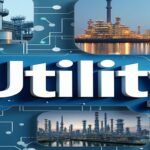
Design, Optimization and Engineering of Facilities and Utility Units
آذر ۵, ۱۴۰۳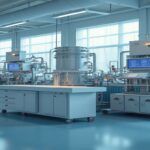
Design & Manufacture of Laboratory and Semi-Industrial Equipment
آذر ۷, ۱۴۰۳Introduction
Recent advances in Artificial Intelligence (AI) have significantly impacted various fields, including process engineering. This paper provides a systematic overview of AI applications in process engineering, classifying current applications and techniques. The paper highlights the importance of combining AI with mechanical models to leverage the strengths of both. It also outlines a comprehensive strategy for utilizing AI in process engineering, emphasizing the potential to improve process efficiency, optimize operations, and accelerate innovation.
The directly related fields of activity in process engineering include “process design”, “process control”, “process operations”, and “supporting tools”, as shown in Table 1.
Figure 1: Fields of activity in process engineering along with their respective tasks and major achievements
Beyond engineering aspects, process economics also plays a significant role in this field. In other words, analyzing the costs and benefits of various industrial processes is also part of process engineering. Each of these fields (engineering, economics, etc.) is divided into numerous sub-branches and encompasses diverse tasks. For instance, product lifecycle management, performance evaluation of a process, and managing potential risks are among these tasks.
The core concept of process engineering is similar to chemical engineering. However, process engineering covers a broader spectrum of industries. From the production of pharmaceuticals and food to heavy industries like metal and cement production, all benefit from the principles of process engineering. Process systems engineering (PSE) is also a branch of process engineering that examines the entire production system and the relationships between its various components.
Table 1 shows some of the most important areas of activity in process engineering and recent advancements in this field. Process engineering operates on different time and spatial scales. For example, the supply chain of a chemical product consists of various stages, each requiring its own models and parameters.
Artificial Intelligence
Artificial intelligence (AI) has been studied since the 1950s as the science that gives machines the ability to learn and solve problems like humans. Today, two main subfields of AI have attracted the most attention: machine learning (ML) and deep learning (DL). Machine learning (ML) refers to a set of methods that allow computers to learn and make predictions from data without being directly programmed.
Deep learning (DL) is a subset of machine learning that uses artificial neural networks (ANNs) to learn complex patterns in data. These networks have multiple layers that allow them to extract complex features from data.
Figure 2 shows that interest in machine learning and deep learning has grown dramatically in recent years.
In Figure 3, the concepts of artificial intelligence (AI), machine learning (ML), and deep learning (DL) and the dependencies between them are illustrated. The methods dedicated to the respective paradigms are also listed along with application examples.
Application of Artificial Intelligence in Process Engineering
The number of published papers on the use of artificial intelligence algorithms in mechanical and process engineering has increased dramatically in recent years. Based on a review of the relevant papers, the described applications in process engineering can be categorized into the following main objectives: data correction, predictive process modeling, process optimization, fault/anomaly detection, process control, and mechanical model extraction, which are schematically shown in Figure 6.
Among these six objectives, process predictive modeling, process optimization and control, and fault detection directly fall within the shared domain of process engineering and artificial intelligence. Data correction is a preliminary process for data preprocessing, usually performed before the main stage of AI training. Among these, predictive modeling is considered the most prominent objective and often plays a key role in other applications as well. This modeling typically serves as an intermediate or initial step in the overall process and provides a foundation for subsequent stages such as process optimization, process control, fault detection, or mechanistic modeling.
Mechanistic modeling holds a special place in this framework, as its primary goal is to transform data-driven and empirical trained models into transparent (white box) mechanical or physical models that are more interpretable and analyzable. This process involves the use of reverse engineering methods on black box models. Hybrid or gray box models are also used to achieve mechanistic modeling.
The main focus is on selecting key features and methodological strategies to provide a roadmap for readers to adapt and transfer these to other applications in the field of process and mechanical engineering, as well as in other engineering fields.
Predictive Modeling
An example of the use of machine learning (ML) as a predictive model in process engineering is provided by Geng et al. They used a two-stage method to train an artificial neural network (ANN) to predict a chemical reaction process in a complex system consisting of a column, a reboiler, and a return tank.
As shown in Figure 7.
In the process under investigation, pure terephthalic acid is produced in a plant consisting of a solvent dryer column, a recycle tank, and a reboiler. A total of 17 input parameters such as return water flow, inlet flow and composition, additional flows, temperatures at various plant locations, and the level of the recycle tank were used with the acid content output from the plant as the output parameter.
Before the actual training of the ANN as a predictor, a preliminary autoencoder (AE) was integrated to extract the main features (also known as dimensionality reduction) from the training data. By reducing redundancies and noise, the efficiency and stability of subsequent AI modeling were increased.
Based on the identified features and acid content data, an ANN, a Extreme Learning Machine (ELM), was trained to accurately predict the process outcome. ELM is characterized by randomly setting the parameters of the hidden layers to avoid local minima in the gradient descent process.
Process Optimization
Zhang et al. demonstrated the process optimization tasks using machine learning (ML) capabilities through two examples. In the first case, a hybrid model was trained for a continuous stirred-tank reactor to simulate the process of a reversible and exothermic chemical reaction. Here, the artificial neural network (ANN) was trained to replace the first-principles-based reaction rate equations in the mass and energy equations; equations that are very difficult to obtain without a detailed knowledge of the underlying reaction mechanisms.
Based on these hybrid models, cost functions for Real-Time Optimization (RTO) and Model Predictive Control (MPC) were designed to maximize economic efficiency and determine optimal setpoints for controllers by using trained neural networks as replacements for first-principle-based nonlinear functions.
In the RTO related to the stirred-tank reactor, cost functions were designed for reactant conversion and heat cost and optimized considering the total cost and AI models trained for reaction rates. Similarly, for the distillation column, an objective function was designed for profit that depended on the process products, feed, and energy.
Process Control
As explained in the previous subsection on process optimization, Zhang et al. [26] developed hybrid predictive models for a stirred-tank reactor and a distillation column that were coupled with process optimization. Based on RTOs containing AI-based hybrid models, separate MPC strategies were extracted. In these cases, process control was tuned in a conventional manner using a Lyapunov-based model predictive controller. This controller adjusted the inputs to reach the steady state predicted by the RTO.
For the dewatering column, optimal RTO parameters were transferred to six control loops (parameters such as flow rate, pressure, and RTO values for temperature and concentration controllers) to set the appropriate process conditions. In these two cases, AI was used for hybrid modeling of physical processes, and then optimization and control strategies were applied using conventional approaches. Alternatively, the entire control process could be implemented using AI.
Conclusion
This study has investigated the current status and potential applications of artificial intelligence, particularly machine learning, in the field of process and chemical engineering. It began with a brief introduction to the field of process and chemical engineering, examining its areas of activity, tasks, and future potential. The concept of artificial intelligence was then introduced. This article has highlighted the increasing capabilities of artificial intelligence due to advancements in software, hardware, and the emergence of AI platforms. This indicates the growing importance of artificial intelligence on a global level and also in the field of process and chemical engineering.
For downloading the article, you can use the following link: