد و ذوب آهن
هدر رفت بخار در صنایع فولاد و ذوب آهن یکی از مشکلات عمدهای است که تأثیرات اقتصادی و زیستمحیطی قابل توجهی به همراه دارد. با توجه به وابستگی شدید این صنایع به بخار بهعنوان منبع انرژی حرارتی و نیروی محرکه، از دست رفتن بخار بهدلیل ناکارآمدی سیستمهای تولید، انتقال و بازگردانی، منجر به افزایش هزینههای تولید و کاهش بهرهوری میشود. چالشهای فنی و اقتصادی از جمله موانع اصلی در پیادهسازی سیستمهای بازگردانی بخار در صنایع فولاد و ذوب آهن هستند.
- پیچیدگیهای فنی و اقتصادی
پیچیدگیهای فنی و اقتصادی در فرآیند بازگردانی بخار شامل چالشهایی نظیر نیاز به تکنولوژیهای پیشرفته، هزینه بالای زیرساختها و تجهیزات، و مشکلات ناشی از نوسانات فشار و دما در سیستمها میشود. سیستمهای لولهکشی فرسوده نیز به دلیل نشتی، مقدار زیادی بخار را هدر میدهند، بهویژه در کارخانههای قدیمی. علاوه بر این، پیچیدگی اقتصادی ناشی از قیمتگذاری آب و تفاوتهای منطقهای و فصلی در هزینهها، بهرهوری این فرآیند را دشوارتر میکند. برای غلبه بر این چالشها، نیاز به برنامهریزی دقیق و سرمایهگذاریهای کلان وجود دارد.
- نیاز به تکنولوژیهای پیشرفته
برای به حداقل رساندن هدر رفت بخار، استفاده از تکنولوژیهای پیشرفته در زمینه کنترل، نظارت و بازگردانی بخار ضروری است. تکنولوژیهای مدرن شامل حسگرهای پیشرفته، سیستمهای مانیتورینگ فشار و دما، و نرمافزارهای مدیریت انرژی میباشند که میتوانند به کاهش هدر رفت بخار و بهینهسازی فرآیندهای تولید کمک کنند.
با این حال، عدم دسترسی به این تکنولوژیها در برخی از کارخانهها، بهویژه در کشورهای در حال توسعه، یک چالش بزرگ است. علاوه بر این، پیادهسازی و نگهداری از این سیستمهای مدرن نیازمند نیروی کار متخصص و آموزشدیده است که بسیاری از کارخانهها فاقد آن هستند.
معرفی شرکت های فولادی با هدر رفت بخار بالا
1- شرکتهای بزرگ فولاد ایران
صنایع فولادی یکی از بزرگترین مصرفکنندگان منابع آب و انرژی در جهان به شمار میروند. در ایران، چندین شرکت فولاد در مقیاس بزرگ فعالیت دارند که نه تنها از نظر تولید محصولات فولادی پیشرو هستند، بلکه با چالشهای جدی در مدیریت منابع به ویژه آب و بخار روبرو هستند. برخی از مهمترین این شرکتها عبارتند از:
-
فولاد مبارکه اصفهان
فولاد مبارکه به عنوان بزرگترین تولیدکننده فولاد در خاورمیانه، ظرفیت تولیدی بالغ بر ۷ میلیون تن در سال دارد. این شرکت طیف گستردهای از محصولات فولادی شامل ورقهای گرم و سرد نورد شده، گالوانیزه و دیگر محصولات فولادی تولید میکند. با این وجود، فرآیند تولید فولاد به ویژه در بخش خنکسازی (Cooling Systems) مصرف آب زیادی دارد. براساس آمارهای موجود، بخشی از این آب به دلیل نبود سیستمهای کارآمد بازیابی بخار به صورت بخار هدر میرود.
-
ذوب آهن اصفهان
این شرکت یکی از بزرگترین تولیدکنندگان شمش فولادی در ایران است که از روش احیای مستقیم (Direct Reduction) برای تولید فولاد استفاده میکند. در این فرآیند، حجم زیادی از بخار تولید شده و اتلاف بخار و آب در سیستمهای خنککننده به شدت بالا است. یکی از چالشهای اصلی فولاد خوزستان، نیاز به بهروزرسانی سیستمهای خنکسازی و بازیابی بخار برای کاهش اتلاف انرژی و منابع است.
بهینه سازی فرآیند های تولید در صنایع نفت، گاز، پتروشیمی، نیروگاهی و فولادی
-
فولاد هرمزگان
فولاد هرمزگان که در جنوب کشور واقع شده، به تولید اسلب فولادی میپردازد. با توجه به نزدیکی به آبهای خلیج فارس، این شرکت از منابع آبی برای فرآیندهای خنکسازی استفاده میکند. با این حال، سیستمهای مدیریت و بازیابی بخار در این شرکت نیز با چالشهای بسیاری مواجه است که باعث افزایش هدر رفت بخار و انرژی میشود.
2- میزان هدر رفت بخار و آب در شرکتهای فولادی ایران
صنایع فولاد به طور کلی در فرآیندهای تولید خود مصرف بالایی از آب و انرژی دارند. بخش زیادی از این مصرف مربوط به خنکسازی سیستمهای تولید و همچنین تولید بخار در فرآیندهای
ذوب و نورد است. در ایران، به دلیل مشکلات زیربنایی و عدم استفاده از تکنولوژیهای مدرن، میزان هدر رفت بخار و آب در بسیاری از صنایع فولادی بالا است. در ادامه به جزئیات هدر رفت بخار و آب در شرکتهای مختلف فولاد در ایران و اهمیت این موضوع پرداخته میشود.
-
فولاد مبارکه اصفهان
فولاد مبارکه یکی از بزرگترین تولیدکنندگان فولاد در ایران و خاورمیانه است که از فرآیند نورد گرم و سرد برای تولید محصولات خود استفاده میکند. در این فرآیندها، بخار زیادی تولید و استفاده میشود، اما بخش زیادی از این بخار به دلیل نقصهای موجود در سیستمهای بازیابی بخار، به محیط تخلیه میشود.
در سیستم نورد گرم، آب برای خنک کردن و شستشوی فلزات داغ استفاده میشود که در نتیجه آن بخار زیادی تولید میشود. سیستمهای قدیمی بازیابی بخار در فولاد مبارکه قابلیت جذب و استفاده مجدد از تمام بخار تولید شده را ندارند و در نتیجه بخار بهصورت مستقیم به اتمسفر تخلیه میشود، که منجر به اتلاف انرژی و افزایش هزینههای تولید میشود.
-
ذوب آهن اصفهان
ذوب آهن اصفهان به عنوان یکی از قدیمیترین کارخانههای فولادی ایران، از سیستم کوره بلند استفاده میکند که مصرف آب و انرژی زیادی دارد. این سیستم به آب زیادی برای خنکسازی و تولید بخار نیاز دارد. به دلیل استفاده از تجهیزات قدیمی و سیستمهای ناکارآمد بازیابی، روزانه میلیونها لیتر آب به صورت بخار هدر میرود. برآورد شده است که این کارخانه به طور متوسط ۲۰ درصد از آب مصرفی خود را از طریق بخار از دست میدهد.
این امر به دلیل عدم وجود سیستمهای مدرن بازیابی بخار است که بهطور مستقیم در هزینههای تولید و نگهداری کارخانه تأثیر میگذارد.
-
فولاد خوزستان و فولاد هرمزگان
این دو شرکت به دلیل موقعیت جغرافیایی خود، یعنی قرار داشتن در مناطق گرم و خشک، نیاز بالایی به سیستمهای خنککننده دارند. فولاد خوزستان و فولاد هرمزگان از روش احیای مستقیم برای تولید فولاد استفاده میکنند که در این فرآیند بخار زیادی تولید میشود. در این شرکتها، یکی از بزرگترین چالشها مصرف بالای آب برای خنکسازی و تولید بخار است.
سیستمهای خنککننده این کارخانهها به دلیل شرایط آب و هوایی گرمتر نسبت به دیگر مناطق، نیاز به آب بیشتری دارند. همچنین، بخشی از این آب به صورت بخار به محیط منتقل میشود و بازیابی نمیشود. نبود زیرساختهای پیشرفته برای بازیابی بخار به این معناست که میلیونها لیتر آب و بخار هر ساله هدر میرود، که به طور مستقیم بر هزینههای تولید و همچنین مصرف انرژی و منابع تأثیر میگذارد.
3- آمار و ارقام هدر رفت آب و بخار در صنایع فولاد ایران
-
بررسی تخصصی میزان هدر رفت آب و بخار
بررسیها نشان میدهد که صنایع فولاد ایران در مقایسه با صنایع پیشرو جهانی، میزان هدر رفت بخار و آب بالایی دارند. در حال حاضر، بسیاری از کارخانههای فولادی ایران به دلیل عدم استفاده از تکنولوژیهای بازیابی بخار مدرن و سیستمهای کندانس بهینه، با اتلاف منابع انرژی مواجه هستند. بر اساس آمارهای موجود، میانگین هدر رفت بخار در صنایع فولادی ایران بهطور میانگین حدود 25 تا 30 درصد است، در حالی که این رقم در برخی کشورهای توسعهیافته به کمتر از 10 درصد کاهش یافته است.
این اختلاف نشاندهنده نیاز فوری به سرمایهگذاری در سیستمهای بازیابی بخار و مدیریت منابع آب در صنایع فولادی ایران است. تولید فولاد، خصوصاً در مراحل نورد، ذوب، و خنکسازی، نیازمند حجم بالایی از آب و بخار است. طبق گزارشات داخلی، در شرکتهای بزرگ فولادی ایران مانند فولاد مبارکه و ذوب آهن اصفهان، به طور میانگین بین 15% تا 20% از کل بخار تولیدی به علت نواقص سیستمی هدر میرود. این هدر رفت به دلیل عوامل مختلفی از جمله:
- عدم استفاده از سیستمهای بازچرخانی (Condensate Recovery Systems)
- نشتیهای تجهیزات بخار
- عدم وجود استانداردهای لازم برای مدیریت بخار در دما و فشارهای بالا
برای مثال، فولاد مبارکه اصفهان، یکی از بزرگترین تولیدکنندگان فولاد در ایران، در خطوط نورد گرم خود به دلیل نبود سیستمهای پیشرفته کندانس، بخشی از بخار تولید شده را مستقیماً به محیط تخلیه میکند. این مسئله باعث افزایش هزینههای تولید و کاهش بهرهوری انرژی میشود. در مقایسه با استانداردهای بینالمللی، این مقدار از هدر رفت بسیار بالا بوده و نیازمند اقدامات فوری است.
شرکتهای موفق در بازگردانی بخار و جلوگیری از هدر رفت آب
1- معرفی شرکتهای ایرانی با تکنولوژیهای پیشرفته
در سالهای اخیر، برخی از بزرگترین شرکتهای فولادسازی ایران برای مقابله با بحران آب و انرژی، اقدامات مؤثری انجام دادهاند. برای مثال:
-
فولاد مبارکه اصفهان
این شرکت با نصب سیستمهای پیشرفته بازیابی بخار مانند HRSG، بخار تولید شده در فرآیندهای صنعتی را مجددا به چرخه تولید باز میگرداند. همچنین، با استفاده از سیستمهای Closed-loop Cooling، نیاز به آب تازه را کاهش داده و از تبخیر بیمورد آب جلوگیری میکند.
-
فولاد خوزستان:
این شرکت با استفاده از سیستمهای خنککننده هوایی (ACC) مصرف آب را به طور چشمگیری کاهش داده است. همچنین، با پیادهسازی سیستمهای Mechanical Vapor Recompression (MVR)، هدر رفت بخار و انرژی را به شدت کاهش داده است.
-
ذوب آهن اصفهان:
این شرکت با نصب سیستمهای Dry Cooling و سیستمهای بازیابی حرارت، مصرف آب و انرژی را به میزان قابل توجهی کاهش داده است.
نتیجه گیری
این پروژه با هدف بررسی امکانسنجی کاهش هدر رفت بخار در صنایع فولاد و ذوب آهن ایران اجرا شده است. در این مطالعه، تحلیلهایی بر روی سیستمهای بخار در این صنایع صورت گرفته و تکنولوژیهای مختلف بازیابی انرژی بررسی شدهاند. پروژه شامل تحلیل دادههای موجود، ارزیابی اثرات اقتصادی و زیستمحیطی، و ارائه راهکارهای بهینهسازی است.
استفاده از واحدهای بازیابی بخار نه تنها یک الزام زیستمحیطی بلکه یک سرمایهگذاری سودآور برای صنایع مختلف است. با توجه به مزایای متعدد اقتصادی و زیستمحیطی VRUها، شرکتهایی که به دنبال بهبود عملکرد و کاهش هزینههای خود هستند، میتوانند با بهرهگیری از خدمات شرکتهایی مانند SANILCO، گام بزرگی در این مسیر بردارند.